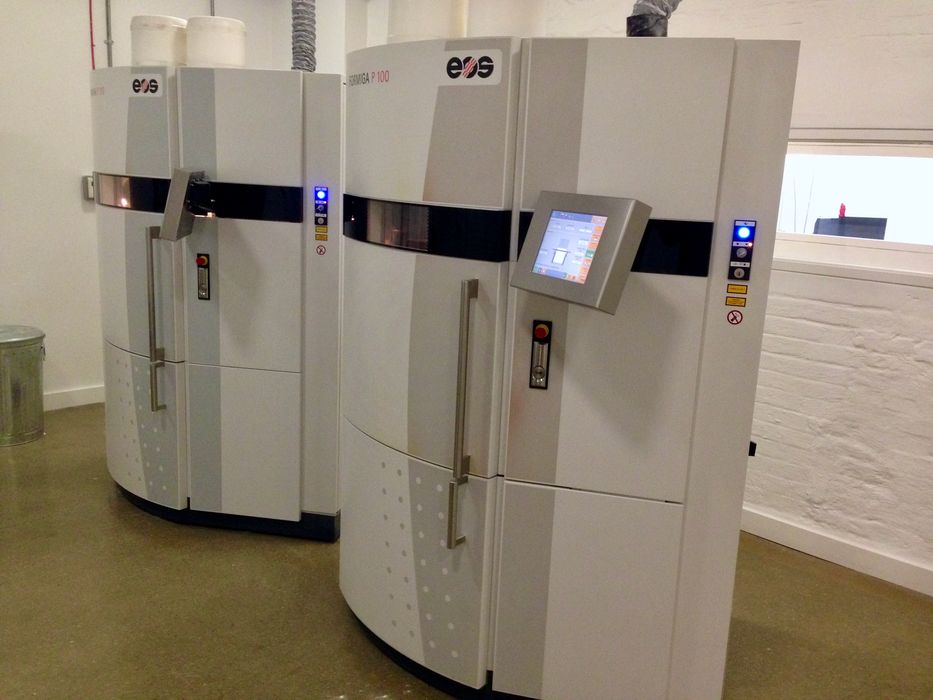
We have consumer-level filament and resin 3D printers, why don’t we have consumer SLS 3D printers?
Note that when I say “consumer-level”, I really mean “enthusiast level” because today’s desktop 3D printers, in spite of their incredible advances in functionality and pricing, are still really suitable only for tech-savvy enthusiasts. There is much to do to make that change, and I’ll get into that another day.
Today we have FFF and MSLA 3D printers that are priced for and targeted at consumer enthusiasts. These devices work pretty well, and there are increasing choices in materials for each at reasonable prices.
What we haven’t seen yet is a desktop SLS 3D printer that’s targeted at consumers. Well, the closest product to that might have been the Sintratec Kit, which was priced at around US$5,300 back in 2017. At that price point it was far too high to be considered a consumer product.
Why hasn’t that happened yet?
First let’s look at the three processes involved in these three 3D printer technologies.
FFF 3D Printing
The first available desktop 3D printing technology involves simply heating a thermoplastic filament to the appropriate level of softness, and then extruding it onto a platform, layer by layer.
MSLA 3D Printing
MSLA 3D printing is a variation of the original SLA process where a laser solidifies successive layers of photopolymer resin. MSLA is similar except that instead of an expensive laser, you have a projector or LCD panel illuminate the entire layer at once. These are quite inexpensive and produce amazingly good output.
SLS 3D Printing
While FFF uses solid material and MSLA uses liquid material, SLS uses powder material. In an SLS system a blade pushes out a flat plane of fine thermoplastic powder (often nylon). Then a laser sweeps across this surface, selectively melting portions into solid form. After one layer is complete, the blade returns and deposits another layer of fine powder, which the laser then processes as before. When the job completes, the printed object is buried in a chamber full of powder. It must be extracted and the powder removed.
Why No Desktop SLS 3D Printers?
To cut the discussion short, the answer is pricing. There currently is no way to lower the price of manufacturing a desktop SLS 3D printer, as far as I know.
The main issue, but certainly not the only one, is the cost of the laser. That alone will ramp up the price significantly. Sintratec was only able to get away with their relatively inexpensive kit in 2017 because they used dark powder only, which tended to absorb more laser light and allowed them to use less expensive lasers.
Even so, their device was still priced at over US$5,000.
SLA also used lasers, and somehow that technology became MSLA. What’s the difference?
The differences is that in SLA the laser was swapped out for inexpensive, mass produced LCD panels. These were made for other applications and repurposed for MSLA 3D printers at low cost. That allowed some MSLA systems to be priced as low as US$200. Desktop resin system that do use lasers, like Formlabs, continue to be priced in the US$4,000 range.
Is there an equivalent of an “LCD panel” for solidifying thermoplastic powder? I don’t think so, as the energies are higher. Remember: thermoplastic powder literally melts by heat energy, while photopolymer resin activates with a simple chemical reaction to certain light frequencies.
The result is that there’s no way to bring the price down and mass produce desktop SLS systems.
There are other challenges.
One is powder management. In a typical SLS system the operator must wear significant PPE to avoid breathing in any of the fine plastic powder during operations. That would be challenging for home users.
Another challenging is powder recycling. The nature of SLS 3D printing leaves lots of unfused powder after a job ends. In industrial systems this powder is reclaimed through complex vacuum systems and sifted to remove extraneous blobs from laser spatters. The resulting powder can be reused — but only to a certain ratio.
To perform that recycling there are complex systems to collect, sift and mix powders to appropriate ratios. All of that implies there are more components required than just the 3D printer, and that adds even more to the cost.
Finally, SLS 3D printing is just a lot more complex than FFF or resin 3D printing: very precise thermals are required to ensure quality prints, and that’s going to add more to the cost.
Because of all of the above, I can’t see a powder-based desktop SLS 3D printer emerge in the near future, or at least one that is priced where most consumers could afford the cost.