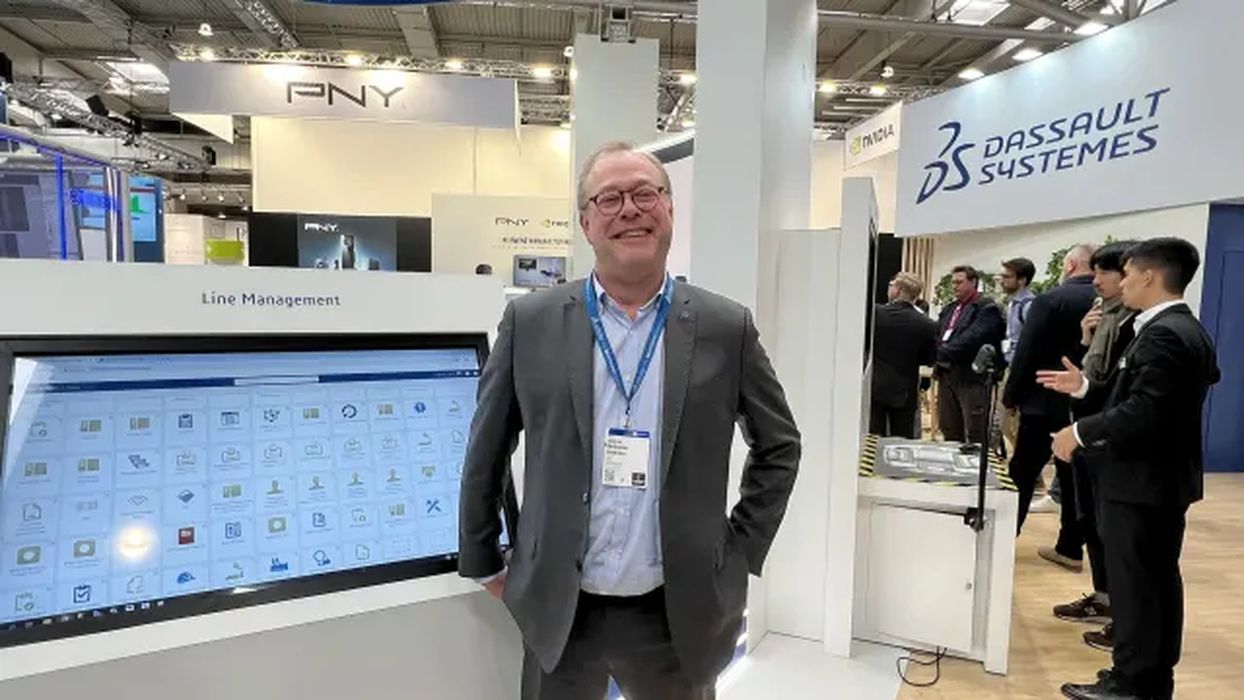
Dassault Systèmes’ Delmia CEO explains the benefits of virtual twins in a challenging business environment. One of them might surprise you.
At this year’s Hannover Messe trade fair in Germany, I had the chance to chat with Guillaume Vendroux, CEO of Delmia, the digital-manufacturing software arm of Dassault Systèmes. Vendroux said that changes are coming fast in the world of manufacturing and operations, and three factors threaten today’s industry.
“First, there is the trend of mass customization. We are all responsible for that when we buy products on Amazon,” he said. “People want products that are very, very close to their needs, and they want to be able to customize them. The first problem our manufacturing people have is that they have a massive amount of highly diversified products. This is not good; it is really complex.”
“Second, what we saw during COVID times is that [the mass-customization issue] hasn’t been solved, particularly on the supply chain side.”
Vendroux noted that if you add in the volatility of the energy market and continued political uncertainties, there is more and more pressure on the supply chain.
“Third, in manufacturing and operations, because of COVID, we see people getting less and less attracted to that space at work. We are lacking talent,” he said.
Vendroux likened manufacturing in the past to being in the army — a generally unattractive world in which it could be difficult for a young person to develop and grow.
Modeling twins
“We have a need for speed and agility in that very difficult environment. At Dassault Systèmes, the way we approach this is what we call the virtual twin experience,” he said. “When you want to tackle a very difficult problem, when you are a scientist, the first thing you do is try to model the problem. Modeling is the first pillar of a virtual twin. That means we can model a station, a line, a shop, a full supply chain, and we can play around with it, trying to understand the problem it may face and trying to optimize it.”
Eventually, Vendroux said, users can validate the way things should work — but by validating them virtually to avoid losing time or making mistakes in real life. Through modeling, manufacturers gain a unique and optimized plan to execute.
“The problem of operation is that a plan is good, but execution is better. So, we’re going to take that plan and push it to the real world. In doing that, we’re going to connect to the virtual and the real. That means data will begin to flow from the shop floor to the model to do two things.”
“First, if you look at data just like this, you will not understand the data. To understand the data, you need to project it to a model, some kind of projection. For example, if I give you GPS data, you don’t know where you are. If I give you the GPS data and the map (the model), then you know where you are. So, if we have the model and we can project data, we understand perfectly well — and our clients understand perfectly well — where they stand, what the topics are, and what they need to do.”
The second thing, he noted, is that models can be predictive.
“If you feed data into models, then you can see into the future, you can anticipate things. And we all know that anticipation, at least in operations, is the key to success because this drives agility,” Vendroux said.
“The third topic, especially now with the emergence of AI technology, is data associated with the model — the plan versus the realization. It is a perfect way to learn and to improve our capacity to better model and be more accurate. Thus, by connecting the virtual and the real, you have a system that tells you exactly where you are, projecting the future. And it is a learning system, which is better and better the more you use it.
“You have quality people, you have finance people, you have manufacturing people, you have engineering people — you have so many people. So, to make a decision, you need to somehow tap into the collective intelligence of the team. And that’s what collaboration and the 3DExperience platform is doing.”
Vendroux said that Dassault Systèmes is uniquely positioned to unite those three pillars because of its 3DExperience platform, which not only hosts but also interconnects many of the company’s software, thus facilitating the end-to-end integration of engineering, manufacturing, supply chain and aftersales.
Read the rest of this story at ENGINEERING.com