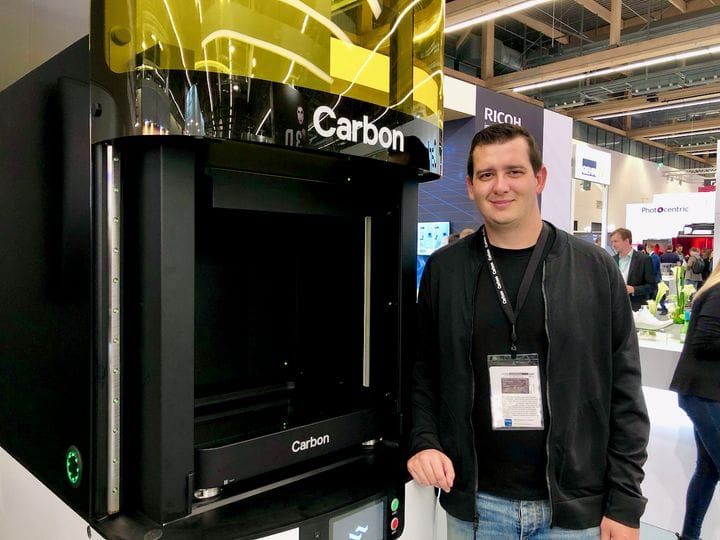
I spoke with Phil DeSimone to find our more about Carbon’s recent decision to make their sophisticated lattice generation tool available to everyone.
A short while ago the company announced plans to make their hitherto customer-only Design Engine CAD tool available to non-Carbon customers.
It’s a very curious decision, because it is a key part of Carbon’s strategy to enable manufacturing clients to use 3D printing technology for large-scale production: most manufacturers don’t have the expertise to design the highly complex geometries necessary to fully leverage the advantages of 3D printing, so Carbon made a tool to do so, Design Engine. By providing this tool to clients, manufacturers would very likely purchase a lot more Carbon equipment, good for both parties.
DeSimone, one of the co-founders of Carbon, made time to chat with me about this question, and other things happening at the 3D printer manufacturer.
DeSimone explained how the decision to produce Design Engine came about:
”We found the design side was very limited, even on our very first client engagement. Making lattices containing 100,000 struts with traditional CAD tools is simply not possible. It would take many years of human work to get those designs done. We created software to take advantage of this gap. All Carbon clients been using this product behind the scenes. Now, we’re taking the tool out to the marketplace.”
Launched in last January, Design Engine is a conformal lattice generation tool, but it’s now “multizone”. This means that a designer can specify different “zones” within a design that have different styles of lattices, perhaps denser, or less dense within a single part. These different zones can offer different mechanical performances, and Design Engine knits them smoothly together.
DeSimone explained:
“The designer highlights areas of the design that need specific performance, and Design Engine populates that region to accomplish this. For example, our client Specialized made a bicycle saddle that had seven different performance zones, in a space that’s less than one inch thick!”
One can imagine the complications if trying to recreate that complex saddle design using conventional manufacturing tools.
DeSimone said:
“These complex designs are often considered impossible, but they’re easy to make with this tool.”
There’s something interesting about Design Engine. While it was ostensibly made to service Carbon clients using the company’s resin process, DLS, the software is actually process agnostic. It can generate complex, multizoned lattice models usable for DMLS, FFF or other 3D printing processes.
DeSimone explained Design Engine’s benefit and future:
“When designing a product, there is a need for an orchestrator, something to help people through. We’re going to provide what we are good at to help the industry as a whole.”
Design Engine will be marketed with normal seat licenses as one would expect, and DeSimone explained there would be two tiers: Basic and Pro. It’s expected to appear sometime in 2022Q1.
I asked how Design Engine differs from what is likely it’s competitor in the market, nTopology. Desimone explained that Design Engine is cloud-based, whereas the competition is GPU based. This is an interesting difference because it suggests that the cloud approach could provide faster results due to the ability to leverage massive cloud power, versus what you get from a locally-installed graphics card.
DeSimone emphasized that the “parts produced by Design Engine are actually manufacturable,” something that isn’t always the case with complex generation tools.
DeSimone said the tool has been quite successful with Carbon clients:
“Learnings from the field are integrated. The more applications that come forward, the more possible sales for hardware. We found that after a client’s first product design experience, the second to tenth products come quite quickly.”
Carbon hopes that the tool will assist designers everywhere to bring new products to the market faster, and I do, too.
Finally, DeSimone said:
“It’s not about making a 3D printed part, it’s about making a new kind of part that could not be made elsewhere. The goal is to get more people in the space designing better products.”
And that is precisely what should happen when people start using Design Engine for new products.
I am extremely interested to see how this tool is adopted by the AM industry. It’s possible that its availability might boost the sales of non-Carbon 3D printers, but in the end, if the use of additive technologies becomes common or even a standard, then every company will gain tremendously.
Via Carbon