![The Sliding-3D caught a lot of attention at formnext 2018 [Image: Fabbaloo]](https://fabbaloo.com/wp-content/uploads/2020/05/IMG_20181116_140521_img_5eb0a14746ead.jpg)
Lumi Industries and Robotfactory remind us that the maker spirit endures in 3D printing even as the technology industrializes.
There’s a reason that so many of today’s engineers remember the LEGO and Tinker Toy sets they played with as kids: playing to create helps to bring ideas to life. That drive to play, to make a thought into a tangible creation, is still very much in evidence throughout the 3D printing industry, and these two Italian companies are an excellent highlight of this spirit.
“We are always full of ideas, maybe too many ideas,” Lumi Industries Co-Founder Manuela Pipino told me with a laugh. “We are very ambitious and we enjoy presenting so many ideas. Maybe by presenting them we will find someone to help with the next steps.”
At the booth Lumi and Robotfactory shared at formnext, these ideas were on full display from viable 3D printers to intriguing prototypes to posters showcasing more ideas in the pipeline.
![The tablet-based Lumifold TB 3D printer at formnext 2018 [Image: Fabbaloo]](https://fabbaloo.com/wp-content/uploads/2020/05/IMG_20181116_140636_img_5eb0a147dce3f.jpg)
The foldable Lumifold TB 3D printer has intrigued us for a few years now, and was a highlight at Lumi’s display as a final prototype. With a goal for commercialization in 2019, the tablet-powered Lumifold is an interesting idea: why would we need (or want) a foldable 3D printer?
“No one is really thinking about portability in 3D printing. Now we are like computers in the 1950s with big systems, but today we have laptops, there is more usability, it is easier to help people understand,” Pipino explained. “There is still some ignorance about 3D printing — not here [at formnext], but at Maker Faire, in movies like Ocean’s 8. People do not understand still.”
A smaller 3D printer is easy to transport to Maker Faire events, to classrooms, to expose new audiences to a technology that’s beginning to pick up more notice. Storage is also easier, as the Lumifold can just be folded up when not in use, not taking up desk space in an office or classroom.
The company has also had requests for a foldable 3D printer using filament, as the current version is a resin-based system.
An eye-catching prototype system also drew visitors as the Volumetric Vibrating Device (VVD) allows for full 3D visualization of a model from all sides without the need for 3D glasses.
![A look at the jawbone visible on the VVD at formnext 2018 [Image: Fabbaloo]](https://fabbaloo.com/wp-content/uploads/2020/05/IMG_20181116_141324_img_5eb0a148700b6.jpg)
“This is a full preview, respecting size and proportion. With this device you can explore every point of view, and many people can view it at once,” Pipino said. “This could be used maybe in the medical space. We are looking for companies to help develop it.”
The photos/video I took of the VVD don’t do it justice, but fortunately Lumi provides a better virtual look at the visualization, the same jawbone on display at formnext:
![[Image: Lumi Industries]](https://fabbaloo.com/wp-content/uploads/2020/05/vvd_img_5eb0a1493741f.gif)
A poster on the wall shared another idea from Lumi, a side project for sustainable 3D printing. The SOLL-E idea is an autonomous fabricating unit using light to build structures: “Use only sand and sun,” Pipino said.
![Manuela Pipino examines the SOLL-E concept at formnext 2018 [Image: Fabbaloo]](https://fabbaloo.com/wp-content/uploads/2020/05/IMG_20181116_141455_img_5eb0a1498ac34.jpg)
Experimentation has led to a small proof of concept, and Lumi is looking for companies that might be interested in cooperating to take this idea to its next levels.
On the other side of the booth, Robotfactory showcased its Sliding-3D, which uses an angled extruder and conveyor belt for ‘infinite’ 3D printing.
CEO and Founder Andrea Martini shared a look at the 3D printer, which took home a blue ribbon from Maker Faire Rome.
