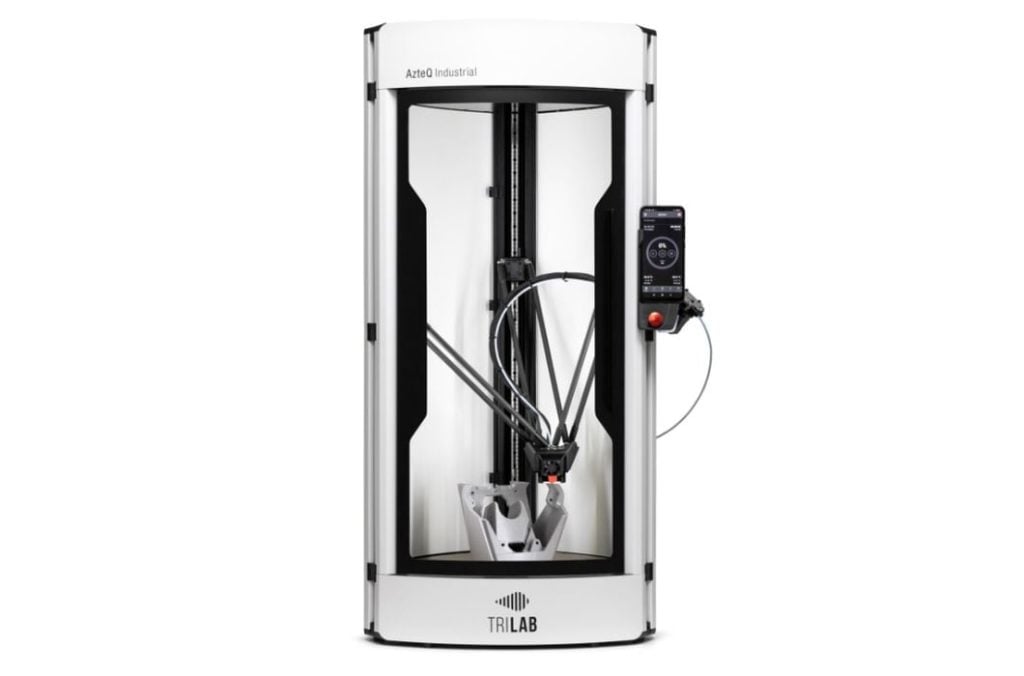
SPONSORED CONTENT
Trilab has launched AzteQ, a powerful new family of delta 3D printers.
While their original open gantry-style DeltiQ 2 device continues to be produced, there are several useful concepts Trilab introduced in the DeltiQ 2 that carry on in the new AzteQ line, which focuses on different materials.
Learning from DeltiQ 2
The Czech company has always produced delta-style 3D printers and has developed some very interesting features for them. When I looked at their previous machine, the DeltiQ 2, I found they had discovered a way to successfully 3D print flexible filaments on a delta system.
Their solution then was to use the radical Nimble extruder from Zesty, which transfers power to the print head using a rotating solid cable. This allows a delta motion system to use a direct extruder, rather than the flexible-challenged Bowden extruders.
However, thereâs a bit of a change on the DeltiQ 2 in recent times: Trilab found they were no longer able to source the Nimble extruder from Zesty, so they redesigned their own âFlexPrintâ extrusion system that offers improved capabilities.
The current version of the Trilab-owned extruder is named the âFlexPrint 2â, and it is capable of 3D printing flexible materials as soft as 70A. This holds for even large objects, because the motion system of the DeltiQ 2 does not involve moving the build platform: the flexible prints-in-progress remain stationary and do not wobble.
AzteQ Design
The AzteQ is designed as a complementary device to the DelitQ. Where the DeltiQ 2 is designed for commonly used 3D printer materials such as PLA and flexibles (using FlexPrint 2), the AzteQ is focused on engineering materials, and uses a standard Titan extruder in a Bowden configuration.
The more advanced AzteQ 3D printer was recently launched after two years of development. The companyâs DelitQ experience provided a considerable amount of knowledge from industry, and that has been incorporated into the design of the new AzteQ 3D printer.
