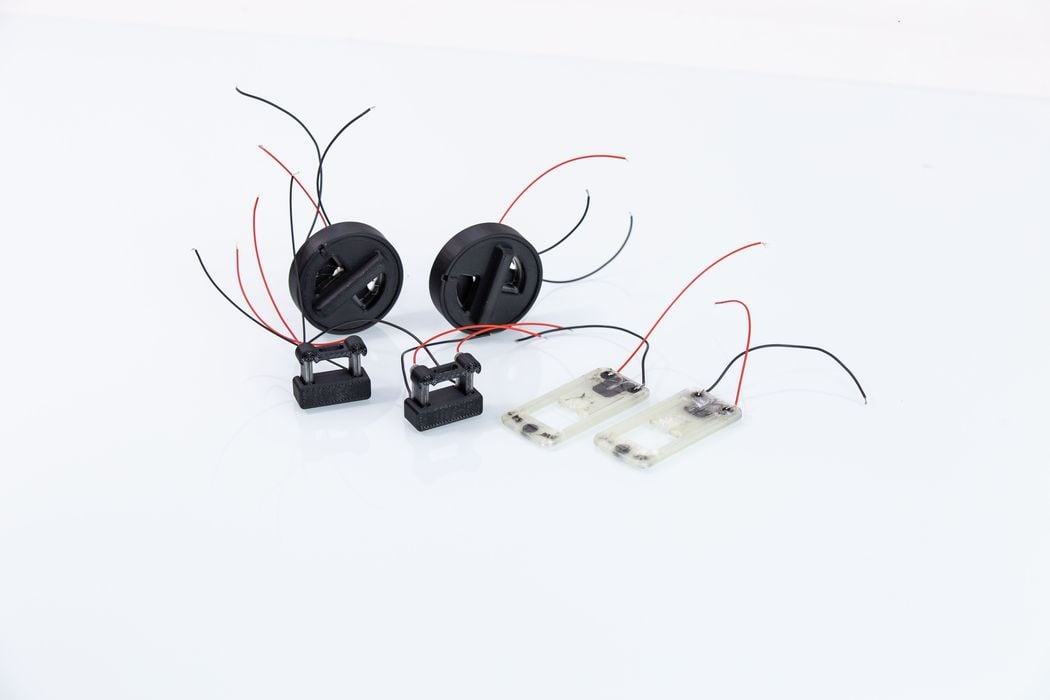
Zortrax recently completed a project for ESA that involved significant use of 4D printing.
If you havenāt heard of 4D printing, thatās not surprising. It is a very complex variation of 3D printing that is used to create parts with peculiar functions.
Zortrax explains 4D printing:
āThe fourth, additional dimension added in the 4D printing technology is time. 4D printed objects can change their geometry and other properties in response to various stimuli like temperature, moisture, electric current, and many more. Imagine an origami-like structure that stays folded in room temperature but unfolds when heated up.ā
In other words, parts can change shape after they are printed. The shape change capability is leveraged to provide unique functions that would otherwise be unavailable if just printing in ā3Dā mode.
ESA was particularly interested in this technology because 4D objects are able to perform mechanical actions without the need for hinges, bolts and other hardware that might add to the weight of a space-based system. Weight is everything in the space business, so itās not surprising ESA pursued this approach.
Zortrax has been the prime contractor on a project to investigate the 4D effect on ESA parts, and has just completed the work. The project involved determining a lightweight 4D printing approach for deploying components in space.
However, designing a successful system to do so is incredibly complex. Not only would suitable materials have to chosen, but a sophisticated geometry would have to developed that would leverage the shape-changing qualities of the material. All that would also have to happen in the anticipated thermal conditions of the space environment.
In addition, conductive elements were required in the design. Such materials exist, but would somehow have to be incorporated into the shape-changing 4D design.
Zortrax had no trouble finding suitable conductive materials, but had trouble with selecting materials for the main mechanical portions of the part. They explain:
āRight from the get-go, it became apparent that commercially available shape memory filaments had glass transition temperature of up to 55 ā which was not enough for space applications. A 4D printed mechanism with such filaments would activate on its own in temperatures exceeding 55 ā which happens quite often on Low Earth Orbit when the spacecraft is exposed to sunlight.
For this reason, Zortrax made a custom shape memory filament which had glass transition temperature of 75 ā which was 50% higher than anything available on the market. The material got delivered, thoroughly tested, and found suitable for proof-of-concept 4D printed systems.ā
Zortrax was able to design three different parts that were able to meet the requirements, which included bending, torsion and actual deployment.
They used their M300 Dual 3D printer, which allows for printing of two different materials in the same job. This is critical for 4D printing, which relies on differing thermal properties in a ābi-materialā printed object.
But how do you actually design these parts? What shapes should be used to accomplish the goals? At the beginning of the project, even Zortrax didnāt know the answers to these and other questions.
However, the project involved considerable experimentation with different geometries, and eventually they were able to develop parts that actually performed as required when triggered by electricity. Their lengthy post details their iterative development process, and itās an interesting read.
4D printing is quite complex, and yet has a promising future. My hope is that the approach becomes more recognized by software and materials developers in coming years. Then we may see tools that can be used to print true 4D objects on demand.
Via Zortrax