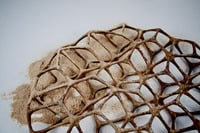
Their new “Tree-D Printing” process involves using actual sawdust as print material. Their process is powder-based (or in this case, “sawdust-based”, we suppose) in which very thin layers of sawdust are laid out, then the object’s solid portions are fused with a binder. This is very similar to how other powder-based 3D printers operate, except that the print material here is significantly less expensive. Hey, it’s wood!
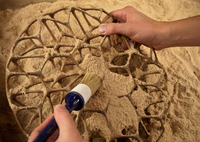
This secret wooden project has evidently been underway for over two years, and the technical dudes at FOC have been able to “3D print in a range of wood sorts from around the world”. Here’s the highlights of this still experimental technique:
- The wood must be reduced to a very fine sawdust
- The first prints have used teak and mahogany wood
- Object strength is said to be similar to MDF, which is pretty decent
- Print accuracy rivals laser sintering processes
- Work continues to develop ways to print softer woods such as Balsa
- Print times are about half the speed of laser sintering (e.g. slow)
- Completed objects must be fished out of a tub of sawdust
We think this is a significant development, not only because wood is a far less expensive material that is typically available locally, but also because wood opens up more possibilities for 3D objects. There are plenty of applications both practical and artistic that will benefit from this new process. Wood just looks and feels different and will certainly be more appropriate for a wide range of new objects.
When will we see the wood process available for general use? FOC plans on printing “interior products” using the process “later this year”, but they do offer to partner with others.
Reminder: Don’t forget you can enter to win one of two free admission tickets to the thingmakers conference in London on May 4th. Enter here!
Sounds like an uprising technology to keep an eye on. From our perspective, it would be even more interesting to experiment printing on different types of wood, especially considering that sawdust from softer woods do not spread evenly on the printer.
Sounds like an uprising technology to keep an eye on. From our perspective, it would be even more interesting to experiment printing on different types of wood, especially considering that sawdust from softer woods do not spread evenly on the printer.
Nice post, thanks for the thorough breakdown of properties, rather than a quick link-through. But, this post exposes some common misconceptions in the maker world about materials. Namely, the difference between isotropic and anisotropic materials.
Isotropic materials – plastics, solid crystals, glass, most metals – have uniformly distributed material, with uniform structure. That generally causes properties like strength to be similar in all directions.
Anisotropic materials on the other hand, have internal structures that vary on different axes, and may be made of multiple types of materials (so-called composites). Most cool materials in the world – Wood, Fiberglass, Bone, Horn, Abalone Shell, and even metals like those in Damascus or Samurai Swords – are all anisotropic. The key here is that the strength, toughness, or rigidity come from this structure, not necessarily from the materials themselves.
Case in point, this "wood" stuff. The article cites that it is comparably strong to MDF, which makes sense, as MDF is made in the same way. But, if you compare MDF to a comparable piece of wood, it is MUCH weaker. For thin prints like the one shown, it would be uselessly delicate. MDF is cool because it's flat, and cheap to make from wood mill waste. As a 3d printing material, this doesn't strike me as that impressive. I suspect that it's strength depends more on the polymer binder that is used, rather than on the wood itself — you could probably make a comparably strong material with clay as the powder, given the same binder.
Now, if we could start printing with chitin or nano-cellulose from bananas, that might make a 3d printed anisotropic material worth getting excited about 🙂
Nice post, thanks for the thorough breakdown of properties, rather than a quick link-through. But, this post exposes some common misconceptions in the maker world about materials. Namely, the difference between isotropic and anisotropic materials.
Isotropic materials – plastics, solid crystals, glass, most metals – have uniformly distributed material, with uniform structure. That generally causes properties like strength to be similar in all directions.
Anisotropic materials on the other hand, have internal structures that vary on different axes, and may be made of multiple types of materials (so-called composites). Most cool materials in the world – Wood, Fiberglass, Bone, Horn, Abalone Shell, and even metals like those in Damascus or Samurai Swords – are all anisotropic. The key here is that the strength, toughness, or rigidity come from this structure, not necessarily from the materials themselves.
Case in point, this "wood" stuff. The article cites that it is comparably strong to MDF, which makes sense, as MDF is made in the same way. But, if you compare MDF to a comparable piece of wood, it is MUCH weaker. For thin prints like the one shown, it would be uselessly delicate. MDF is cool because it's flat, and cheap to make from wood mill waste. As a 3d printing material, this doesn't strike me as that impressive. I suspect that it's strength depends more on the polymer binder that is used, rather than on the wood itself — you could probably make a comparably strong material with clay as the powder, given the same binder.
Now, if we could start printing with chitin or nano-cellulose from bananas, that might make a 3d printed anisotropic material worth getting excited about 🙂
Thought this was aprils fools, but the article you link too is written yesterday! *confused*
Thought this was aprils fools, but the article you link too is written yesterday! *confused*