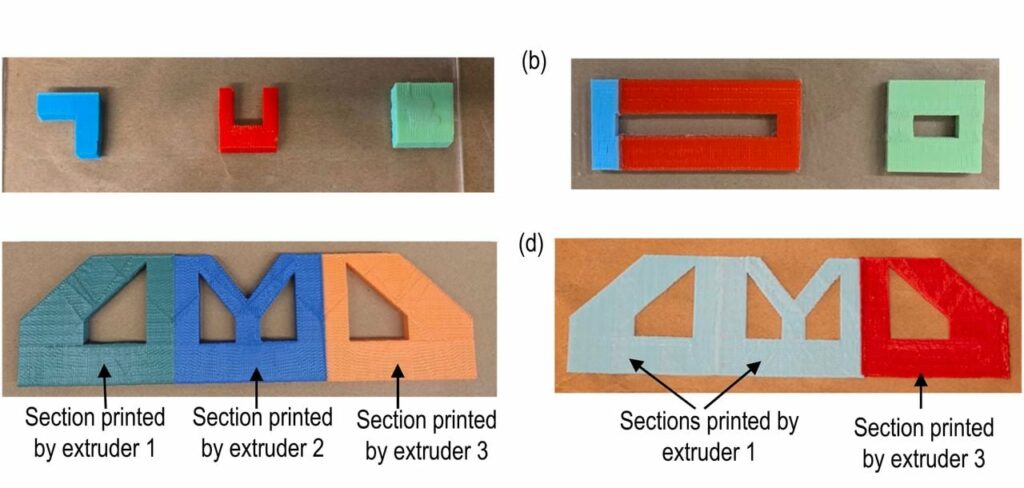
Researchers have developed a unique and very powerful FFF extrusion technology they call “MF3”.
The research team at Rutgers wanted to find a way to overcome one of the deepest problems in 3D printing: the tradeoff between print time and print resolution.
Most 3D printers have confronted this dilemma simply by choosing between “Draft” and “Detail” slicing options. The idea is to either print fat extrusions to complete the print quickly but with coarse layers, or print far more small extrusions to get fine detail at the cost of more print time.
There have been attempts to solve the problem with hardware, too. A very common solution is to use FFF nozzles with a wider diameter. While a 0.4mm nozzle is standard, a 0.8mm nozzle can dump 4X as much material. But then you lose the resolution.
Multiple extruders have also been attempted, but normal this isn’t done for print speed: it’s usually for multiple materials or printing copies of identical parts. Dual independent extruders can print more than one object at a time, which is faster, but can’t help each other on a single object due to the overwhelming complexities of managing the motion system.
How MF3 Works
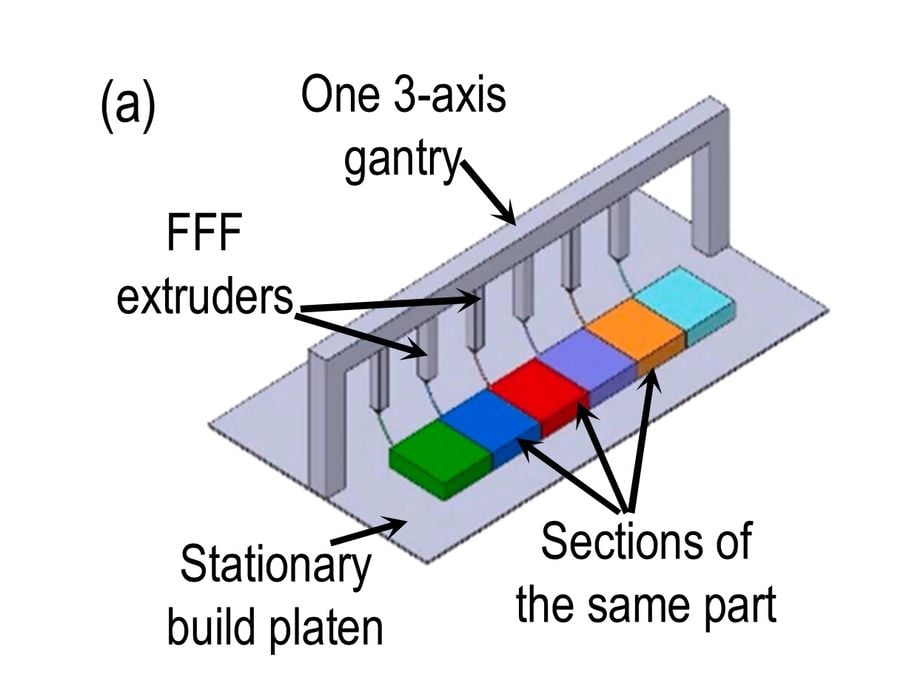
Enter MF3, which is a revolutionary concept for overcoming this problem. Here’s how I understand it works:
Imagine a single gantry upon which is mounted multiple standard extruders. These extruders would all move in sync as they are attached to the same carriage on the motion system.
