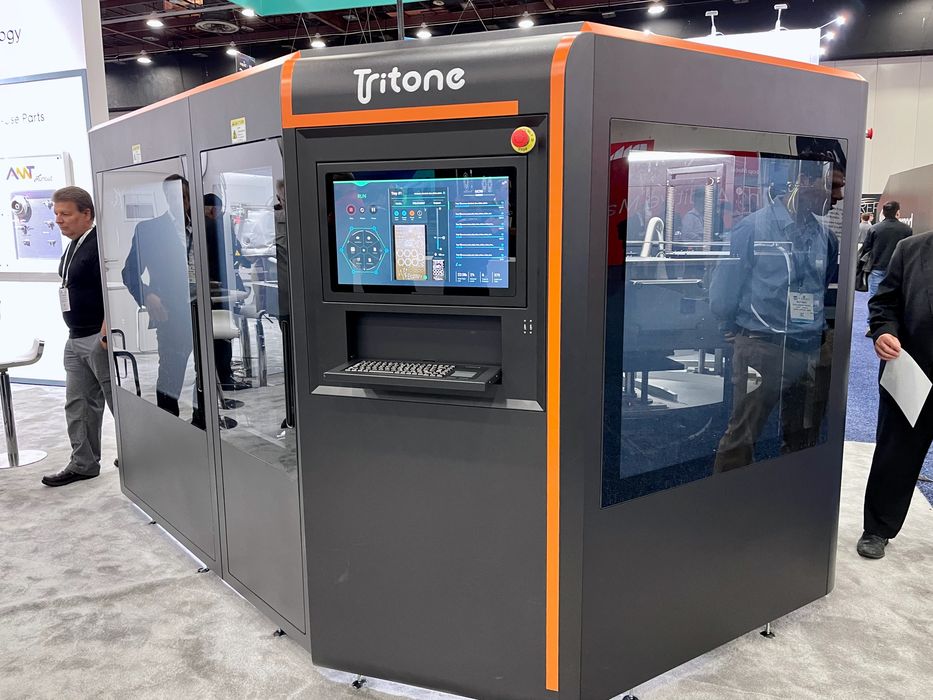
I had a look at the latest from Tritone.
Tritone is an Israeli 3D print startup, founded only five years ago. They’ve developed a very unusual 3D printing process called “MoldJet”, and deployed it in two different 3D printer models, the huge “Dominant”, and the somewhat smaller “Dim”.
Their MoldJet technology is really quite interesting. It combines standard MIM (metal injection molding) technology with advanced 3D printing technologies.
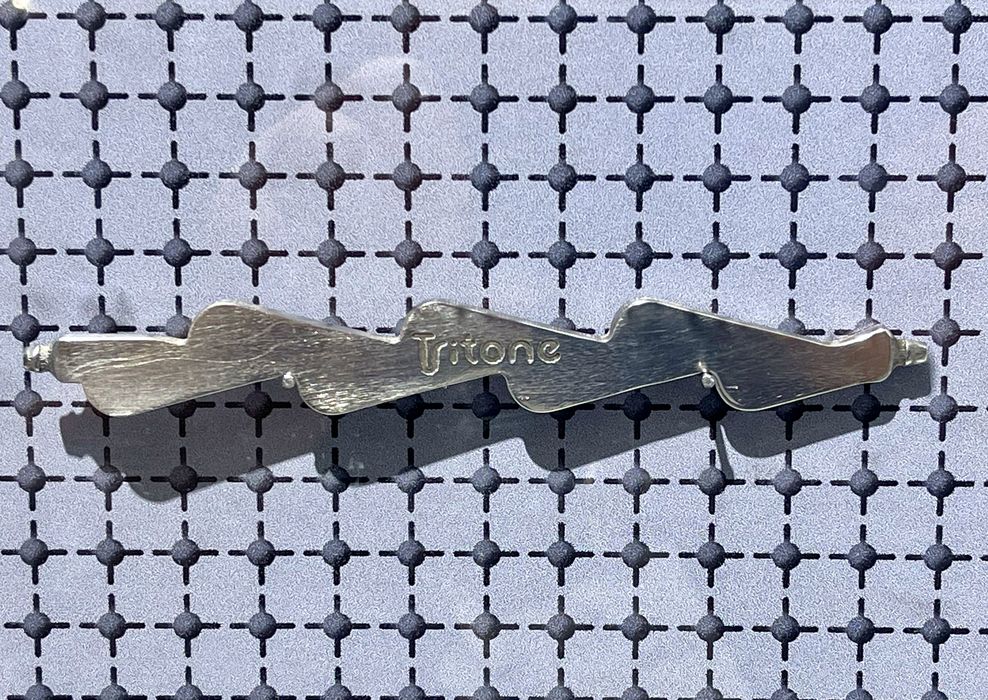
MoldJet does two things: it 3D prints a mold, but at the same time fills the mold with a desirable material. This is done layer-by-layer.
