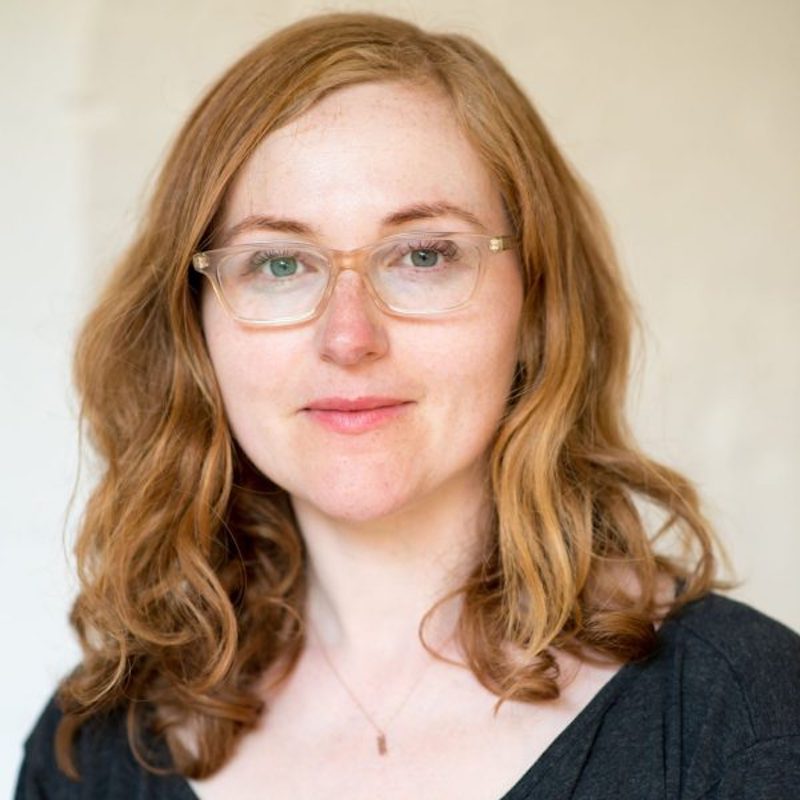
This article originates from Women In 3D Printing and is part of our effort to support the use of 3D printing technology by women. The article is re-published with permission.
Nora Toure: Sophie, could you let us know about your background and what brought you into 3D printing in the first place?
Sophie Kahn: I trained as a photographer, but around 2003, after finishing my undergrad studies at Goldsmiths in London, I became somewhat frustrated with the limitations of photography. I was also becoming intrigued by 3D modeling, and so I enrolled in a Graduate Certificate program in Spatial Information Architecture at RMIT University in Melbourne. This was an interdisciplinary program, set up for artists to collaborate with architects and designers. I was instantly captivated by the 3D scanner the department used. It felt like a very natural transition from photography for me: the scans were made using light and a lens, and contained similar errors to those found in photography (motion blur, etc.) They also had a wax stereolithography printer and so I began experimenting with printing from the glitchy scans I was making.
Nora Toure: What was your very first 3D printed model?
Sophie Kahn: I first printed a city model I had made using draped surfaces in Rhino, that was supposed to be a spatial map of the parts of a street that were included in historical photographs.
Nora Toure: You are the founder of Scannerworks NY. Could you explain furthermore what Scannerworks NY is and the services that you are offering?
Sophie Kahn: I provide 3D laser scanning services to artists, designers, and animators in the New York area. In addition, I consult on digital fabrication, providing advice and referrals to customers who are new to digital fabrication.
Nora Toure: How did you come to build the company?
Sophie Kahn: I initially took out a lease on a Polhemus scanner in grad school, as I was tired of having limited access to 3D equipment – it was like being a photographer without a camera. Then I needed to keep up the lease payments, and wondered whether other people had the same hassles with accessing scanning technology and expertise. I was fortunate to find a niche in the market in New York, and took out some Google ads and quickly found that customers responded.
Nora Toure: And who are your customers now?
Sophie Kahn: I serve a combination of businesses and consumers. Some clients are designers who have a hand-produced item and need to digitize it in order to mass-produce it – eg a hand-carved chair or surfboard. Some are artists who want to scale their work up or down, either to have it fabricated at a monumental scale using CNC milling or to produce limited-edition artist’s multiples using 3D printing.
Nora Toure: What is is that you scan the most?
Sophie Kahn: My most common job is a sculptor’s maquette. Making a scan allows them to translate their skills in making by hand into the realm of the digital, giving a modeler a precise guide from which to reverse-engineer a large model for CNC milling.
Nora Toure: Do you have any (fun or not) story about the company to share with us?
Sophie Kahn: I’ve had more than one phone call requesting a 3D scan of a client’s face, to be used for the purposes of visualizing plastic surgery. I’ve always said no to these jobs, as the stakes are too high to make a mistake! (I think there is more than one company currently developing 3D scanner’s for plastic surgeon’s offices.) I also regularly turn down jobs for copyright reasons. I only agree to do a job if the item to be scanned is an original design, or if they can provide me with written permission from the copyright holder for the design in question.
Nora Toure: As a woman entrepreneur, what is your biggest challenge? Any challenge specific to the 3D printing industry?
Sophie Kahn: I found that when I went to network on meetup.com, most 3D meetups would be a sea of white, male faces. I was so frustrated by this experience actually that I co-founded a group called the Lady Tech Guild, specifically for women in the 3D industry. Our members include artist, educators, designers and animators, and we recently flew to India to teach workshops at Makerfest in Ahmedabad. We run monthly meetups in New York.
Nora Toure: What makes the 3D printing industry particularly interesting for you?
Sophie Kahn: I think there is still an enormous amount of untapped potential in the industry. As with the plastic surgery patients I mentioned above, every job I do is a case study on which a business could be founded. I think that we could reach so many more customers if they were educated on the ways in which 3D scanning and printing can help save them time and money. I also struggle with the assumption that the technology is more advanced than it is; customers seeking quotes sometimes don’t understand that there is no magic machine that will do what they are asking, and their project, in fact, requires 10 or 20 man- (or woman-)hours to accomplish.
If you are interested in learning more about Sophie, I recommend checking Scannerworks NY and the Lady Tech Guild if you are based out of NYC! You can also check her personal website within the following link!
And don’t forget to join the Women in 3D Printing group on LinkedIn and Facebook.
Thank you for reading and for sharing!