Now let’s consider how a layer is 3D printed with this configuration with MF3.
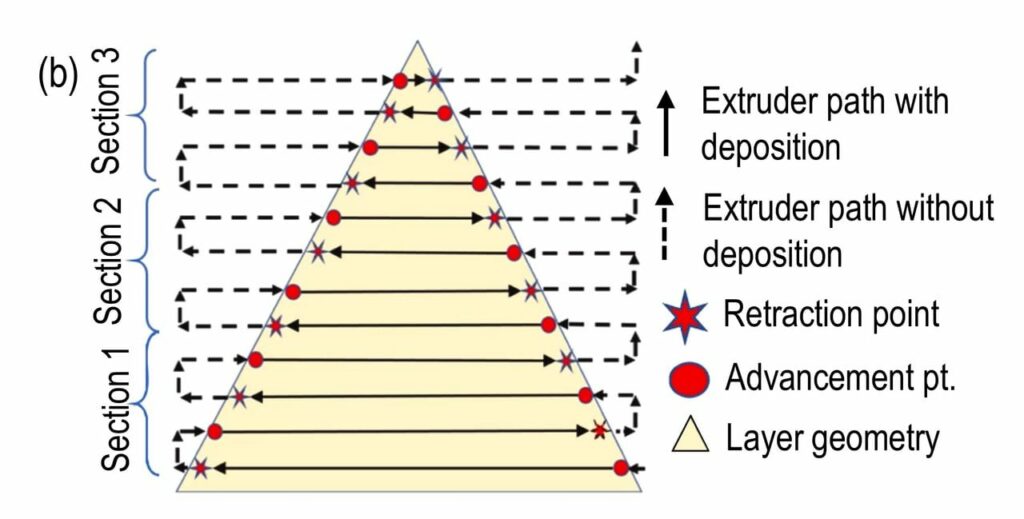
For each layer, a bounding rectangle is identified that encloses all solid portions of that layer.
The MF3 slicer creates a toolpath (shared by all extruders) that causes nozzles to move overtop of each part of the bounding rectangle in a raster-like pattern. The toolpath ends up with each nozzle “covering” a certain section of the layer.
