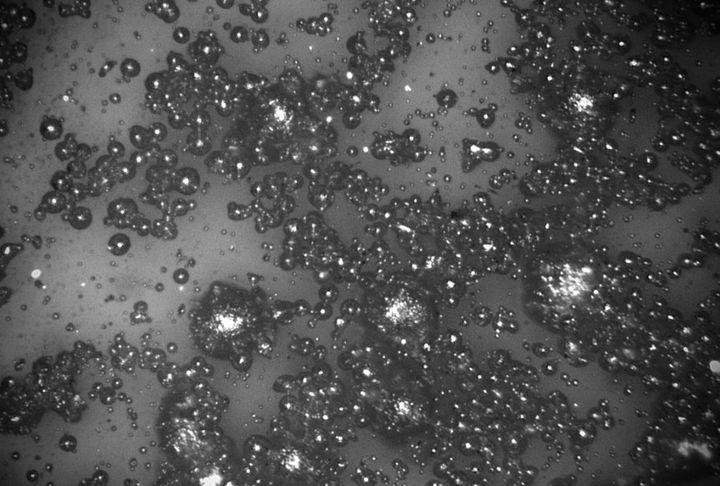
Desktop Metal and Uniformity Labs have developed Uniformity 6061, a powder that enables aluminum sintering for binder jetting.
From a startup touting mysterious plug-and-play metal additive manufacturing (AM) technologies to going public on the New York Stock Exchange five years later, Desktop Metal is achieving its mission and taking AM to new levels.
A multiyear collaboration with Uniformity Labs, an AM parts, printing and metal feedstock producer, has resulted in a new powder that enables sintering of unadulterated aluminum for binder jetting AM technology.
The new powder, Uniformity 6061, was the result of a combined goal to create a low-cost raw material option for dense, sinterable 6061 aluminum alloy parts. While 3D printing with aluminum may be nothing new, the options available have had their downsides.
The majority of aluminum alloys available were for direct energy deposition, melting or direct metal laser sintering, which often came with a higher cost, limited build size, additional waste and finished parts with a rough surface. Creating an option for binder jetting enables larger build volumes, fewer geometry restrictions, faster printing and smoother surfaces.
āThis breakthrough represents a major milestone in the development of aluminum for binder jetting and a significant step forward for the AM industry as it is one of the most sought-after materials for use in automotive, aerospace and consumer electronics,ā said Ric Fulop, CEO and cofounder of Desktop Metal. āThe global aluminum castings market is more than $50 billion per year, and it is ripe for disruption with binder jetting AM solutions.
āAccording to Desktop Metal, Uniformity 6061 has an elongation greater than 10 percent and provides both an improved yield strength and ultimate tensile strength when compared to wrought 6061 aluminum with similar heat treatments.
The ability to use sintering means that powder particles donāt have to be coated, additional metals donāt have to be added and expensive nanoparticles arenāt required. The new powder is compatible with water-based binders and has a higher minimum ignition energy (MIE), giving it a safer profile.
āThe introduction of lightweight metals to binder jetting opens the door to a wide variety of thermal and structural applications across industries,ā said Adam Hopkins, founder and CEO of Uniformity Labs. āThis innovation is a key step towards the adoption of mass-produced printed aluminum parts.ā
Read more at ENGINEERING.com