AzteQ 3D Printer Heated Enclosure
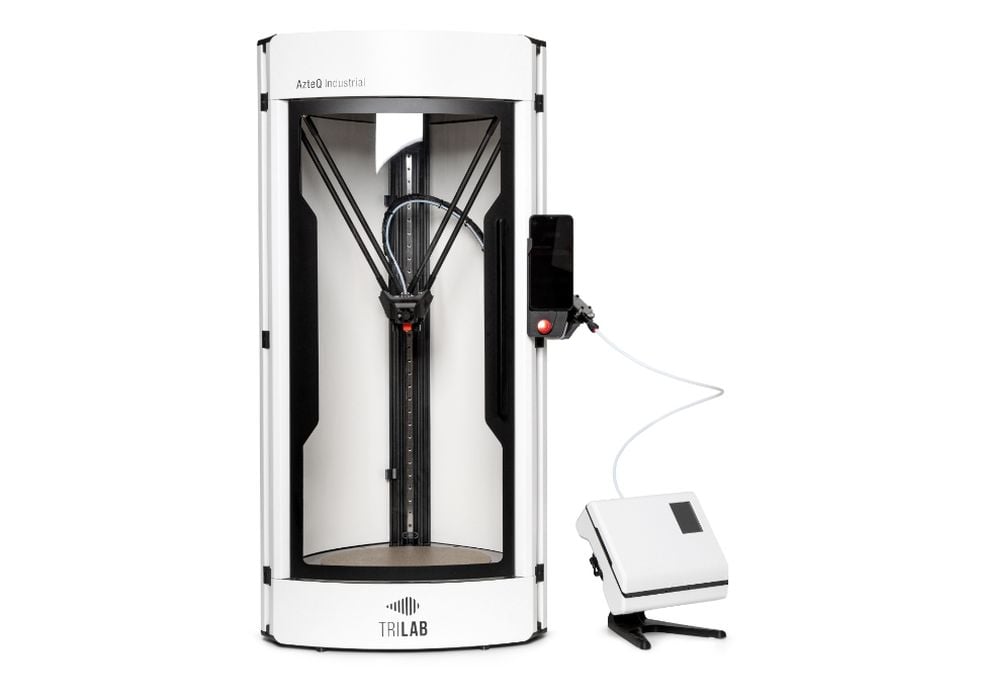
The AzteQ is, as you might suspect, a delta 3D printer, but it is an enclosed device. This is somewhat rare, as fully enclosed delta devices are not plentiful on the market.
In fact, the build chamber on the AzteQ is not only fully enclosed, but also thermally isolated from the electronics, which are actively cooled themselves with ambient air.
The enclosure allows the build chamber to be actively heated, up to 80C in only a few minutes. The heat is consistent throughout the build chamber by the continual movements of the delta motion system, and by the fans on the toolhead that move air around the chamber.
A heated build chamber is important because it enables proper 3D printing of a wide variety of engineering materials. Trilab said the AzteQ is able to 3D print challenging materials like ABS, ASA, PA, PC, PP as well as more standard materials such as PLA, PETG and CPE.
Many typical engineering materials, such as ABS, ASA or nylon tend to warp due to the thermal gradient that occurs after extrusion. While some 3D printers attempt to overcome this effect with a heated build surface, the AzteQ instead heats the entire chamber. This means that ALL printed layers are thermally identical throughout the print job, and thus geometric distortions are minimized.
Because of this it is possible to 3D print dimensionally accurate 3D prints on the AzteQ. Slicing parameters need only to expand the objects size appropriately, so that when completed and removed from the heated build chamber, the object uniformly shrinks to the correct dimensions.
I should point out that the design of the AzteQ moves the systemâs electronics (a 32-bit Duet board) outside of the build chamber. This is a critical design feature, because systems that happen to mount electronics within the heated environment can suffer heat damage. That wonât happen on the AzteQ.
The AzteQ does have a heated build surface to ensure adhesion of engineering materials, but itâs a bit different from the standard approach youâd see on most 3D printers. Instead of a simple heat plate, the AzteQ includes a massive 8mm thick aluminum plate that ensures very even thermal transmission.
On top of the heated aluminum plate the actual print surface is a removable sheet. These âPrintPadsâ are flexible steel and magnetically attached, making it easy to remove prints with a twist. Trilab offers several different PrintPads to account for different material adhesion properties, and I expect they may add more in the future, including a glass version.
AzteQ Features
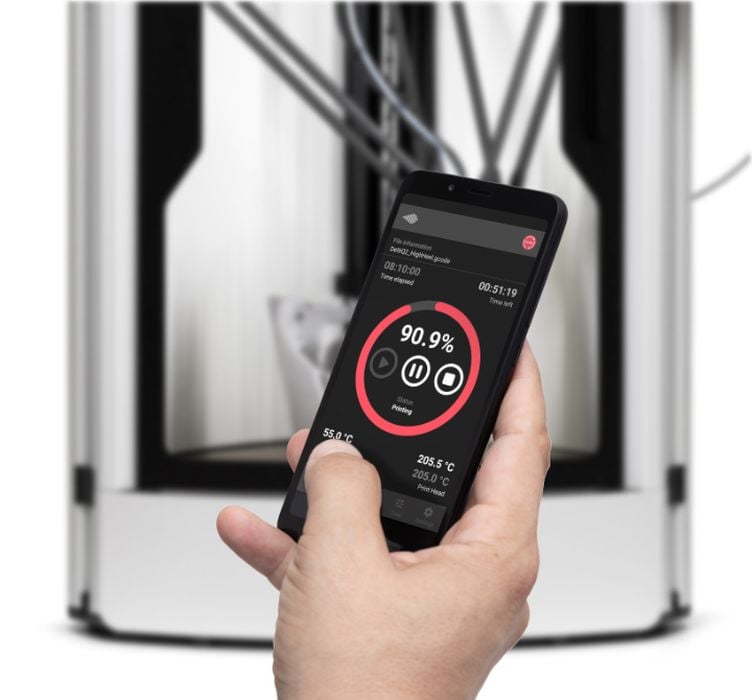
The AzteQ includes another very interesting feature: quick swap printheads. The printheads are attached magnetically, so it is very easy to change them. After changing, the AzteQ will automatically calibrate them so they are almost immediately ready for use and is done using Duetâs tensometric process to avoid any possibility of error.