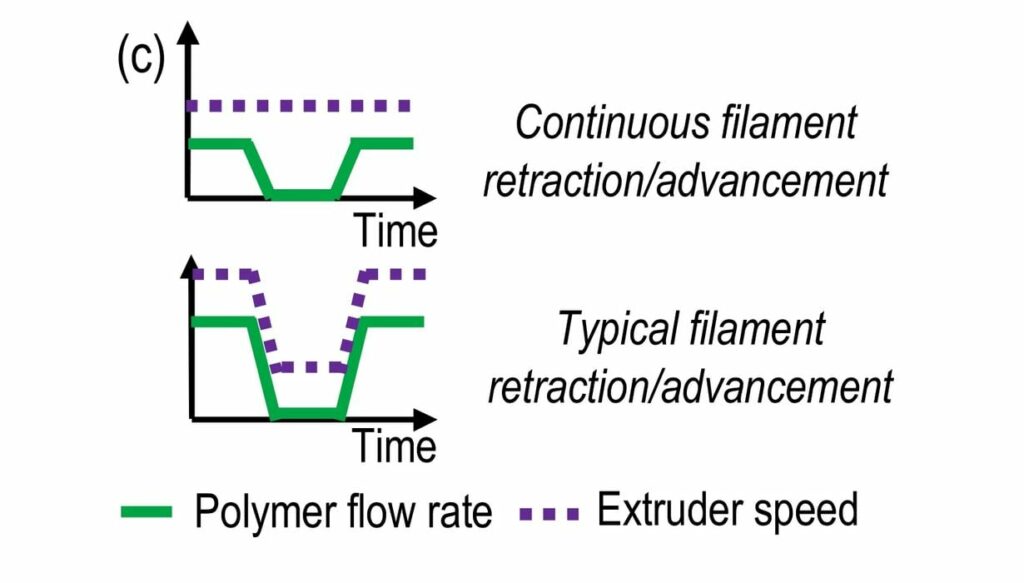
As the layer’s GCODE is executed, the extruder motors are running continuously — either extruding or retracting. The switchover between those motions is determined by whether that extruder is required to extrude over that point in the layer.
Visibly you’d see the extruder complex sweep over the model back and forth — no curvy motions — and as it does the extruders are “on” or “off” as required to deposit material in the correct locations.
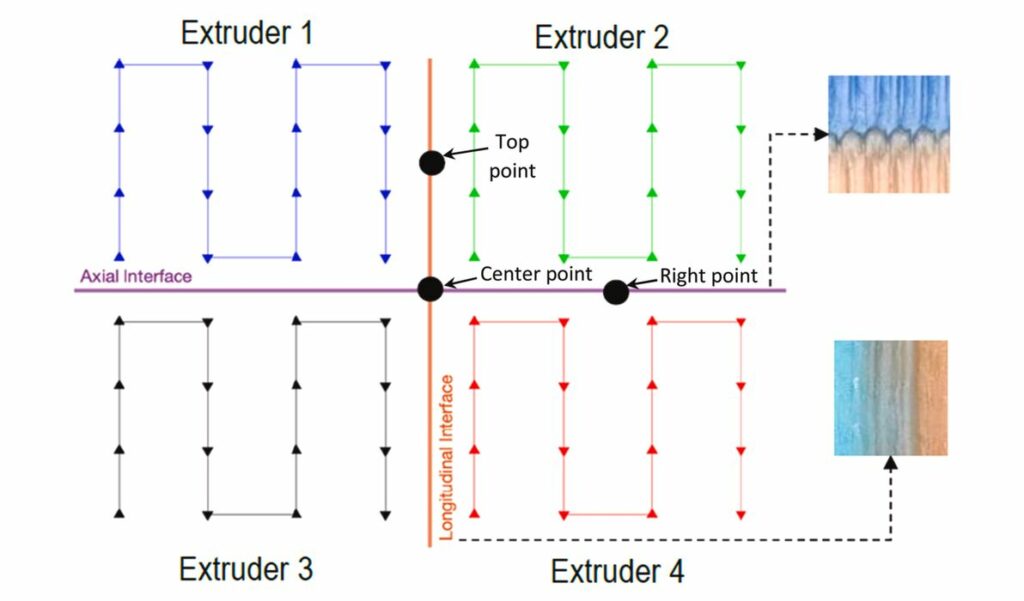
The result is a system that is using multiple extruders simultaneously and thus overcomes the resolution-time barrier. It can print large objects using all print heads, or print multiple smaller independent objects.
