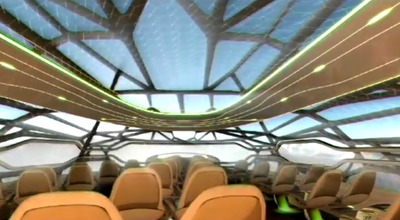
We considered this and had mixed thoughts. There are certainly a number of benefits to 3D printing large portions of an aircraft, but three are most prominent: First, you can manufacture complex shapes in a much more effective manner. Rather than manufacturing parts and then joining them together with bolts or other connectors, why not just 3D print a whole complex component and forego the need for bolts?
The second key advantage would be the ability to vary the internal structure of components, placing strength where stresses occur and lightening up the less stressful areas. Both of these approaches will save considerable weight, an important factor in aircraft.
The third key advantage is an ability to theoretically mix materials during printing to produce unique substances and components. Today this is done only by Objet’s 3D printers, but one can envision a far more capable method in the future.
But there are disadvantages to 3D printing an aircraft as well. First, the size is fantastically beyond even the largest commercial 3D printers today. To put this in perspective, an 80x80x20m “build chamber” (or hangar) would be tens of thousands of times larger than a huge 3D printer of today. This size difference implies one very important factor: The aircraft prints would take almost forever to complete. One meter sized objects on today’s larger 3D printers can actually take days to complete. It may be years to complete a single aircraft cabin at that size if current technology is merely scaled up, particularly if reasonable resolution is required.
We think that a hangar-sized 3D printer requires very different approaches than are used today. One can imagine having multiple print heads operating simultaneously within this giant 3D printer (and by multiple, we mean hundreds). The software to control such a beast would be, um, interesting and resemble automobile traffic management.
One thing we do agree with Forbes: “The technology is more than over 20 years old, but it could be at least another 20 before we see it on the scale of what (Airbus Cabin Designer) Bastian and others are foreseeing.”
Via Forbes
I agree that we should wait another 20 years! It's a brilliant concept and technically viable, but lets wait until we know more about the ins and outs of 3D printing.
I agree that we should wait another 20 years! It's a brilliant concept and technically viable, but lets wait until we know more about the ins and outs of 3D printing.