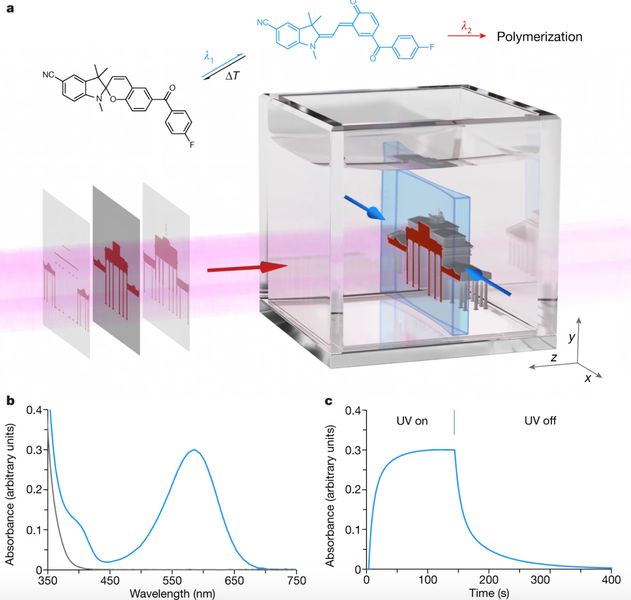
3D printing is entering its fourth decade.
The technology has been booming lately—hundreds of millions of dollars are being invested in industrial 3D printing, with companies exploring applications ranging from footwear and implants to rocket engines.
There are several types of 3D printing. The most popular is currently fused deposition modeling (FDM)—also known as fused filament fabrication (FFF)—a cost-effective and quick method for producing physical models.
FFF uses the layer-by-layer principle, which results in parts having relatively rough surface finishes and lacking strength. This is also the case for selective laser sintering (SLS), stereolithography (SLA) and other processes.
Volumetric 3D Printing
Enter volumetric 3D printing, also known as holographic or tomographic 3D printing, which was first introduced by researchers at Lawrence Livermore National Laboratory (LLNL). Instead of a layer-by-layer approach, volumetric 3D printing works by repeatedly projecting a pattern into a vat of transparent photopolymer liquid from various angles; this method is known as computed axial lithography (CAL). It is like a CT scan in reverse, and the pattern is projected to form the object rather than scanning the object.
Another player in the market is xolo, a startup developed by scientists in Germany. They have named their new procedure ”xolography,” as detailed in research published in Nature.
Xolography
The researchers introduce xolography as “a dual-color technique using photoswitchable photoinitiators to induce local polymerization inside a confined monomer volume upon linear excitation by intersecting light beams of different wavelengths.” The concept is demonstrated using a volumetric printer designed to generate 3D objects with complex structural features as well as mechanical and optical functions.
In other words, two different kinds of light energy are applied on a vat of photopolymer resin that reacts differently to the light energy. This also explains the name of the company and the printing process, as the crossing (X) light beams generate entire objects (holos).
The approach is to project a “sheet” of light into the resin vat. Though sheets may seem much like the layers used in other 3D printing, there are many different angles in this approach. The sheets are not stacked on top of each other to build an object. As can be seen in the figure above, a light sheet of a certain wavelength (λ 1 ) activates a thin layer of photoinitiator molecules.
Another projector arranged orthogonally generates light of a different wavelength (λ 2 ) and focuses sectional images of the 3D model to be manufactured into the plane of the light sheet. Only the initiator molecules in the latent state absorb the light of the projector and cause the activated resin to solidify as it polymerizes. The optical setup is fixed, while the vat of resin is moved to present different views. Additionally, because the rest of the resin is not activated, the intersecting wavelength inhibits polymerization. In this way, the desired object is continuously fabricated.
Because this approach of utilizing two intersecting lights both encourages and inhibits polymerization, xolography can produce solids of very high resolution. Additionally, the sheet approach ensures that any specific voxel is exposed to the curing light only once during the entire process.
Read more at ENGINEERING.com