There are multiple advantages to this approach beyond reducing print time:
- Theoretically, a non functioning extruder could have its job load taken on by working extruders by adjusting the GCODE appropriately
- Many extruders could be added — more than two or even the three used by the researchers
- Extruders could be arranged in a matrix, say a 3×3 9 extruder configuration, instead of the traditional “in-line” layout
- Only one carriage is required on the motion system, as opposed to complex dual independent arrangements
This would appear to be a style of hardware that could be implemented at relatively low cost: you’re just adding some extruders to the existing motion system. The magic is in the software that generates the toolpath.
Thoughts On MF3
While this is definitely revolutionary and absolutely will show up in commercial products, I do have some concerns.
The print time is indeed reduced on many prints, but as you continue to add extruders, the savings effect diminishes.
I wonder if there are geometries that are pathological to MF3. What if you had a spindly 3D model where there wasn’t much to print on each layer, which is an increasingly common scenario based on today’s generative design? Would there really be much speed up, as there would be a wait time to ensure the prior layer has solidified.
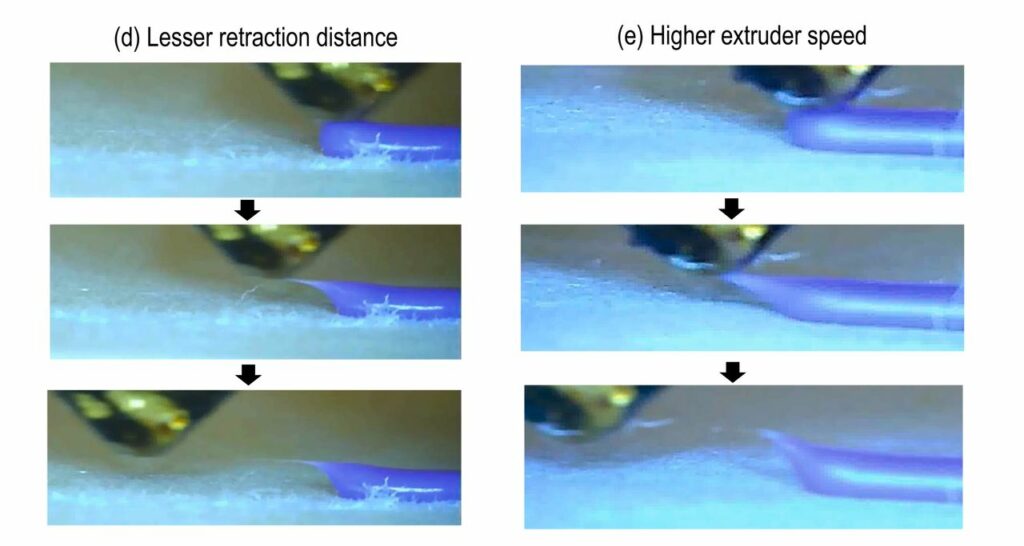
As you might imagine, the surface quality of the parts will be terrible, because you will frequently see the “ends” of the extrusions on the surfaces as the raster movement proceeds through each layer. It would be similar to having the normal layer “seam” literally everywhere.
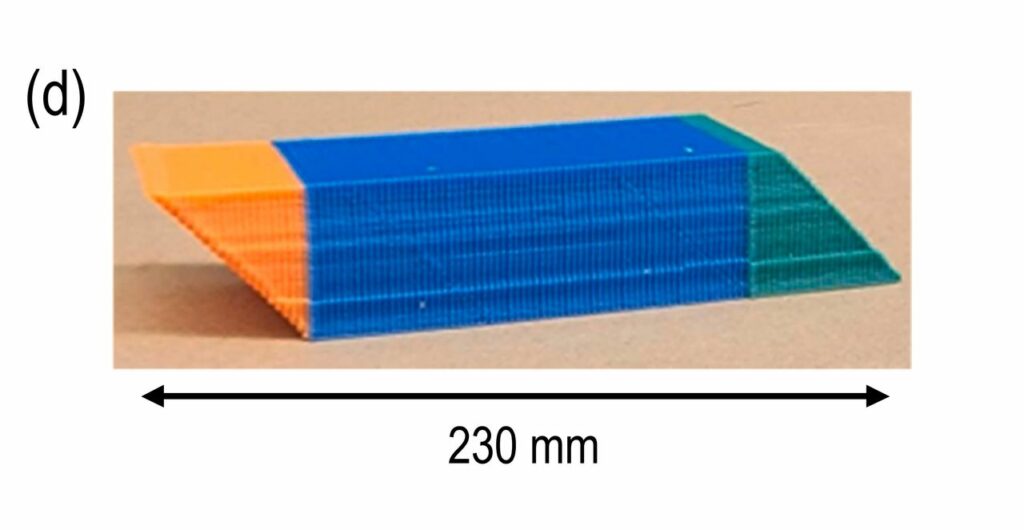
One way to overcome this might be to ensure the slicer adds a standard curvy set of perimeters to each layer. That would be an easy solution.
