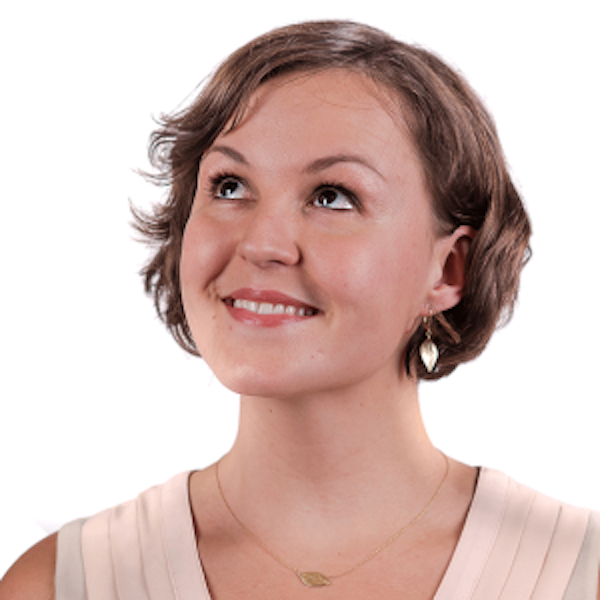
This article originates from Women In 3D Printing and is part of our effort to support the use of 3D printing technology by women. The article is re-published with permission.
Stefani Pellinen-Chavez is a co-founder and the Chief Operations Officer of Ivaldi Group. Her expertise lies in identifying new opportunities and systems to generate higher efficiency and better customer experiences, and in refining existing systems to generate improved outcomes.
A practicing attorney with experience as both CFO, in-house counsel and COO for a variety of startups, Stefani’s most recent role was as co-founder and Chief Operations Officer for Type A Machines, a provider of additive manufacturing equipment and services.
Nora Toure: Stefani, could you let us know about your background and what brought you into 3D printing in the first place?
Stefani Pellinen-Chavez: In 2012 I was just setting myself up as an independent attorney. One of my first clients was Type A Machines and the more time I spent around the other founders, the more awakened I felt to the opportunities built-in to developing a business. I branched out from legal almost immediately. I think my first hands-on project was to redesign the packaging for our Series 1 printer, I took it from a failure rate (think in terms of smashed printers) of 2 out of 3 to 1 in 10 in my first iteration.
Nora Toure: Could you detail your very first experience with 3D Printing?
Stefani Pellinen-Chavez: The first time I heard of 3D printing was in 2006. It sounded like a magic box or Star Trek Replicator and it felt so far into the future that I didn’t really consider that I’d end up ever seeing one. I’m hedging a little because my first and only experience pressing ‘print’ so to speak resulted in filament spaghetti. It was 2012, and I was really excited to print this design, it was for a tissue box loaded with TP instead of single sheet tissues and I thought it would be super convenient. I used Sketch Up to design the object, installed a plugin to export it as an STL, followed our old tool chain to turn that STL into GCode, and finally installed the Arduino drivers on a first gen Windows 8 machine after much fiddling. Not gonna lie, I was pretty disappointed that my print failed, but the feedback I got internally lead me to a very important realization: the company was already well supplied in 3D designers who could optimize my design way faster than I could learn to do it myself. Conversely, there were lots of business needs that we didn’t have covered at the time, procurement, customer support, design for manufacture, bookkeeping, the list goes on. I chose to focus my efforts on those, which is a big part of how I eventually worked my way up to Chief Operations Officer.
Nora Toure: Type A Machines is placing itself on the industrial manufacturing level. Why using desktop 3d printers for manufacturing rather than industrial-grade printers?
Stefani Pellinen-Chavez: ROI baby! As quality improves, the difference between printers that fit on your desk and manufacturing grade printers is narrowing. So if there’s a printer out there that meets you needs in terms of print quality, but costs 4K instead of 40K, why not get one of the 4k printers? Then if your first printer works, why not go ahead and get 9 more and run them in parallel? Different machines run at different print speeds, so you may not get quite ten times the production capability, or who knows, you might exceed it. Ten printers also means redundancy so you can continue to produce while a machine is receiving maintenance. At a tenth of the price, it also means that you can continue to expand your production capability much more affordably than by chosing higher priced “manufacturing” printers.
Nora Toure: Is being a Woman in Tech with no Tech background a struggle?
Stefani Pellinen-Chavez: I’d like to unpack this question a little bit. There are basically two ways to look at it. First, yes I’m a woman in tech, but fundamentally this is a business. There are jobs in businesses for people who work directly on tech and for those who don’t. In terms of my own professional development, I’d call it an advantage that I came to work in tech not on tech. Around the Bay Area and especially in industries that are as exciting as 3D Printing, competition for research, engineering, and design jobs is fierce, and there is no shortage of people with those skill sets who are willing to take the risk of working at a startup. That’s not so much the case for lawyers, communications specialists, accountants, production managers, and other operational roles that a business must have covered to thrive. I think it’s very much the case that startups with very tech heavy founding teams are eager and grateful to have qualified or dedicated non-tech people to help with things like marketing, customer service, bookkeeping, and payroll.
