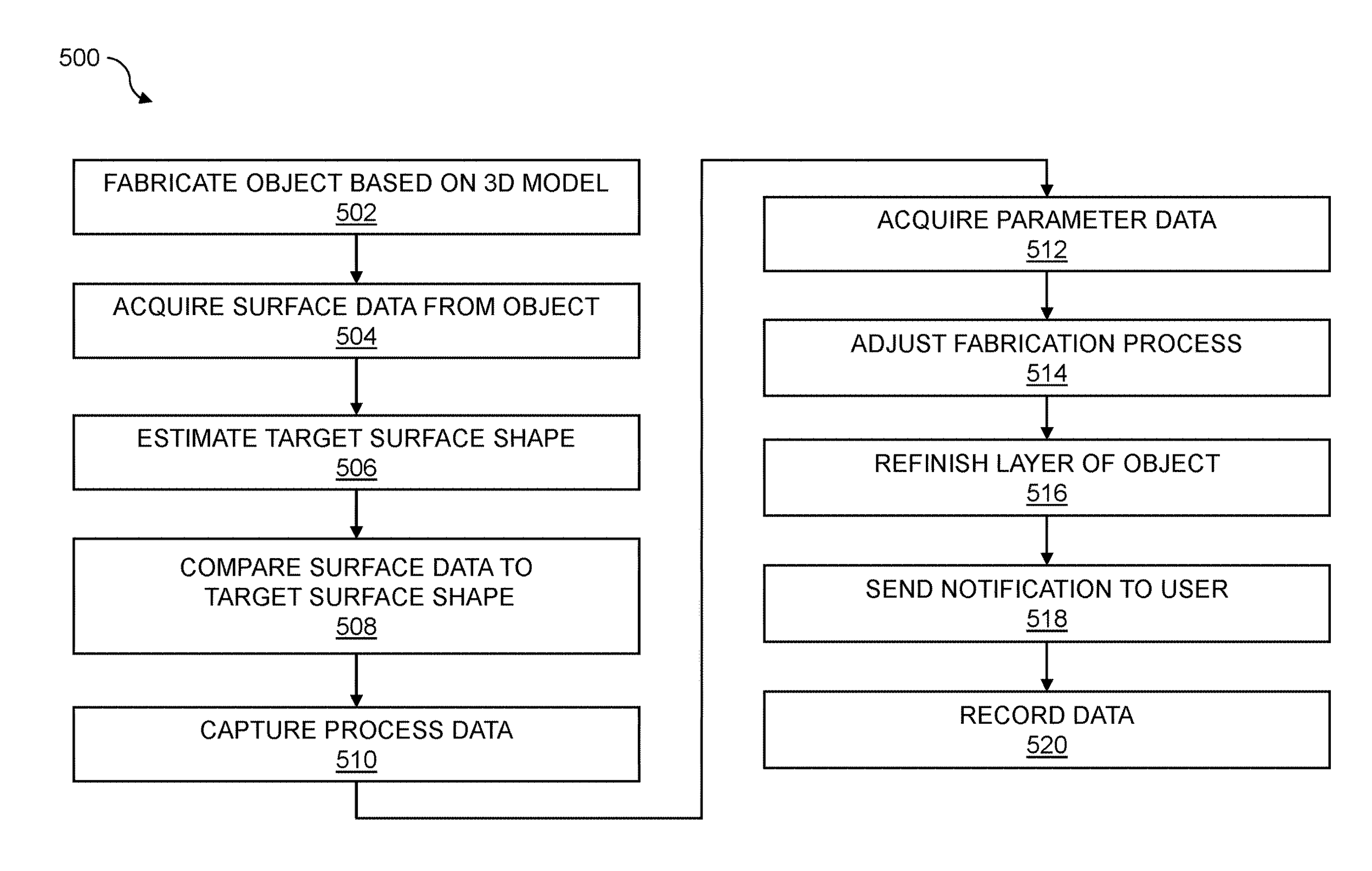
I’m trolling through patents and found an interesting application from Desktop Metal, who propose a way to perform real time quality control.
Desktop Metal recently (and finally) announced their product line, which includes new technology for low cost production metal 3D printing. Their announcement has gathered a great deal of attention as the current methods of 3D metal printing tend to be quite expensive in both equipment, facilities, materials, processing and operating expertise.
A new method of inexpensive 3D metal printing would be extremely attractive to many current users of 3D metal printing, and enable new users who could not previously afford the expense of setting up a proper 3D metal printing workshop.
However, there is a nagging question: would the printed objects from Desktop Metal’s equipment be of sufficient quality for use in real applications?
This is important because many of the current users of 3D metal printing are now producing critical metal parts for industry. In the aerospace industry, for example, parts must be tracked individually and exhibit all the properties specified by their designers. If the parts cannot be certified and tracked, they cannot be used in aircraft.
Desktop Metal believes their parts are of good quality, but then there’s this patent, US Patent Application no US20170056967A1, entitled, “CONTROL OF METALLIC ELECTROHYDRODYNAMIC THREE-DIMENSIONAL PRINTING USING FEEDBACK OF SURFACE CHARACTERISTICS”.
Here’s the abstract from the patent:
A metallic electrohydrodynamic (EHD) three-dimensional printer fabricates an object while surface characteristics of the object are monitored. Sensors acquire data on surface characteristics, and feedback related to these surface characteristics is used to adjust the fabrication process, e.g., where the surface characteristics deviate from a target surface shape.
Aha! This is a way to perform quality control during printing operations. It seems they will (or perhaps already have) included sensors in their equipment that could perform this type of action.
Here’s more about how this could work:
The metallic liquid expeller may be configured to drive the droplets of liquefied metal by applying an electrostatic field to a meniscus of the liquefied metal extending from an outlet of the metallic liquid expeller of the printer. The surface data may be acquired for each one of the droplets of liquefied metal. The surface data may be acquired for a surface region about the location. The surface data may be acquired for a voxel about the location. The method may further include capturing process data characterizing the droplets of liquefied metal.
They provide a long list of potential sensors, including: volume of droplets, droplet dimensions, droplet velocity, droplet distance, environment heating, contact profile and more.
The analysis of these sensor readings should permit Desktop Metal to quickly adjust the machine operation to correct any deviations.
This could be a powerful advantage allowing Desktop Metal to compete on quality aspects with their larger and more established competitors, who only recently have begun to include quality control – or even just quality monitoring – features into their equipment.
Via Google Patents