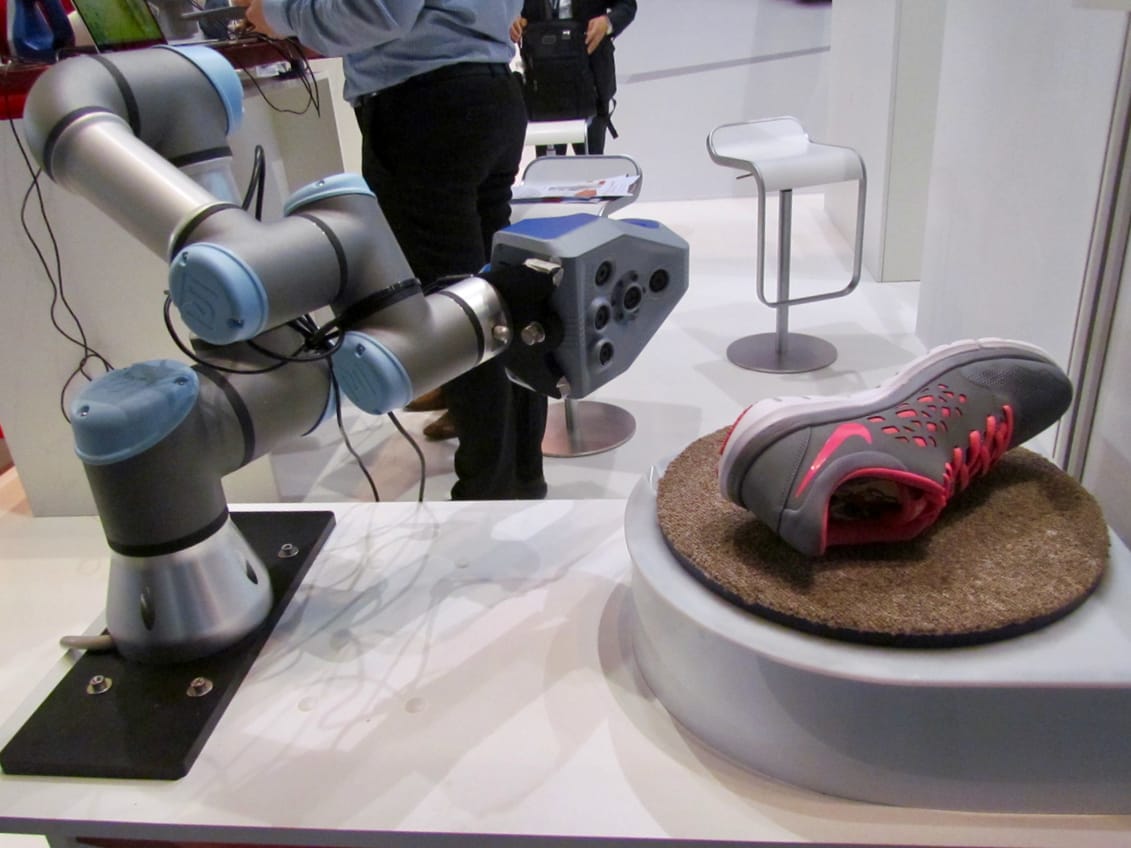
I had a thought about the implications of increasing levels of production 3D printing.
Production parts are typically for end-use purposes, that is they will be used in real-life application situations. They must perform to specifications as intended by the partsā designers. If not, the maker may be liable for unexpected outcomes from using the part.
For that reason production lines frequently involve quality inspection systems. The function of such systems is to physically inspect a freshly made part using various sensors and compare the data with what one would expect to see from a part that meets quality standards. The sensed data would have to be within specified tolerance levels to pass the test.
Such tests could involve a variety of sensor types, including optical for color and surface finish, or even tactile sensors. But the most common process, at least for 3D printed parts, would be a 3D scan.
In this process, a completed part is presented to a 3D scanning system, which uses lasers, structured light or other optical means to capture a 3D digital representation of the completed part.
This digital representation is then compared with the actual 3D design model in rapid fashion, and any deviances from the intended design are noted. Should any portion of the part – or perhaps any CRITICAL portions of the part – are off the tolerance window, the part can be rejected.
This is very important, as such a rejection allows the operator to diagnose a problem and tweak the 3D print job to bounce the prints back into the quality envelope. You donāt want to run a machine and find a large percentage of the prints awry.
This all makes sense, but we have to consider that there are an increasing number of production parts coming out of 3D printers these days. Stratays in particular has been focusing on developing ways for production 3D printing to be automated and scaled up, while 3D Systemsā new Figure 4 system will print volumes of parts as well. Other companies are developing similar systems.
But there are two ways to accomplish quality control: automated or manual.
The manual approach is straightforward, but undesirable. An operator manually 3D scans completed parts with a handheld or table top 3D scanning system, and awaits the results. While this approach could be easily set up for an initial production approach, itās hugely expensive as you must provide the labor to operate it continuously.
On the other hand, automated 3D inspection systems are perhaps a more practical way forward. In this approach, the 3D prints are delivered to a 3D inspection system that automatically can scan and evaluate the parts, sorting them into categories.
The good news is that there are many such systems available in the market today. Why? Because part inspection is not something unique to 3D printing: ANY part made with ANY process could require inspection, and thatās something thatās been done for decades.
It seems to me that those 3D printer companies wishing to get involved in true production may want to consider directly integrating with existing part inspection systems if they hope to speed up the integration of 3D printing technology into todayās production systems.