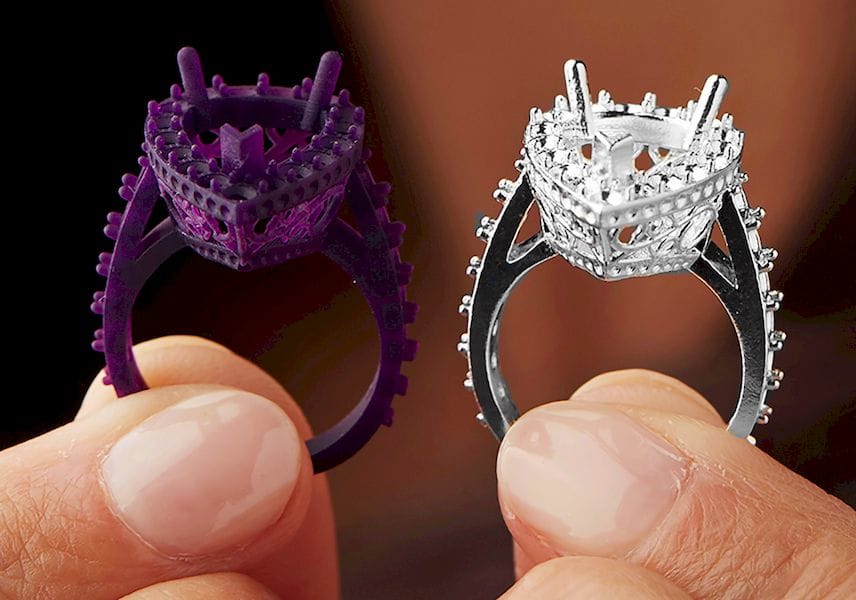
Formlabs announced they’re now shipping a new castable wax resin.
The new material, designed for use in their popular Form 2 3D printer, is specifically for casting applications. The material takes on the role of “actual wax” in the lost wax process.
That process involves first producing a replica of the object in a castable material, in our case by 3D printing the object. Then this “positive” object is surrounded by a casting material, like plaster. The key is that this surrounding material is able to withstand heat to a higher degree than the object’s material.
An application of heat melts the object, leaving a void in the exact shape of the original object. Into this void can be poured other high temperature materials like liquid metal, for example. After cooling, the surrounding casting material is removed to reveal the final object.
It’s a very common process, and even one that’s been used in 3D printing. However, the problem is that most 3D print materials leave a residue when they are heated. PLA is sometimes used in this regard, but the residue is such that you can’t expect extremely fine details to be accurately represented in the final object, since the ash residue prevents the liquid metal from fully exploiting the void.
Jewelers often use high-priced wax 3D printers to produce castable objects in near-pure wax, similar to their traditional processes. There are some resin 3D printer manufacturers that produce materials with similar qualities, but they tend to be quite expensive and are thus beyond the financial capability of most jewelers.
Formlabs has had a history of introducing high quality 3D printing to new industries due to their very low priced equipment, when compared with traditional resin 3D printing equipment. Now they may have a chance to do this to a much deeper degree in the jewelry industry with their new resin.
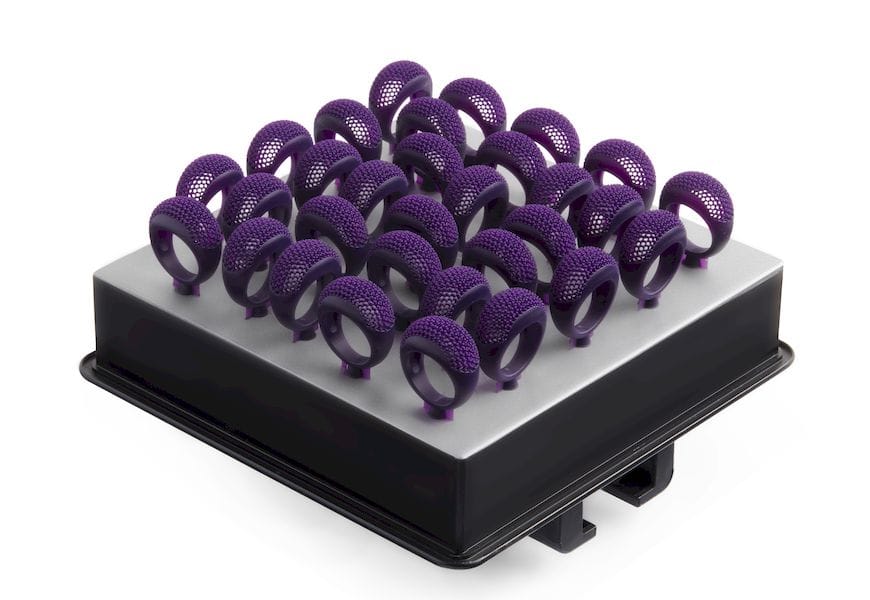
The new resin is ”Castable Wax Resin”, and it adds to their already existing portfolio of jewelry-focused resins. They already market a castable resin, but it isn’t a wax type, but the new wax-style resin will be far more familiar to jewelers. They say:
This wax-filled material is designed for reliable direct investment casting with zero ash content and clean burnout. Printed parts are suitable for both custom try-ons and final production.
And
Highly detailed and challenging jewelry is complicated to produce by hand, and in a world driven by high demand and fast fashion, it can be difficult for hand-crafted pieces to keep pace.
Castable Wax Resin was formulated to set the standard for print quality on an affordable desktop 3D printer, combining the smooth surface finish that stereolithography (SLA) 3D printing technology is known for with increased part strength and precise print settings to capture astonishingly sharp detail.
Accurately capture fine features, like raised text, delicate filigree wires and meshes, and detailed pavé, with no visible layer lines.
The new material is actually made from 20% real wax, and offers up to an eight our burnout turnaround, which should work well with many jewelers.
There are some caveats with this material, as Formlabs publishes documents describing the best practices. For example, larger builds will require longer burnout periods.
I feel this is a very strong update for Formlabs, as they have produced what appears to be a material that very precisely matches the needs of a particular application group. This should boost their sales capability in that market strongly, and certainly put a scare into the higher priced jewelry 3D printing option providers.
Via Formlabs