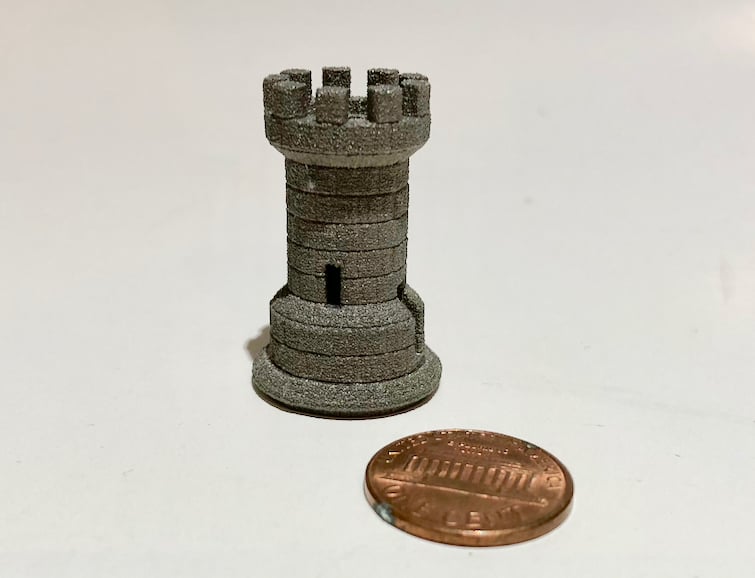
There’s something fascinating about underdogs in any race, something that attracts your attention.
In the race to 3D metal printing supremacy, there are many players, some of which are enormous intergalactic conglomerates with essentially unlimited cash to compete. There are others that are far less equipped, but nevertheless they compete well.
One of them is Australia’s Aurora Labs, who produce a powerful 3D metal printer that is capable of producing high quality 3D metal parts at pricing far less than most, if not all of their competitors. Their prime product, the S-Titanium Pro, is directed at research institutes, and offers a 200 x 200 x 500mm build volume. The machine is capable of 3D printing in up to three different powdered metals at once, and costs only USD$49,999.
In spite of their incredible price and excellent quality parts (as seen in the sample print at top) they have a stiff uphill battle against the established players in the 3D metal printer market, such as EOS, GE and 3D Systems, each of whom have massive sales networks and far larger marketing budgets. On the low end, startups such as Desktop Metal and XJET have been attracting much attention due to their lower pricing and different processes, leaving Aurora Labs in a challenging position to attract attention.
But that doesn’t stop inventive people such as those manning Aurora Labs. They’ve taken a very unusual step towards success that seems quite different from the other market players.
Rather than spending time and money building up a large sales network, they’ve integrated with the market directly. Their recent deal with WorleyParsons is far more important than I had realized, after a discussion with representatives of Aurora Labs and WorleyParsons.
Who is WorleyParsons? They happen to be a very large Australian professional engineering firm that designs very large projects in the hydrocarbon, power and mining industries. They build large infrastructure in worldwide locations, even deep under the ocean.
Their first venture with Aurora Labs is entirely fascinating, as it deals with a major issue in the mining industry that I hadn’t understood previously.
Let’s talk about mining. It’s a highly mechanical business, with plenty of metal parts employed in the increasingly automated business of extracting materials from the Earth. It’s also a massive industry with countless mines around the world.
These mines operate continuously, and in a sense the goal is to operate the machinery 24×7 to gain the best return from the infrastructure investment. Downtime is a very bad thing, and is measured in money. WorleyParsons explained that a typical, average-sized iron mine might cost close to USD$40K PER HOUR when down.
Thus it is critically important to keep the mine going, and almost any expense is required to do so. This is done today by storing countless numbers of spare parts at each mine, each ready to be installed on a moment’s notice to get the mine restarted when failure occurs.
But there’s a big challenge here. There are many kinds of parts. They are almost always made of metal, and are very large and very heavy.
And the mines are inevitably located in extremely remote areas that almost always do not have suitable roadways on which to deliver these spare parts. Heavy metal parts are often delivered by air with helicopters at enormous expense.
Worldwide, mining companies currently store multiple billions of dollars of spare parts at mining sites.
That is an astonishing amount of money, and it will increase over time due to changes in mining technology and the opening of additional mines.
This is the concept from WorleyParsons and Aurora Labs: They want to deliver a 3D metal printer to EACH mine so that many replacement parts can be 3D printed onsite. This reduces the inventory cost very significantly, even if a 3D printed part might individually be more expensive than one from the factory.
But to do so, Aurora Labs won’t be sending their current model to the mines. Instead they are developing a large format 3D metal printer that employs an “entirely different technology”. Their target is a machine that can deliver a one tonne metal part in less than 24 hours.
Such parts need not have extreme resolution, but merely have to be “good enough” to get the mine going again. It’s possible a proper factory replacement part might arrive later to take over, but that’s still far less expensive to do than keep ALL of the spare parts onsite.
To me this seems to be an incredibly valuable business case that should be addressable by 3D printing. However, I don’t believe any other 3D metal printer manufacturer is working on this issue, perhaps due to the extreme environmental costs of setting up a typical powder-bed metal printing system.
For Aurora Labs this could be a rocketship to success; there are an awful lot of mines in the world, and a company like WorleyParsons can certainly make the necessary connections.
But that’s just mines. There are dozens of other heavy industries that would have similar issues, such as oil & gas, rail, shipping. The opportunities here are staggering.
To address this, WorleyParsons and Aurora Labs are apparently opening a demonstration center in which they can educate industry representatives on these concepts.
The future looks bright for Aurora Labs if they can produce the new heavy-duty 3D metal printer.
Via Aurora Labs