“It needs very little support, and if you break the support surface it is still very, very beautiful. It avoids traditional FDM issues — it is possible to have a structural part,” Martini explained. “It also saves energy, printing at half the time of other 3D printers.”
![The Sliding-3D at work at formnext 2018 [Image: Fabbaloo]](https://fabbaloo.com/wp-content/uploads/2020/05/IMG_20181116_142016_img_5eb0a149e1a0f.jpg)
Benefits in surface finish and avoiding delamination issues could be seen in the parts coming off the running system. Martini sent me home with a small part, which has a smooth surface and shows not a single ding from its time in my very full conference bag through formnext and the international travel home.
Below we see a direct comparison of the same print 3D printed on a standard FDM machine (right) and on the Sliding-3D (left).
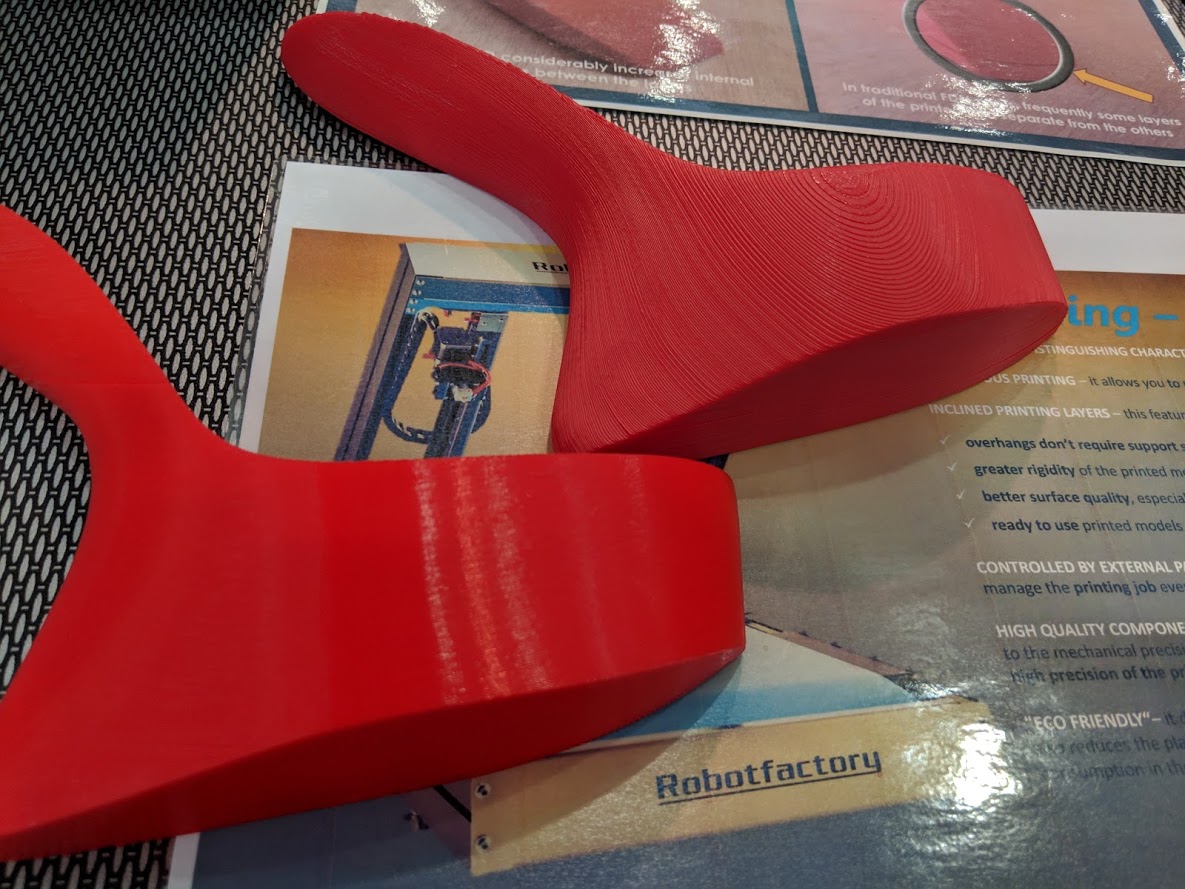
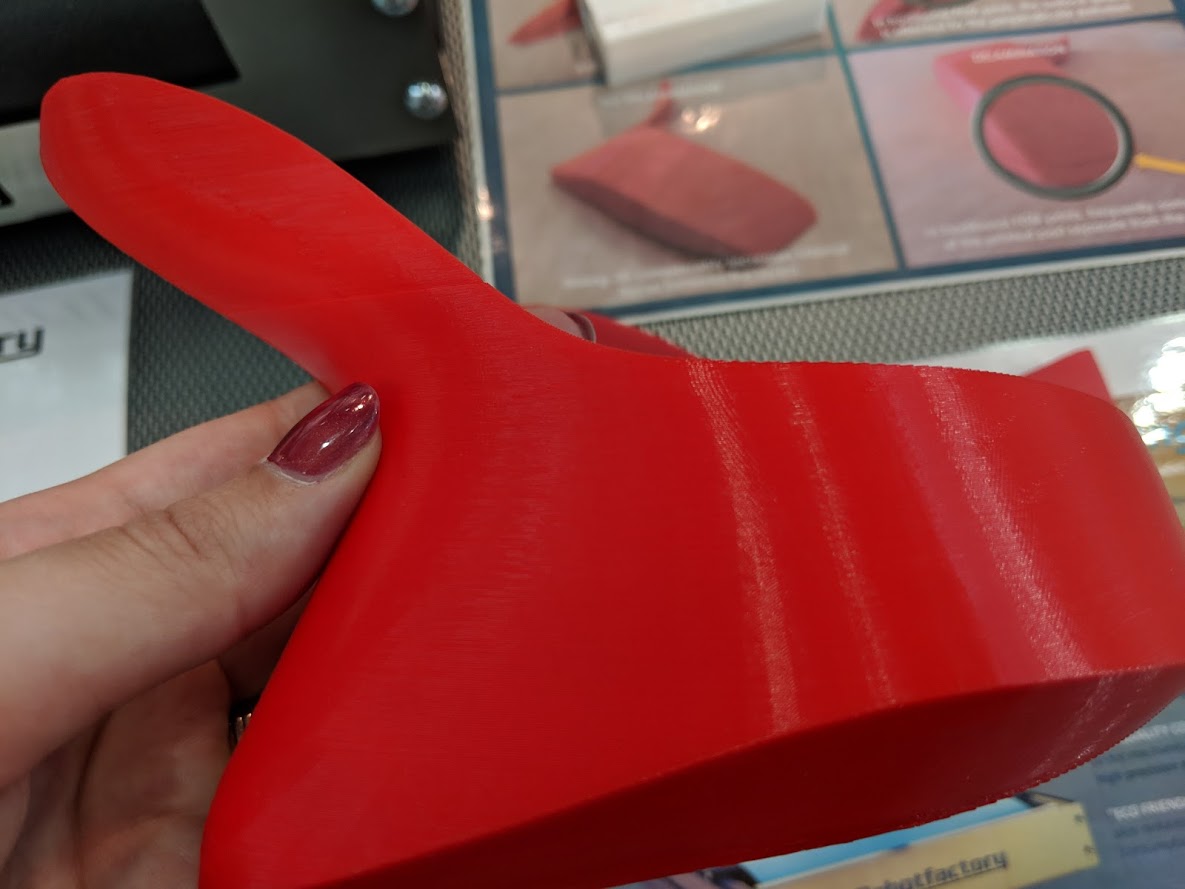
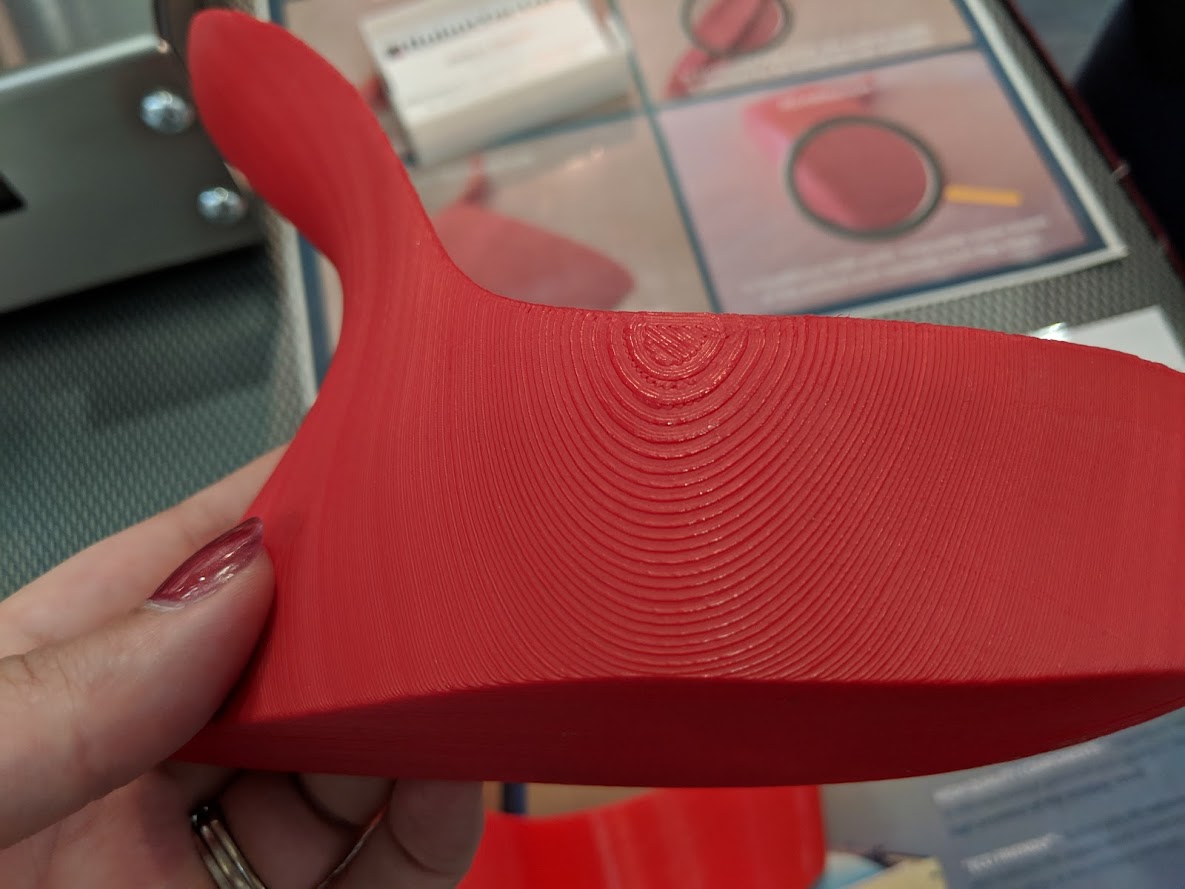
Infinite build 3D printing is picking up some traction — as is a renewal of the notion that we need to keep playing with different techniques and technologies to continue to advance.
Bringing new ideas to the table and trying them out is invaluable to the creative process. Not every idea will be a commercializable winner (we’ll see if SOLL-E takes off), but actually making the mechanics work to advance new angles, new ways to see (and to visualize, à la VVD), and to get technologies into new hands is what keeps this industry moving forward.
While 3D printing is often used in prototyping, the development behind the 3D printers is obviously an important process itself — and new ideas are always welcome.
Via Lumi Industries and Robotfactory
The 3D printing industry is fast-changing. Sometimes taking a step back, though, is necessary to grasp the bigger picture.