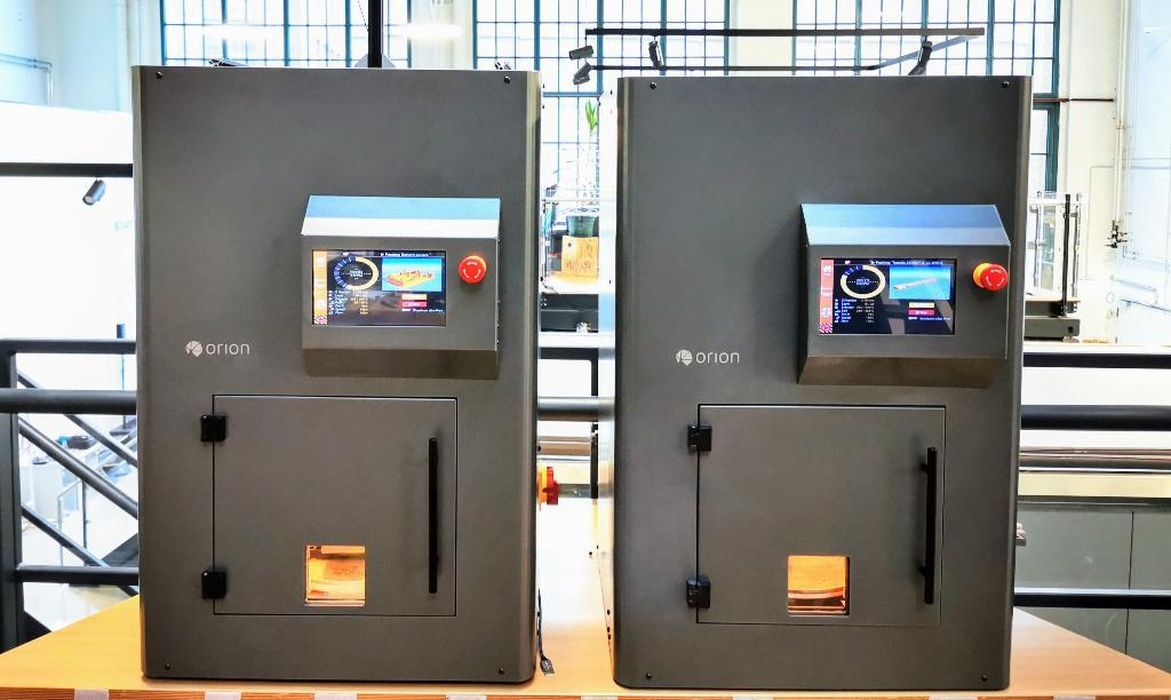
Orion AM’s Thermal Radiation Fusion 3D printing process can produce incredibly strong parts.
You may not have heard of Germany-based Orion AM, and that’s likely because they were formed just before the pandemic. Their goal is to produce parts for advanced applications using aerospace-grade polymers, like PEEK and similar high-temperature engineering materials.
Their unique Thermal Radiation Heating process provides a twist on traditional FFF 3D printing.
Normal FFF processes involve laying down a line of extruded polymer on top of a prior layer. The problem is that the earlier layer has cooled somewhat, making the bonds between the layers less strong. This is quite evident in many typical 3D prints as they tend to break along layer lines. Some even re-orient parts to ensure the layer lines do not align with expected mechanical stresses.
Non of this would matter if the parts were truly isotropic, where the mechanical properties are identical regardless of the direction of the force. No layer lines would exist.
That’s the typical scenario for injection molding, where the entire part is liquid and crystallizes all at once. As a result, injection molded parts are often seen as “superior” to 3D printed parts, although the geometry constraints can be severe.
