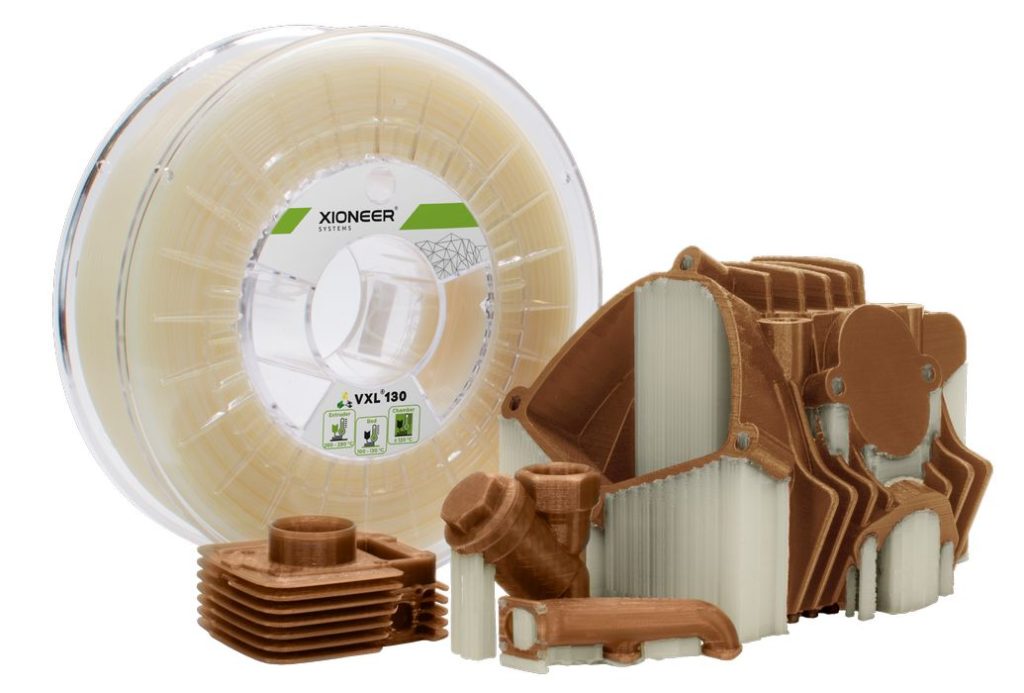
SPONSORED CONTENT
A support material you may not have heard of is VXL, and it could be the best support material available today.
Supporting overhangs for FFF 3D printing has always been problematic, yet it is a necessary evil we all must deal with. Over the years there have been increasingly sophisticated approaches to solving this dilemma, with many options available today.
Xioneer published a hierarchy of support resolution strategies that explains these options, which helps explain our shared experience solving the overhang problem. Here is their hierarchy, with my thoughts:
Trivial Method: Avoid Support Structures
You may laugh, but this is perhaps the most frequently used approach: just donāt use support material at all! If you are very fortunate that the geometry of your 3D print just happens to eliminate overhangs if 3D printed in a peculiar orientation, youāre gold. But most often this is not the case.
Beginner Method: Use Model Material For Supports
For equipment using only a single material, this is the only option available. While it does work, it almost always involves the tedious task of ripping off the excess support structures after printing completes. However, even then the surface texture is almost always ruined by the support attachment points.
In some unusual geometries, it is actually impossible to use this approach because the supports end up inside the print where they are inaccessible for removal.
Quick Method: Use Dedicated Break-Away Support Material
This method requires a 3D printer that can deposit a second material, and itās used to 3D print a support material that does not chemically bond with the model material. Thatās ideal because the interface leaves a smooth surface, and the support material can be easily pulled away.
That is, if it is accessible. There are part geometries that can still lock in the breakaway support material inside a 3D print, so this approach is not always usable.
Lazy Method: Use Soluble Support Material
This approach also requires a 3D printer that can deposit two different materials, and this is the approach used by an increasing number of 3D printer manufacturers. The reason is that soluble supports are the easiest method because virtually no labor is required to post-process the print: just drop it in a solvent solution inside a support removal station (such as Xioneerās Vortex EZ) and chemistry does the work. After some hours, the print is clean of support materials and has a smooth surface.
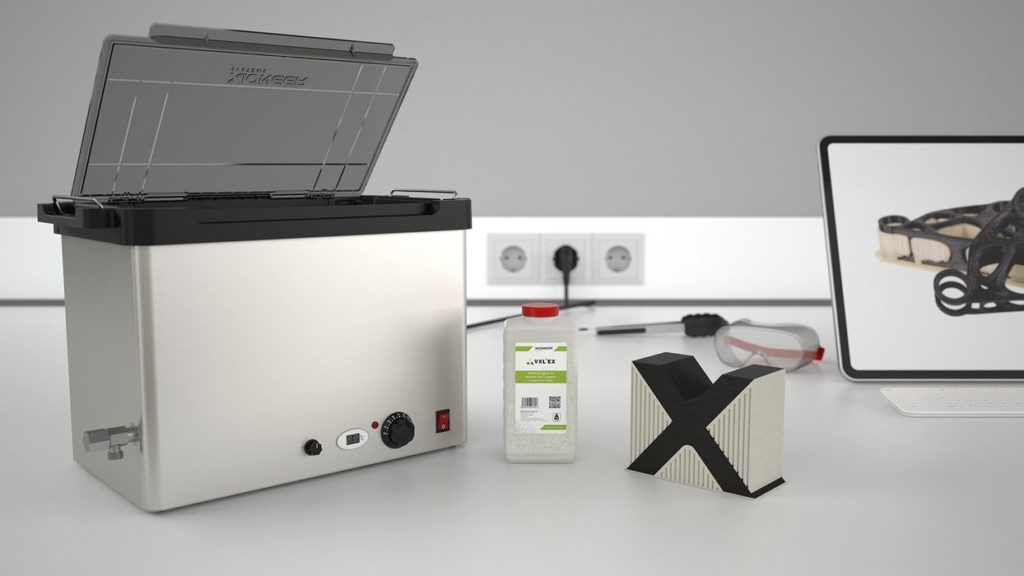
This sounds like the solution to the support challenge, but in fact weāre not done yet. It turns out there are three basic forms of soluble support materials: water-soluble, oil-soluble, and alkali-soluble.
