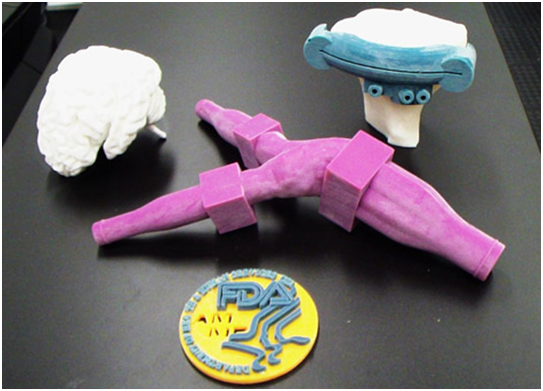
The medical device industry is one of the largest and fastest growing global markets. Charles Goulding and Preeti Sulibhavi examine the growing integration of 3D printing in this area.
MedAccred is a core Performance Review Institute (PRI) Program that is aligned with the FDA Case for Quality Initiative. MedAccred includes approximately 40 active medical device companies in addressing various industry challenges regarding quality in specific technology areas, such as batteries used in medical devices and sterilization of equipment. MedAccred Audits are essentially production and process assessments.
MedAccred focuses on the following core manufacturing processes involved in the production of medical devices:
-
Cable and Wire Harness
-
Heat Treating
-
Plastics – Extrusion
-
Plastics – Injection Molding
-
Plastics – Mechanical Assembly
-
Printed Circuit Board Assembly (PCBA)
-
Sterilization
-
Sterile Device Packaging
-
Welding
-
Printed Boards (Bare Boards)
There are many reasons to become MedAccred-ited. It is vital to the goal of companies looking to improve quality and reduce risk; it helps align expectations and provide visibility to all tiers; the potential of becoming a preferred vendor for subscribers such as Stryker and Johnson & Johnson; and, demonstrating a clear commitment to continuous improvement.
Leading MedAccred Participants
MedAccred subscribers include: Baxter, Becton Dickinson & Co., Boston Scientific, GE Healthcare, Global Technologies, Johnson & Johnson, Medtronic, Philips Healthcare, and Stryker. These are all key players in the healthcare industry. To be accredited by MedAccred can in some instances make a supplier a preferred supplier or awarded new business based on accreditation alone. For example, Stryker has indicated that MedAccred vendors are preferred. Scott Goolsbey, manager of supplier controls for the device giant’s endoscopy division, told Medtech Insight that Stryker will eventually grant business based on whether suppliers are certified to MedAccred.
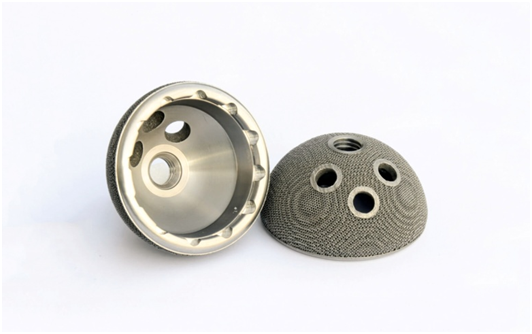
The use of continuous, innovative procedures and processes that utilize 3D printing can help MedAccred, its subscribers and suppliers receive R&D tax credit incentives as well as a safer and streamlined supply chain for medical devices.
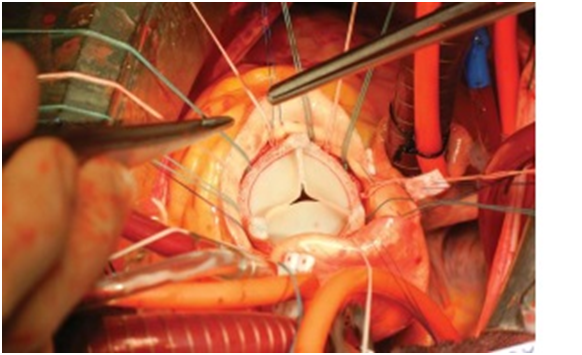
The Research & Development Tax Credit
Enacted in 1981, the now permanent Federal Research and Development (R&D) Tax Credit allows a credit that typically ranges from 4%-7% of eligible spending for new and improved products and processes. Qualified research must meet the following four criteria:
-
Must be technological in nature
-
Must be a component of the taxpayer’s business
-
Must represent R&D in the experimental sense and generally includes all such costs related to the development or improvement of a product or process
-
Must eliminate uncertainty through a process of experimentation that considers one or more alternatives
Eligible costs include U.S. employee wages, cost of supplies consumed in the R&D process, cost of pre-production testing, U.S. contract research expenses, and certain costs associated with developing a patent.
On December 18, 2015, President Obama signed the PATH Act, making the R&D Tax Credit permanent. Beginning in 2016, the R&D credit can be used to offset Alternative Minimum tax for companies with revenue below $50MM and for the first time, startup businesses can obtain up to $250,000 per year in payroll taxes and cash rebates.
What This Means for MedAccred and the Medical Device Supply Chain
Surprisingly missing from the MedAccred supply chain are 3D printing/additive manufacturing companies. With continuous innovation comes continued growth. 3D printers offer lightweight construction and feature complex geometries that injection molding (a MedAccred category) would not be able to create. They would also be more cost-effective.
MedAccred could also leverage the fact that 3D printing technology has already begun to be widely used in the healthcare industry. Orthopedic and cranial implants, surgical instruments, dental restorations (e.g., crowns) and external prosthetics have all been created using the versatility of 3D printing. In fact, the Food and Drug Administration (FDA) regulates medical devices through its Center for Devices and Radiological Health (CDRH). MedAccred would have the guidance and regulations established by the FDA as a guide in 3D printing its medical devices to use in its existing supply chain. Perhaps MedAccred should designate 3D printing as one of its core manufacturing technologies.
MedAccred, as well as 3D printing/additive manufacturing companies, have a unique opportunity at this juncture. This is a burgeoning market and on the East Coast, the state of New Jersey has one of the largest medical devices supply chains in the world. The New Jersey statewide MedAccred expert at New Jersey Manufacturing Extension Program, Inc. (NJMEP) is Peter Russo ([email protected]).
In addition to batteries and software, PRI has announced that the following are critical-process areas that might eventually be added to MedAccred:
-
Additive Manufacturing
-
Assembly
-
Casting/forging
-
Chemical processing
-
Cleaning
-
Coatings
-
Counterfeit parts
-
Electronic displays
-
Fluidics
-
Machining
-
Material-testing laboratories
-
Measurement/inspection
-
Nondestructive testing
-
Optics
-
Packaging
-
Power sources
-
Raw materials
-
Reagents
Conclusion
In taking the next steps and having 3D printing companies in its medical device supply chain, MedAccred, its participants, suppliers and its subscribers could also benefit from R&D tax credit incentives as it improves its processes and procedures.
FELIXprinters has released a new bioprinter, the FELIX BIOprinter, which is quite a change for the long-time 3D printer manufacturer.