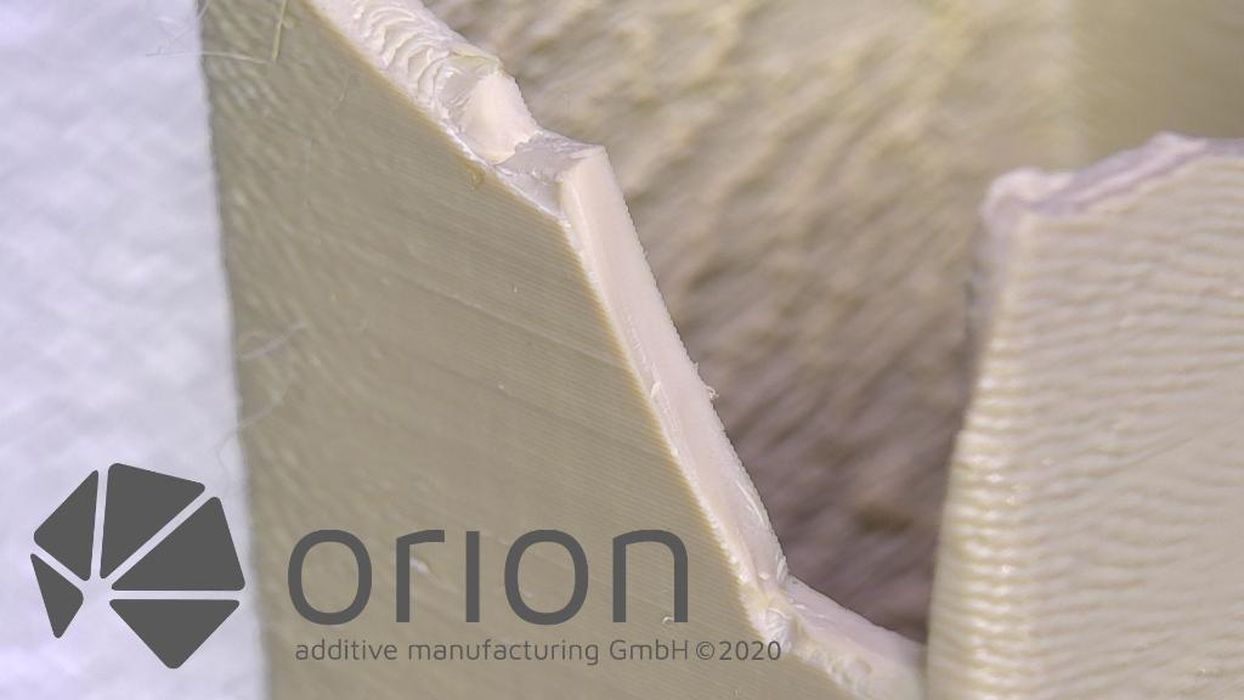
Orion AM’s FFF-TRH process apparently solves this issue. While the extrusion part of the FFF process is basically the same, the chamber in which the extrusion takes place is bathed in thermal radiation.
They don’t use convective heating approaches, which are typical for heated chambers. Instead they use a radiative approach that provides a very even and precise level of heating. The radiation is also tuned to match the heat spectrum of the target material. It’s not quite a microwave, but operates much like one.