A first pass by a high resolution inkjet system selectively deposits the mold material in the appropriate pattern. Then, before moving on to another layer, a second pass deposits the model material into the thin void created by the mold portion of the layer.
This process repeats, layer by layer, until you have completed the full 3D object — both mold and model material.
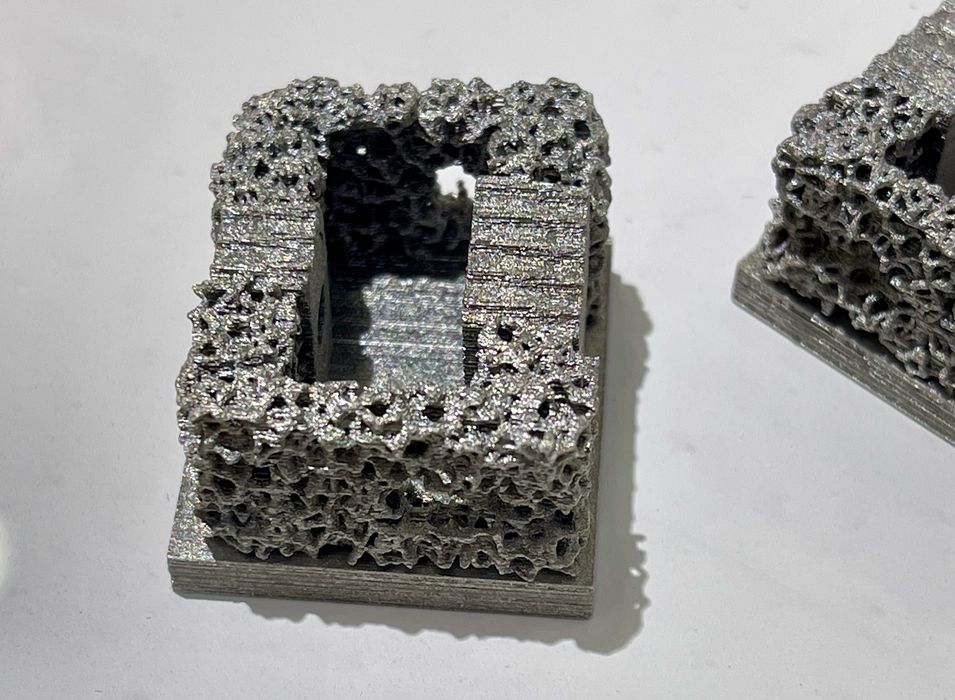
The wax-like mold material is removed through a heating process that takes a couple of hours to complete, leaving “green” parts made of the model material. These are then sintered in a furnace to finalize the metal parts. The process of sintering does shrink the parts somewhat, typically 15%, so parts must be designed to be printed in larger dimensions.
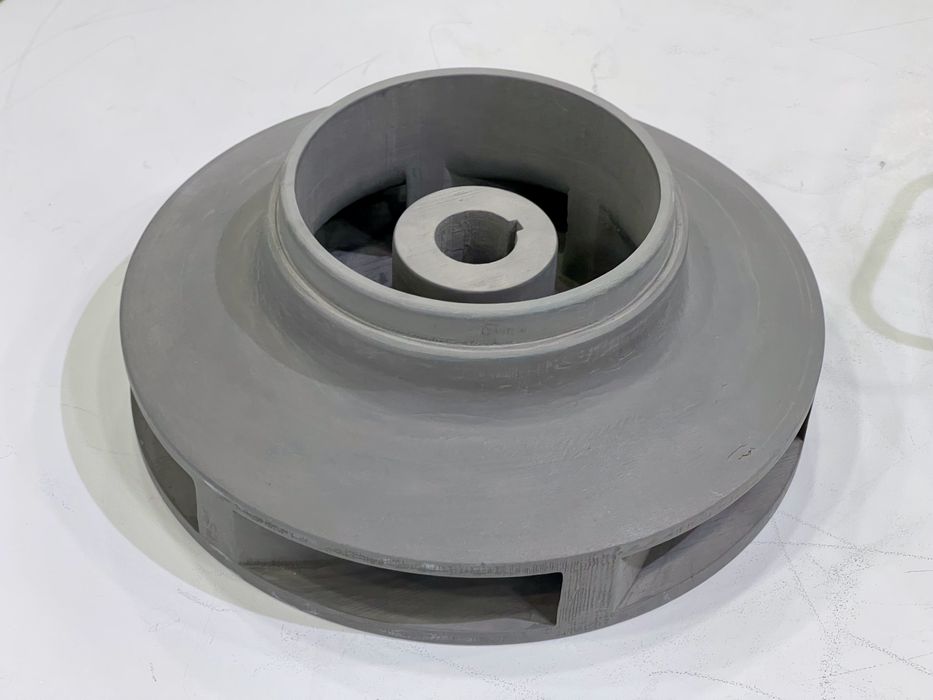
Sintering can be done by the operator if a suitable sintering furnace is present, or by outsourcing that step to others. Unfortunately, the Tritone machines do not themselves contain or come with a sintering furnace.
