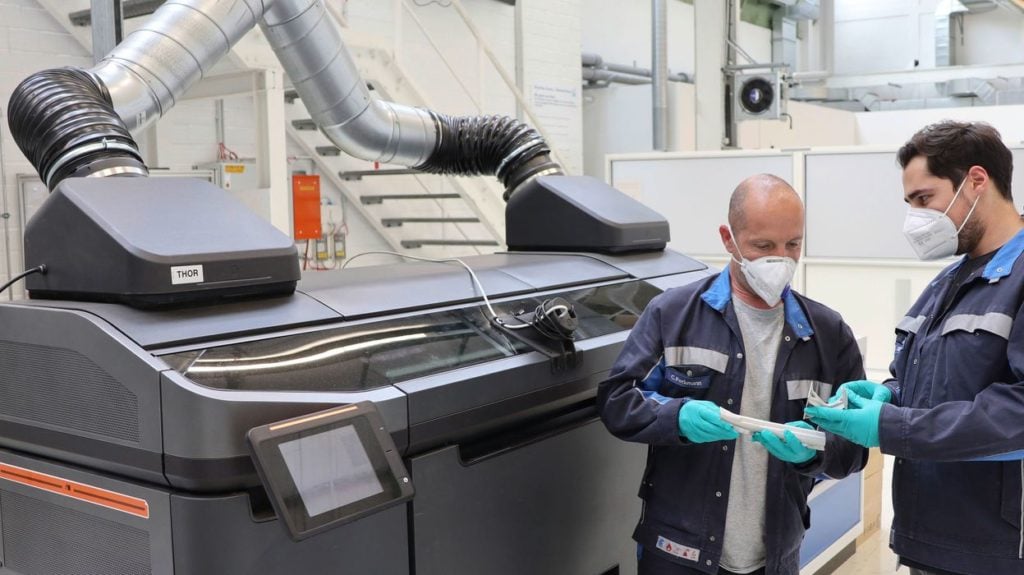
Volkswagen announced a collaboration with Siemens and HP to enable production of complex 3D printed parts for future vehicles.
The well-known German automaker has actually been using 3D printing for over two decades, and employs many of the 3D printing processes on the market today. The company opened an additive manufacturing center in Wolfsburg three years ago, and it seems that this center will be the focus of AM activity for the next few years.
Integrating AM into a world-class manufacturing environment such as Volkswagenās is not a trivial matter, and this is why they have partnered with Siemens, which will provide the sophisticated software necessary for the project.
They explain:
āOne key process step that has been worked on jointly by Siemens and VW is optimizing the positioning of components in the build chamber. Known as nesting, this technique makes it possible to produce twice as many parts per print session.ā
That is no doubt one of many production aspects that would be considered when developing a way to integrate AM.
The 3D printers to be used in the Volkswagen project will be HPās Metal Jet, with which the VW team are by now well acquainted. This device uses a binder jet process in which adhesive is selectively applied to powder bed, layer-by-layer. Objects are formed in this way, and a heat treatment after printing sinters the metal particles together to form fully solid metal parts.
Volkswagen has a long-term strategy underway. In this short video from 2019 you can see hints of whatās happening today:
But why is Volkswagen pursuing this goal? It seems they have seen the advantages now available to the aerospace industry through that industryās long experimentation with AM.
These benefits include: lighter weight parts; complex parts requiring less assembly; and new part designs that could not have previously been considered using conventional manufacturing techniques.
Volkswagen explained some of the initial advantages obtained with the process:
āThe first components made using the binder jetting process have gone to Osnabrück for certification: components for the A pillar of the T-Roc convertible. These weigh almost 50 percent less than conventional components made from sheet steel. This reduction alone makes the process especially interesting for automotive production applications. Volkswagen has already successfully conducted crash tests on 3D-printed metallic vehicle components. Until now, the production of larger volumes was not cost-effective enough. However, the new technology and the collaboration will now make production-line use economically viable.ā
It appears that Volkswagen has been waiting for a technology to emerge that is sufficiently inexpensive to operate to financially justify the move forward. That technology seems to be HPās Metal Jet.
Where are they heading? They plan on producing a modest 100,000 parts per year by 2025, but scale up to 1M components by 2046. While the target of 1M seems large, I am quite puzzled by the slowness of their scaling up process. By 2046 the technologies available in 3D printing will be vastly different and no doubt significantly more productive. Over the course of those 25 years part designs will become radically different from today.
Nevertheless, Volkswagen is one of the first large automakers to commit to large-scale 3D printing for production.
Via Volkswagen