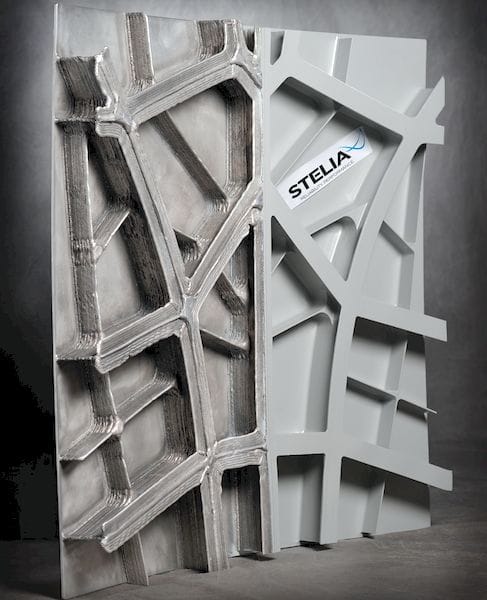
Aerospace has long been interested in 3D metal printing, but it seems a milestone may have been hit.
There are two types of parts in an aircraft: “flight critical” and “everything else”. While there has been plenty of activity in the aerospace sector in 3D printed parts, virtually all of it relates to the “everything else” category.
Stratasys, for example, is developing systems and software to enable 3D printing of interior walls. That’s a fabulous idea that should save aircraft manufacturers significant amounts on spare parts inventory, but the interior wall panels are not exactly flight critical.
Use of 3D printed flight critical parts would require significant levels of certification, obviously, as any mistakes could result in catastrophic events, lawsuits and financial situations.
Now I see a release from Stelia Aerospace, a very large French company that “designs and produces aerostructures, pilot seats and business and first class passenger seats”. The release describes a technique they’ve used to produce “metallic self-reinforced fuselage panels”.
I don’t know about you, but I suspect that fuselage panels could very likely be flight critical parts.
Their process uses Wire Arc Additive Manufacturing (WAAM), which essentially is pushing a wire through an electric arc to melt it, while moving the melt point in 3D space with a robotic arm to deposit the meltpool on a surface in an additive manner.
It’s definitely not a layer-by-layer 3D printing process as is often seen in these pages. But it is an additive process.
Stelia Aerospace appears to have deposited a reinforcing structure on the inside of what is otherwise a standard fuselage panel with WAAM. This provides a way to apply constantly varied reinforcement shapes to panels without having to produce the traditional parts.
I think the key here is varied. If every fuselage panel on an aircraft were made in this way, then I suspect that each panel could have a different reinforcement structure to match the expected forces on the panel in that particular part of the aircraft.
I’m not sure if this is done in traditional aircraft assembly approaches, but if so it could be expensive to produce unique reinforcement structures. Designing and printing them as required could be a much better approach.
This could result in aircraft with lower weights, but maintaining the same engineering strengths.
Stelia explains they’ve been working on this processs for 2 and a half years, but now were able to produce a unit. It’s not clear whether this will make it into their regular production, but at least this is a very good first step.
Via Stelia