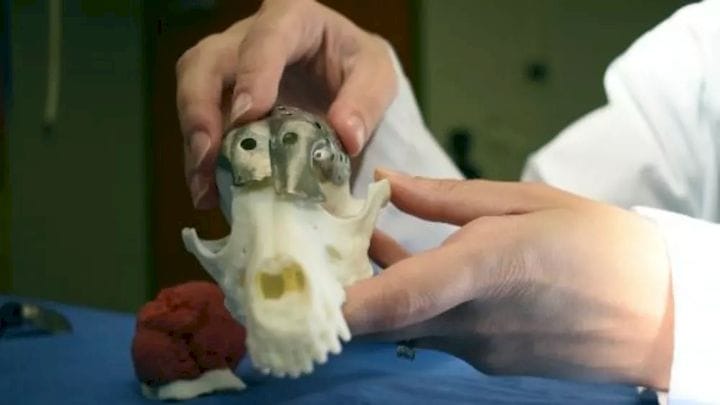
Every dog has his day.
For Patches the dachshund, it was the day she received lifesaving surgery to replace part of her skull with a custom 3D-printed titanium plate. Patches had developed an orange-sized tumor that had started to grow through her skull, and that would have eventually been fatal if it werenāt for the intervention of a team helmed by researcher Michelle Oblak.
āThe technology has grown so quickly, and to be able to offer this incredible, customized, state-of-the-art plate in one of our canine patients was really amazing,ā said Oblak, who is examining cancer in dogs as a model for human cancer. She believes that this surgery technique could one day be used to help humans.
The surgery process started with a CT scan of Patchesā head. After that, Oblak teamed up with the University of Guelphās rapid prototyping of patient-specific implants for dogs (RaPPID) working group, a team that develops 3D-printed dog implants. Together, they mapped the tumorās location and size, and performed a ādigital surgery,ā in which they removed the tumor to see how much of the animalās skull they would need to remove.
The model showed that they would need to remove approximately 70 percent of Patchesā skull. With the digital tumor and the diseased portion of the skull āremoved,ā the team was able to develop a 3D-printed model of what a skull implant would look like, including holes for screws to hold the implant in place.
Generally, when removing a brain tumor, the surgeon needs to wait until the section of the skull has been removed to create the implant, and then has to shape titanium mesh into an implant during the surgery.
The 3D modeling meant the team could perform the step in advance, shortening surgery time. āI was able to do the surgery before I even walked into the operating room,ā Oblak said of her method.
After the team developed the digital model of the skull implant, Oblak sent the plans to ADEISS, a 3D printing company in London, Canada. ADEISS specializes in titanium-printed medical implants for humans, so Oblak worked with them to ensure they could craft an implant that would work for Patches.
She also developed a ācutting guideā for the surgeon to follow; a deviation of millimeters would have meant that the implant wouldnāt have fit.
Read more at ENGINEERING.com
FELIXprinters has released a new bioprinter, the FELIX BIOprinter, which is quite a change for the long-time 3D printer manufacturer.