Trilab currently offers three different printheads: E3D-Onlineâs V6, Volcano and SuperVolcano, all of which come with excellent reputations. In fact, Trilab offers any combination of V6, Volcano or SuperVolcano heat blocks, heatsinks, nozzles or other components. Each Trilab printhead is coded so that the AzteQ always knows which tool is currently installed, and weâre told they test all combinations. For AzteQ operators, it means the printer can be quickly adapted for a given print job by simply selecting an appropriate printhead.
Trilab has spent considerable effort to enable the AzteQ for remote operation. The device includes internal build chamber lighting, an on board camera, WiFi network connection, connectable external USB camera. Using these combined technologies, Trilab provides a web access page to monitor and control the AzteQ – both on local networks as well as remotely via secure link.
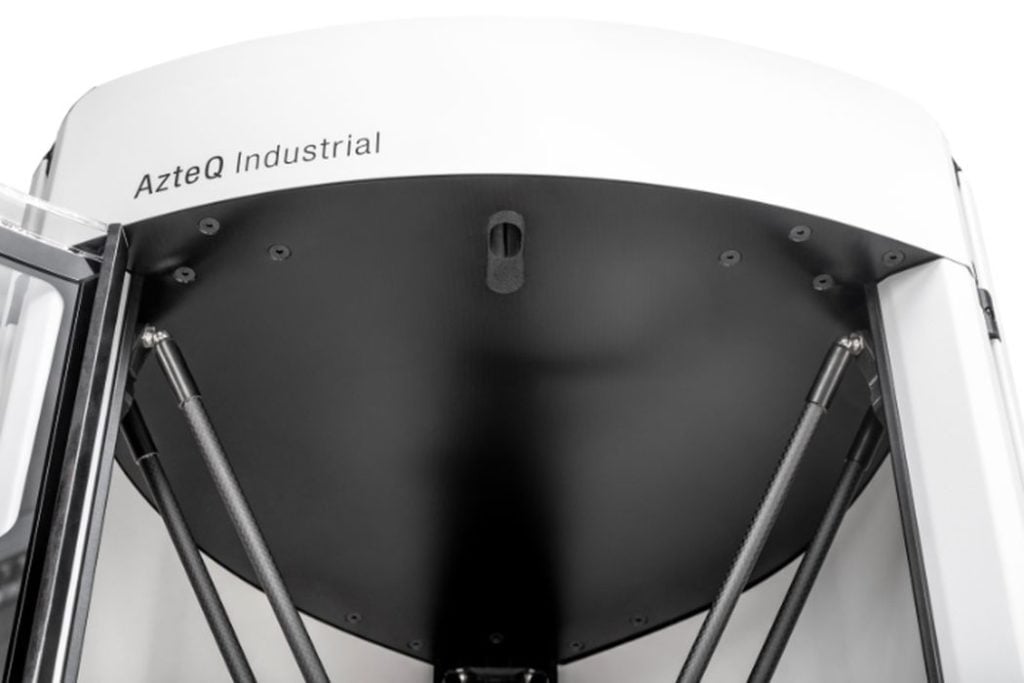
This remote operation is more useful than you might think, because it can be leveraged during support situations. Trilab provides complete coverage of the Azteq through their support team, using email, voice and chat interfaces. But because the AzteQ (and DeltiQ 2) can be remotely controlled, it is possible for the support team to assist with firmware and software upgrades more easily.
Physical control of the AzteQ is similar to the DeltiQ 2: an Android device connects to the printer via Bluetooth, and the Trilab app provides a control interface. Jobs may be stopped, started and monitored visually using the on board webcam. The app can also be run from the operatorâs own Android device if required.
Trilab also offers an optional method of 3D printing with multiple materials. Their âQuadPrintâ option will support up to four different input filaments to print using the single printhead on the AzteQ. This is a Mosaic Manufacturing Palette 2S or Palette 2 S PRO specifically configured for the AzteQ.
The AzteQ is a large delta machine, with a build volume of 300mm wide (cylindrical) and 400mm tall, and if thatâs not large enough for your application, the company also offers the AzteQ Plus, which has a 400mm diameter and whopping 600mm Z-axis.
The enormous build volume will enable 3D printing of large objects, which could take many hours or even days to complete. Trilab said the AzteQ is fully capable of operating for long periods, and the remote monitoring capability is of particular value during those long jobs.
AzteQ configurations start at âŹ7,999 (US$9,400) and up, depending on options. Trilab wants to make the best delta 3D printer in the world, and they may indeed be doing just that.
Via Trilab