The water-soluble materials are perhaps the most commonly found in the industry today, including BVOH and PVA. While these materials do work, they have a number of challenges aside from their high cost.
Any water-soluble material tends to rapidly absorb moisture from the air, and once this happens they do not print well: the absorbed moisture boils in the hot end, creating bubbles and gaps. To counteract this, water-soluble support must be constantly kept in extremely dry conditions. You could use Xioneerās filament storage cabinet DryBox EZ but keeping water-soluble filaments dry has never been an easy task.
A second major issue with water-soluble materials is that they have relatively low melting points. This means they cannot be effectively used for higher temperature materials such as PEEK, PEAK, PEKK, PSU, or ULTEM.
The most popular oil-soluble support material is HIPS, a commonly available 3D print material. While it is not expensive, it turns out the usual solvent, limonene, is a lot more expensive than the plain water used for dissolving water-soluble materials. Thereās also an odor problem: prints processed in limonene actually end up smelling like orange peels, the material limonene is made from. Besides, limonene is highly flammable hazardous chemical.
Finally, there are the alkali-soluble support materials. I should say āmaterialā, because at this moment there is only one open filament on the market: Xioneerās VXL material. This support material, which was specifically designed for 3D printing, has a number of amazing properties:
- Bonds with all commonly used 3D print materials, including ABS, ASA, Nylon, TPU, PC, PEEK and many more
- Very smooth part surfaces can easily be obtained
- Itās easily dissolved, meaning you donāt require much labor to post process 3D printed parts.
- The solvent used is warm water with a mere spoonful of the non-caustic and safe VXL-EX powder
- Itās highly resistant to moisture absorption, unlike PVA and BVOH, so no special handling is required
- VXL is very easy to 3D print
- It is chemically stable at high temperatures, thus avoiding nozzle clogs that occur with other support materials and providing constant material flow
- It comes in a variety of formulations (VXL 70, 90, 111, and 130) to match the specific model material you use
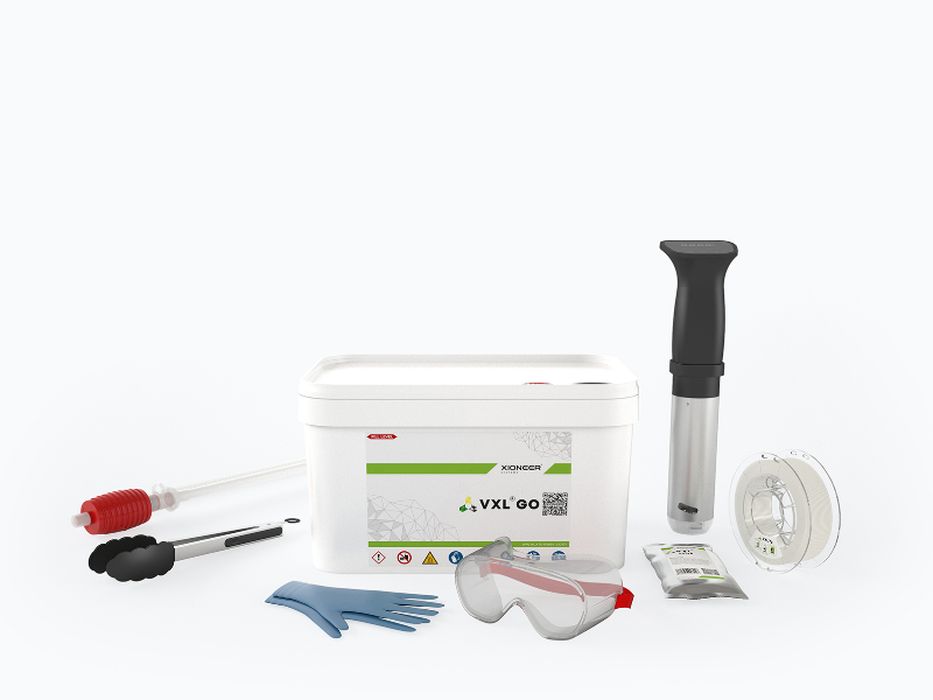
For those who want to try VXL, Xioneer offers a budget starter kit VXL Go. It includes a sample spool of VXL, a small support removal station, and a number of accessories to get you off the ground.
As you can see, while there are many options for support materials there are also many issues. Fortunately, VXL avoids the problems and provides an easy way to 3D print highly complex geometries in a reliable fashion.
Via Xioneer