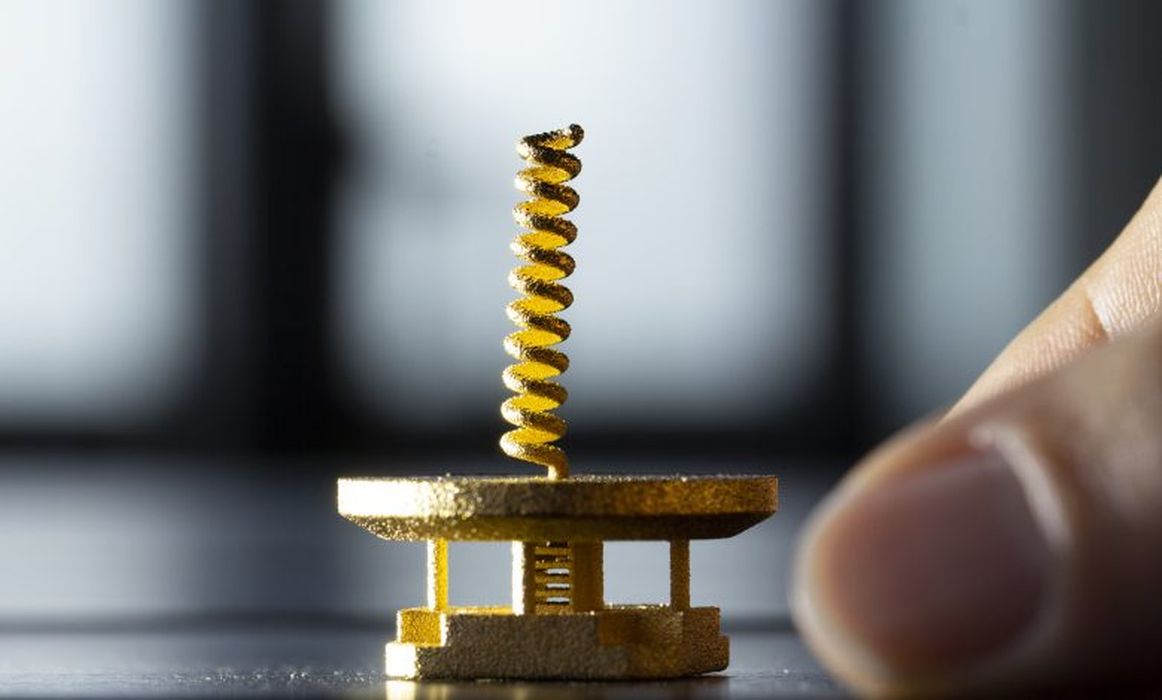
EOS’ latest polymer technology offers the durability and scalability of SLS and the precision and high-resolution of SLA.
German AM specialist EOS first revealed it had developed a new approach to selective laser sintering (SLS) back in 2019. At the time, we remember learning about the new technology, called Fine Detail Resolution (FDR), which made the exciting promise of offering “the detailed resolution of stereolithography with the durability and quality of selective laser sintering.” A few years on, and EOS’ FDR technology is now established on the market in the FORMIGA P 110 FDR system, and it is very much delivering on those promises.
What FDR offers
EOS’ FDR technology isn’t a million miles away from SLS: both technologies utilize lasers to fuse powder particles of polymer powder, building up parts layer by layer. Where FDR sets itself apart is in the use of CO lasers (as opposed to CO2 lasers, which are the common option for SLS platforms). CO lasers are capable of generating ultra-thin beams of about 200 µm, which EOS points out is about “half the size of what’s seen in SLS 3D printers.” This smaller laser size has an immediate impact on what users can achieve in their prints, particularly when it comes to fine details, thin walls and small features like lettering and microelectric connectors.
The CO laser is only a part of the FDR equation (albeit a big one), the technology also relies on a highly precise recoater, which distributes fine layers of powder rapidly (at a rate of 600 mm/s) and with even density. The combination of the CO laser and the recoating system have resulted in a dimensional accuracy of +/- 40µm, comparable to that of injection molding and SLA 3D printing.
On top of that are all the benefits typically associated with laser powder bed fusion processes, such as supportless builds (since the powder bed functions as a support). This significantly simplifies post-processing for FDR prints, as well as streamlines the design process and reduces material waste. In short, parts are ready for use after cooling and depowdering, though additional post-processes like coatings and vapor smoothing are possible.
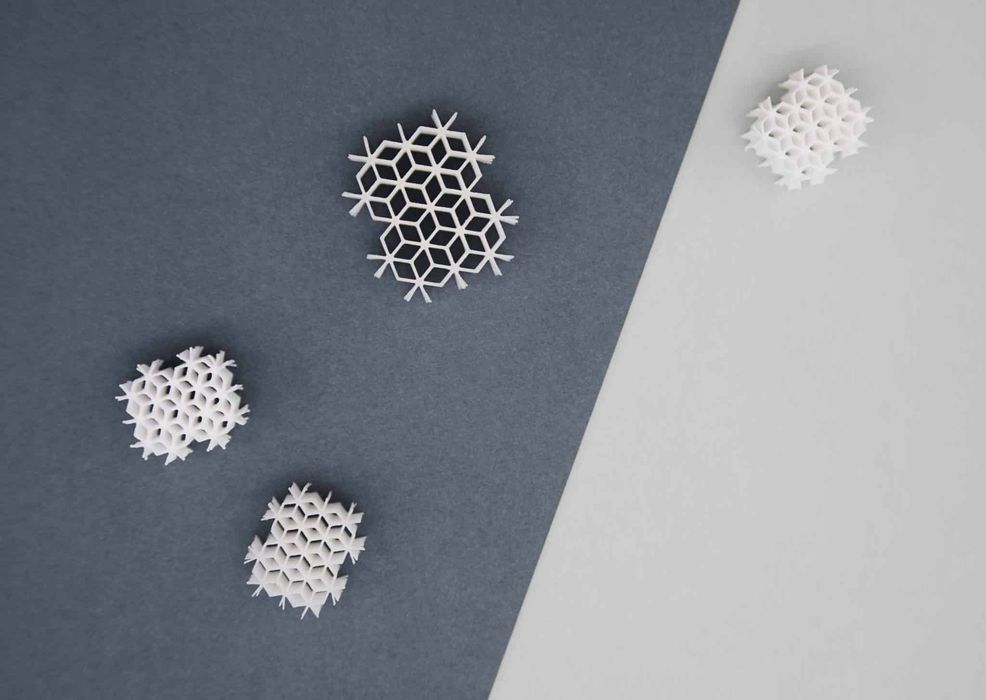
Like SLS, FDR is also well equipped for production volumes thanks to its rapid sintering, minimal post-processing and the ability to nest multiple parts in a single build. This is where the technology offers a distinct edge over resolution-matching resin technologies. As EOS says: “The 3D printing methods that can match FDR for detail resolution, like SLA and DLP, can’t approximate its production volume: This is due in large part to the slow build processes of these resin-based methods, which the relatively quick laser sintering of FDR can easily outpace.”
Read the rest of this story at VoxelMatters