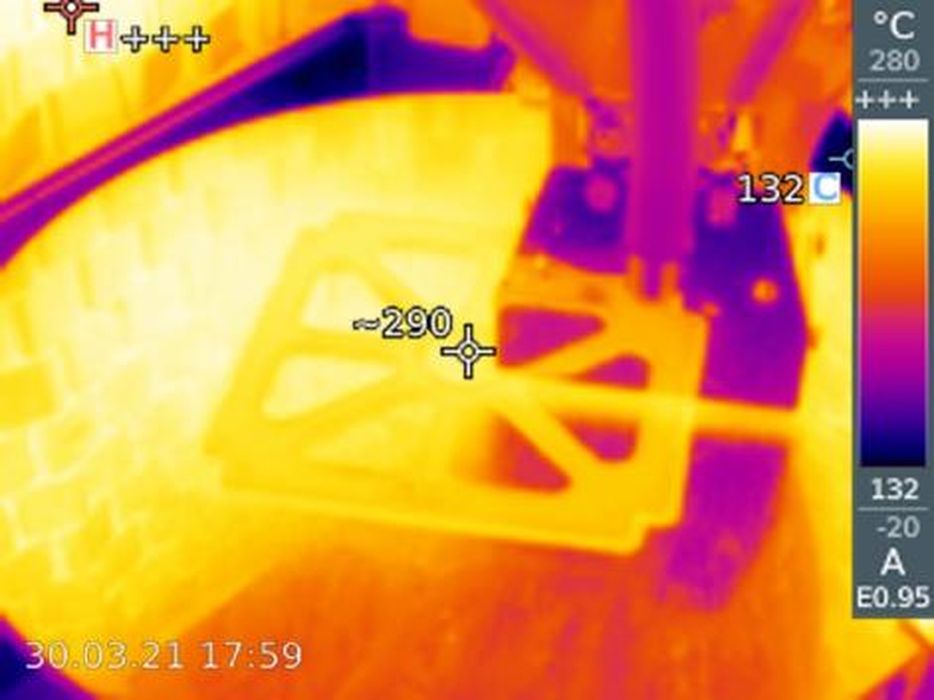
The effect of FFF-TRH is that the extruded material remains capable of strong bonding. This is not a surprise, as Orion AM said the temperature in the chamber can be up to 300C. Subsequent layers bond extremely well to previous layers, resulting in a very strong part.
How strong? Watch this video:
You’ll notice in the video that there are no visible layers in the TRH-printed part. That’s because the layers bonded deeply into each other. You do see layers on the outside surface of the part, however, but that division doesn’t carry into the interior of the part.
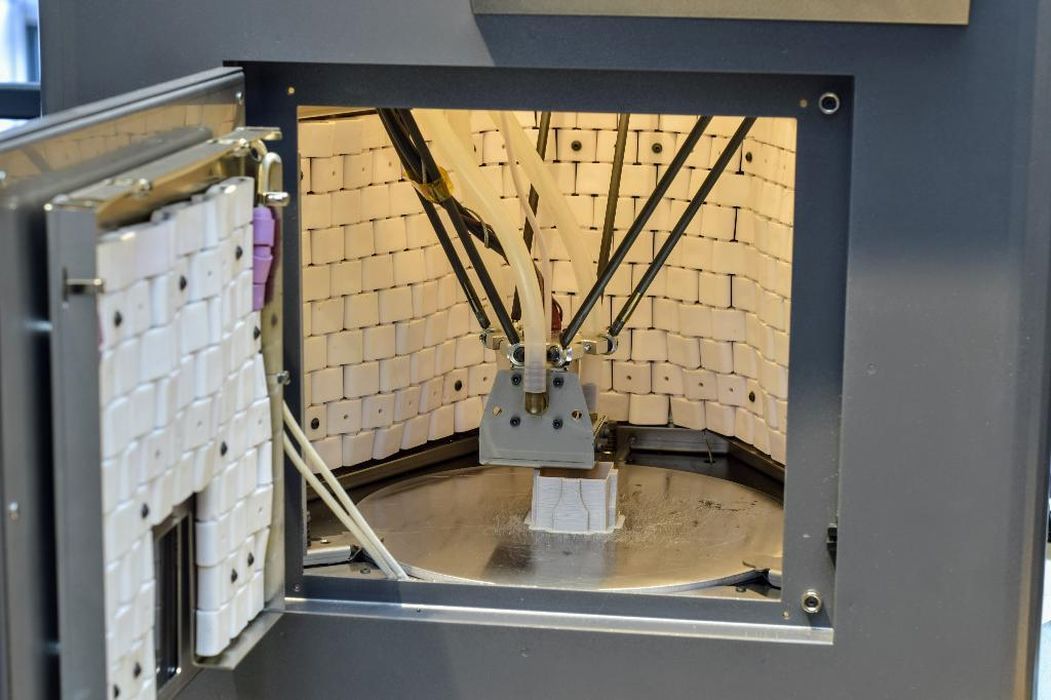
Orion AM markets two variations of their technology, the A150 and M150 (for medical use). Both machines sport a cylindrical build chamber of size 180mm diameter and 150 mm tall.