Tritone is now able to handle the following materials, all of which are provided in sealed cartridges for safety reasons:
- Stainless Steels: 316L, 15-5 PH, 17-4 PH, 420
- Tool Steels: M2, H13, 4340, 4140
- High Temperature Alloy: Inconel 718
- Titanium: 6-4
- Copper
- Bronze
- Ceramics: Alumina, Zirconia
It’s a fascinating process that enables use of a wider selection of metal and ceramic materials than is typically found with metal 3D printers. Essentially they allow use of common MIM powders, and this suggests they could very well expand the list of available materials quite broadly in the future.
One very interesting feature enabled by MoldJet is the ability to inspect each layer as it is laid down. If the inspection shows a flaw, then the machine can actually physically slice off that bad layer and trigger a redo. This improves the quality and reliability of print jobs.
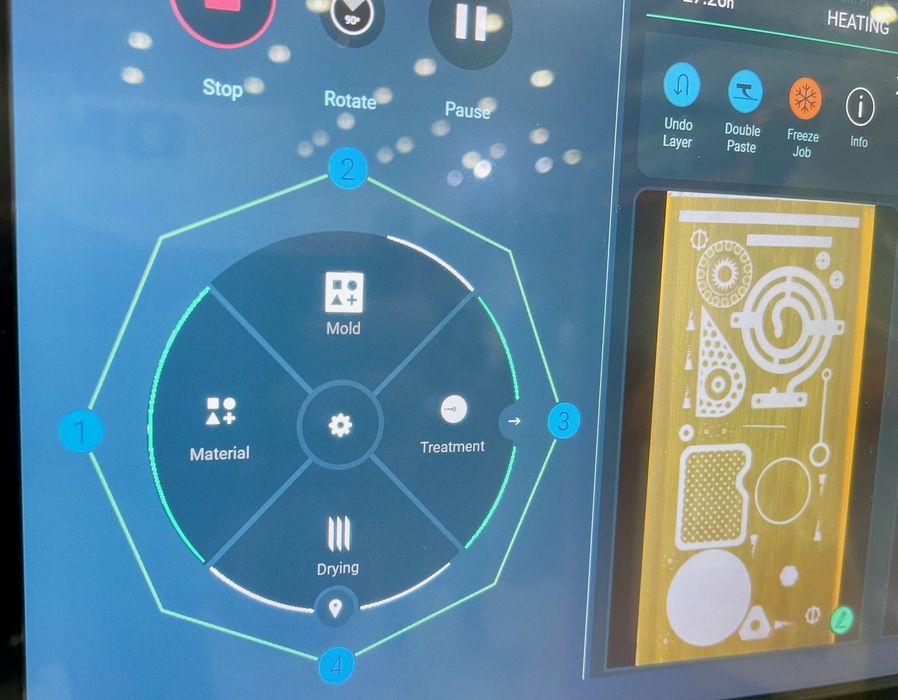
Tritone implements MoldJet in an unusual robotic system that carries print jobs through a series of different stages, all happening right inside the 3D printer. Above you can see a control panel showing the status of the different machine components, and below you can see a view of inside the machine where the print jobs travel in a circular path towards completion.