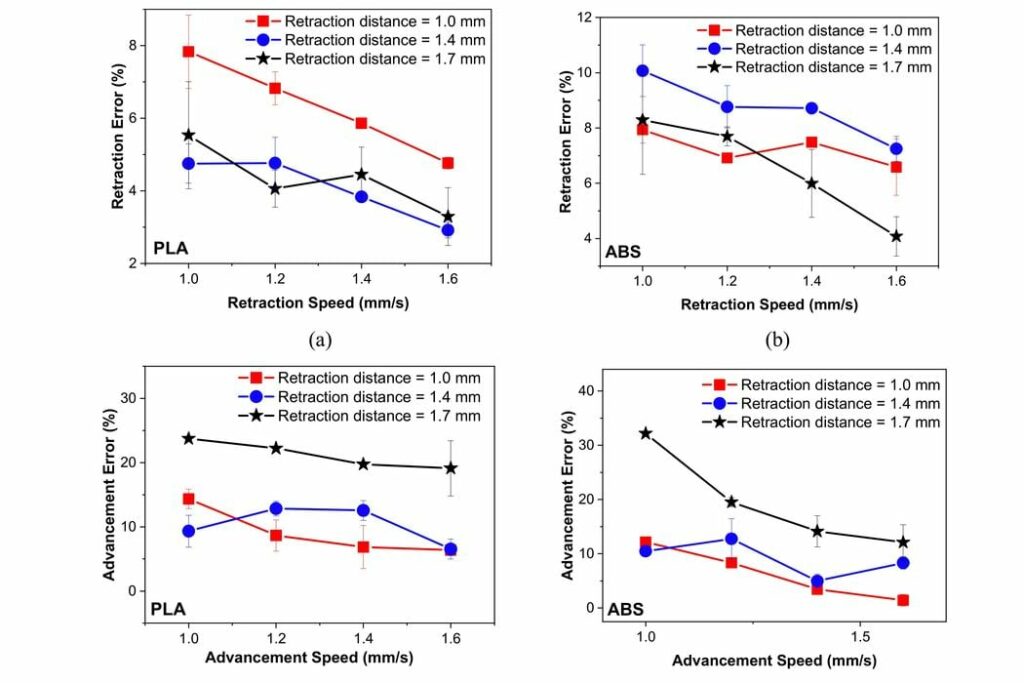
The researchers are aware of this, and spend considerable time in their paper tuning the retraction speeds to minimize this effect. See the charts above showing some of this work, and the equation used for pixel heat transfer below:

A more tricky issue to solve might be the notion of reinforcing areas. For example, some advanced slicers might do extra perimeters around bolt holes to make them stronger. But that kind of movement doesn’t seem to be in MF3’s playbook.
The researchers intend on performing strength tests of MF3 printed parts in upcoming work, so we’ll no doubt find out more then.
MF3 is certainly revolutionary, but clearly requires some additional investigation and development before it could appear in commercial products. But because of its incredible benefits and likely efficiency, I am certain those will be overcome.
Via ScienceDirect