It’s not surprising the build chamber is cylindrical, and not only because they seem to be using a delta-style motion system: the cylindrical geometry would be ideal for equal thermal radiation on all sides of the print.
The extrusion system on these machines is able to print layers as small as 0.20mm, and has swappable nozzles ranging from 0.1 – 0.4mm. This enables operators to 3D print parts with very fine details.
The hot end can reach 500C, and the print surface is heated to 300C. They say the TRH system can heat the chamber to 315C, and the material to 370C. This enables them to print near-perfect parts using these materials:
- PEEK
- PAEK
- PEKK
- PEI
- ULTEM1010
- ULTEM9085
- ABS
- PC
- PA6
- PA12
- PPSF/PPSU
Using the FFF-TRH printing process one could produce extremely strong parts using already-strong engineering materials like PEEK.
That has been recognized by the European Space Agency, which has used the technology to produce samples for an abrasion test on the Rashid lunar rover that is currently enroute to the Moon.
The Emirates Lunar Mission was launched in December via a SpaceX Falcon 9 rocket, and is expected to arrive this March. The Rashid lander is riding with the Japanese-built Hakuto lander, which will take it (hopefully) safely to the surface.
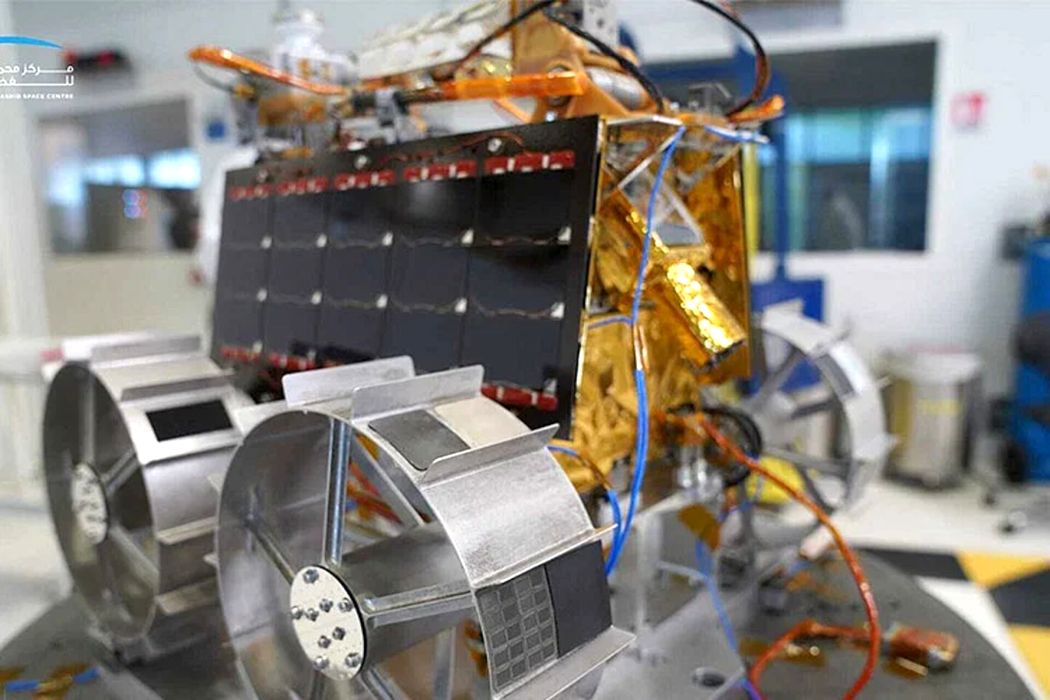
Above you can see an image of the Rashid lander. If you look carefully you’ll see some colored patches between the treads of the wheels. Some of these are 3D printed samples — made by Orion AM.
The experiment used a material that is based on PEEK, but contains carbon nanotubes & graphene, and is a conductive material. As the wheels rotate the material will come in contact with the lunar surface, allowing abrasion testing to take place.
Apparently this will be the very first time 3D printed PEEK parts will touch the Moon.
They won’t be the last.
Via Orion AM (Hat tip to Benjamin) and The National News