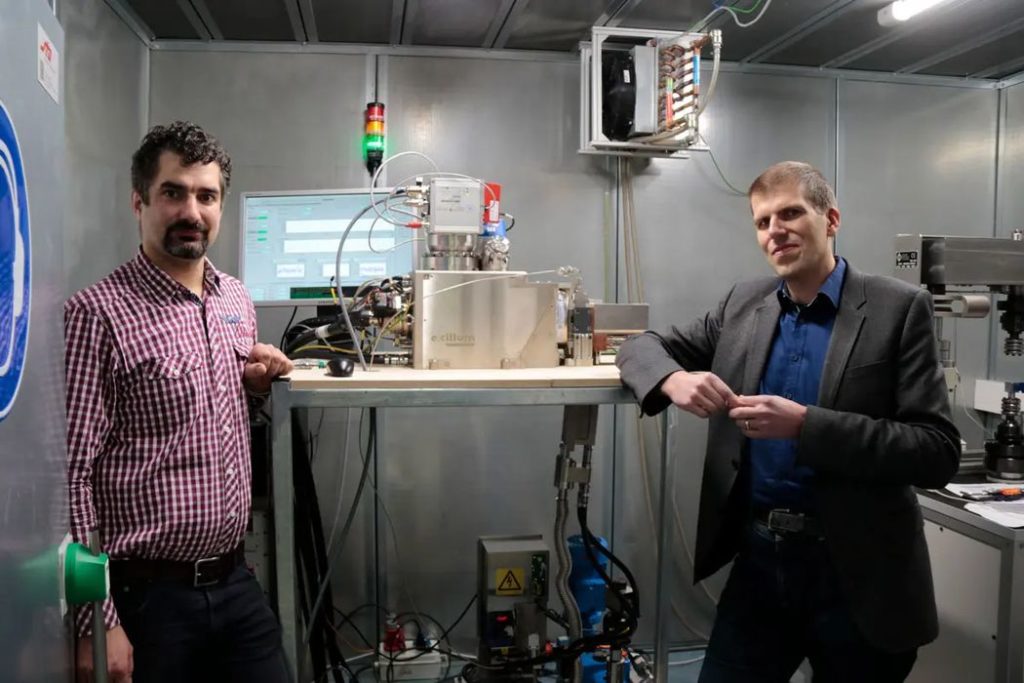
New research has developed an incredibly powerful X-ray system that could directly show microstructures in 3D prints as they are made.
Researchers installed a MetalJet E1+ 160 kV from Excillum, said to be the worldās brightest X-ray source, and apparently the first to be installed at a University in Europe. The ā¬500K (US$566K) X-ray tubeās power is an incredible 1000 watts, and can focus to a 30 micron spot diameter.
The device achieves this high power level due to a unique cooling system in the anode, which is made from liquid indium-gallium alloy.
But what would you do with such a powerful X-ray? Head of X-ray fine structure analysis group, Alexander Liehr explained (via Google Translate):
āThis allows us to observe live what is happening in our samples during the experiment, for example how liquid metal solidifies or how components react under compressive or tensile stress and when exactly the finest microscopic cracks form in the material , which we only notice much later would see with the naked eye.ā
Hold on a moment, isnāt that precisely what many metal 3D printing operations are most concerned with?
Metal 3D printing has become popular, but it is very challenging to do because of the microstructures generated during printing.
As the laser passes over fine metal powder in a typical LPBF system, the metals quickly melt into a small pool. After the laser swings away, the meltpool cools and solidifies ā crystallizes ā into a portion of the desired object.
The problems result in poorly formed crystalline microstructures. The microstructure could be so bad that it actually compromises the strength of the part. Even worse, many metal 3D prints are intended for end-use by customers, and so they must meet strength targets.
The new X-ray system could help figure out the best way to achieve optimum 3D printed microstructures. Dr. Thomas Niendorf explains how this could be done (via Google Translate):
āHuge amounts of data come in live to us: high-resolution radiographic and diffraction images of the X-ray source, but also information on the temperature change in the material from other sensors. If we then change parameters such as the exact composition of the materials or process speeds, we can see in real time how the properties change in 3D printing.ā
This could be a significant breakthrough. Current advanced metal 3D printing systems employ real time meltpool monitoring systems that typically track temperature and cooling rates. However, being able to actually see the microstructures is at another level entirely.
This capability could be used to test various print parameters to gauge the quality of the microstructures, eventually resulting in rules-of-thumb for achieving proper 3D prints.
It might also be possible to equip a metal 3D printer with the same X-ray device so that the printer itself could perform realtime adjustments to maintain target microstructures as the print proceeds. However, thatās likely only happening on the most expensive devices, since the cost of the X-ray tube itself is over half a million dollars.
Thereās more: this approach could also be used for polymer examination. In other words, we could also see improvements in print parameters and techniques for polymers as well as metals.
Now Iām wondering what the industrial 3D printers of the future might truly be capable of making.
Via 3Druck (Deutsche) (Hat tip to Benjamin)