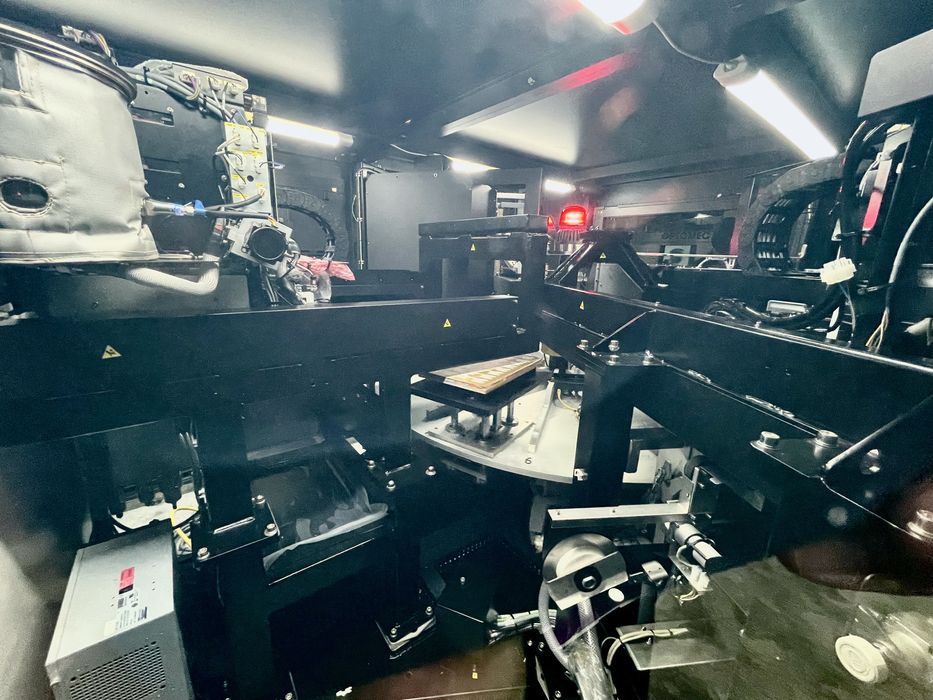
The build volume is 400 x 240 x 120 mm, but there can be six trays operating within the machine’s carousel system. This “pipeline” approach provides an ability to perform low volume manufacturing, as each tray produces another batch of parts.
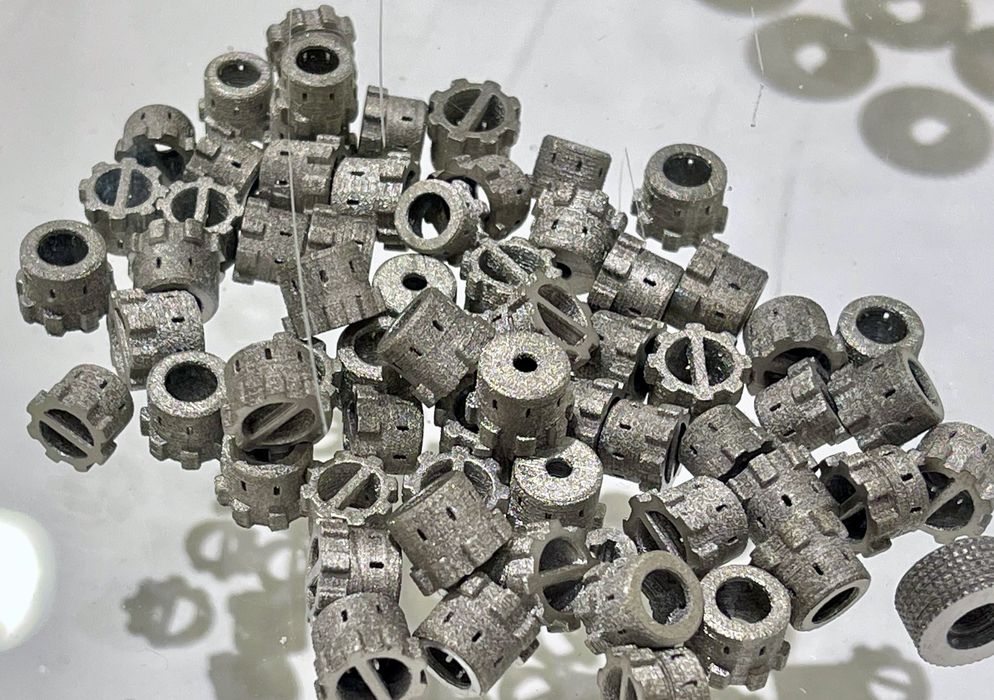
I asked about the difficulty of changing materials, which is quite troublesome in some 3D printers, often requiring so much effort that companies usually just get another machine to run a second material. This is not the case with Tritone’s system. Apparently you need only change a material tube and the machine is ready to proceed with an alternate material.
Tritone suggested the price of the Dominant machine would be in the US$320K range.
Via Tritone