The second way I look at it is like this: especially in the early days, there were often improvements that I wanted to make that I didn’t receive support for – the answer I got was “You can’t do this, we need to hire someone.” I could treat those instances as gender-based doubts about my competence but no one would ever admit to that, so it’s kind of a lost argument. Plus, I was just a lawyer back then. I hadn’t proven my chops. Bit by bit, I started pitching in in ways that others didn’t expect of me and over time, the skepticism about what I was capable of just went away. That’s not to say that there aren’t issues that women face disproportionately, but it helps if you first try to look at how you can bring value and prove to others, but more importantly to yourself, that you have what it takes.
Nora Toure: And so, as a woman working in a Tech industry, what was/ is your biggest challenge? Any challenge specific to the 3D printing industry?
Stefani Pellinen-Chavez: This is a really impactful question for me. I’d say the hardest part of my job is to always put in the effort to make gradual and consistent improvements. As COO, orchestrating a gradual set of measurable improvements to the company is my job. As a female executive and co-founder, I feel a responsibility to take these gradual improvements beyond the strictly measurable. That can often mean helping my coworkers to identify when their actions harm me (sometimes as a woman) or others in subtle and unintended ways. To throw in some tools that I find truly fruitful, I’ll say that I’m talking about using mindfulness to unpack unconscious bias in ways that benefit my employees and my company. The tetchy thing about unconscious bias is that it’s continual and by definition, I’m not aware of it. My employees sometimes describe the aggregation of these continual assumptions that others unintentionally make as “bro culture.”
Preparing for this interview, someone described me as “not afraid to stand up for things.” That’s not exactly what’s happening. As part of an organization, I think all of us will sometimes feel like other people are making assumptions because, well, it could be because I’m a woman, because I’m a lawyer, because I have dogs, or because I’m 5’7, and not even know that they’re doing it. What’s important is that unintended assumptions can result in expectations about things like workplace behavior, interpersonal skills, or reasoning processes, that can negatively impact an employee’s ability accurately communicate. I’ve spoken to women in tech who say it’s not one big thing, but all the little things that add up. For me, in terms of my responsibility to my employees and the company, the biggest challenge is to put in the effort day to day to try to help make sure that those little things don’t get the chance.
Nora Toure: What makes the 3D printing industry particularly interesting for you?
Stefani Pellinen-Chavez: Wow, you know, 3D Printing is a vast open sea of opportunity. I would argue that to date, there still isn’t an IMac of 3D printers – someone, some time, is going to scale that mountain, but right now all of us have the chance to be the company that built that product. The sense of adventure is completely thrilling to me. To switch analogies, it’s also kinda like gold rush, when people who never panned for a single flake made a mint providing services or products for the prospectors. 3D Printing is a little like that too. There are new companies starting up focusing on a single aspect of 3DP Printing hardware, software toolchains, online libraries, you name it.
Nora Toure: Do you have any (fun or not) story about the company to share with us?
Stefani Pellinen-Chavez: After my first maker faire, I was the only person on my team willing to back the UHaul up a 45% San Francisco street and pull perpendicular into our original CEO’s driveway. When I finally got the car parked and opened the UHaul door, the angle was so severe and seats so vinyl, that I had to brace myself against the door to avoid falling out. Street cred for days!
Nora Toure: Anything exciting coming up you’d like us to know about?
Stefani Pellinen-Chavez: I’m deeply proud to announce that going into 2017 Espen Sivertsen and I are venturing into our second advanced manufacturing startup. Ivaldi Group will go beyond the thrill of the tech, that is, 3D Printing for the sake of 3D Printing, to focus on marketable applications for the products made using advanced manufacturing.
Nora Toure: In your opinion, how could we encourage more women to become involved with 3D Printing?
Stefani Pellinen-Chavez: Hire them. I make very specific efforts to encourage women to apply for work in my companies. From the way a job description is written, to where you post it, there are a lot of things employers can do to diversify their applicant pool. I had a staff member poll his friends on a forum when I removed “Perks: ping pong and skateboarding in the office” from a job description he drafted. His friends all agreed that it was better before, and it probably would have been better at getting his friends to apply for the job. On the other hand, for people who are shy of bro culture, adding that to the job description could really limit the diversity of my applicants. Sorry dudes, you’ll have to stop by in person to find out about the ping pong and skateboarding.
If you are interested in learning mo
re about Stefani, Type A Machines or the new Ivaldi Group, I recommend checking the associated websites.
And don’t forget to join the Women in 3D Printing group on LinkedIn and Facebook!
Thank you for reading and for sharing!