![3D printed gowns and accessories at the 2019 Met Gala [Image: Getty Images]](https://fabbaloo.com/wp-content/uploads/2020/05/GettyImages-1147450488-lrg_img_5eb097fd07b8c.jpg)
3D printed fashion added to the extravaganza that is the Met Gala this year.
Last night, “fashion’s biggest night out” brought A-listers together at the Metropolitan Museum of Art. The annual event is a pretty big deal; the benefit always raises not only funds for the Met, but eyebrows at the audacious garments and capital-L Looks.
It’s one of those very “It’s fashion, dah-ling” types of events that, each year, proves I know nothing about fashion. At all.
Designers like Zac Posen, in stark contrast, do know fashion.
The Met Gala is a designer’s dream: a platform to showcase their creativity on a major world stage on some of the best-known faces in art, design, music, theatre, and silver screen. Granted most of my experience with the Gala came from watching Ocean’s 8 last year, during which I was mostly distracted by the questionable use of 3D scanning / 3D printing.
Fortunately for this year’s Gala, the 3D printing was both real and legal.
The 2019 theme was “Camp: Notes on Fashion”, which, well, not everyone necessarily understood immediately. The name plays off writer Susan Sontag’s 1964 essay, “Notes on Camp.” Essentially, ‘camp’ can mean whatever you want it to mean, but comes down to something like Sontag’s description: “style at the expense of content.” So, style it is.
Posen and his creative team came up with a concept for a collection that essentially froze the movement of natural objects, and turned to digital technologies to turn that vision into wearable realities. Key to the project was collaboration, and Posen turned to some solid choices in partners, teaming up with GE Additive and Protolabs to realize the concept.
“I dreamt the collection, GE Additive helped engineer it and Protolabs printed it,” said Posen.
In all, that collaboration resulted in four elaborate gowns and a delicate headdress, all highly engineered and featuring 3D printed pieces.
![A lot of engineering went into the 3D printed rose gown, worn by Jourdan Dunn [Image: Zac Posen / GE Additive / Protolabs]](https://fabbaloo.com/wp-content/uploads/2020/05/ManufacturingTheRose_InfographicMay3REV_img_5eb097fd6e66d.png)
3D printers located around the world — for the most part at Protolabs’ dedicated 3D printing facility in North Carolina, but also at that company’s facility in Germany, and one titanium cage made at the Cincinnati-based GE Additive Technology Center — turned the designers’ sketches into tangible pieces.
The pieces were worn by some big names.
Supermodel Jourdan Dunn wore a hefty rose gown comprised of 21 SLA-3D printed unique petals, each about 20” long and weighing in at a pound. The petals are attached to a titanium support cage 3D printed on a GE Additive Arcam EBM machine. Altogether, manufacturing and finishing this design was a 1,000-plus-hour endeavor.
![Jourdan Dunn in the elaborate and weighty rose gown [Image: Getty Images]](https://fabbaloo.com/wp-content/uploads/2020/05/GettyImages-JourdanDunn1147440047-lrg_img_5eb097fdd7210.jpg)
Actress Nina Dobrev was outfitted in a clear dress with a custom clear bustier, 3D printed on an SLA system with Somos Watershed XC 11122 material. This 200-hour creation was the one made in Germany.
![Nina Dobrev in the clear 3D printed creation [Image: Getty Images]](https://fabbaloo.com/wp-content/uploads/2020/05/GettyImages-NinaDobrev-1147432950-lrg_img_5eb097fe2eed9.jpg)
Actress Katie Holmes’ creation brought a purple palm leaf collar to a purple fabric dress of Posen’s design. The structured piece was 3D printed in Accura 60 material on an SLA system, made and finished in 56+ hours.
Actress Julia Garner’s Posen gown — admittedly my favorite of the designs, and itself not 3D printed — was topped with an MJF-made headpiece. The elaborate vine design was made in one piece in Nylon 12, then brass plated. Its creation took just under a full day, clocking in at a bit more than 22 hours.
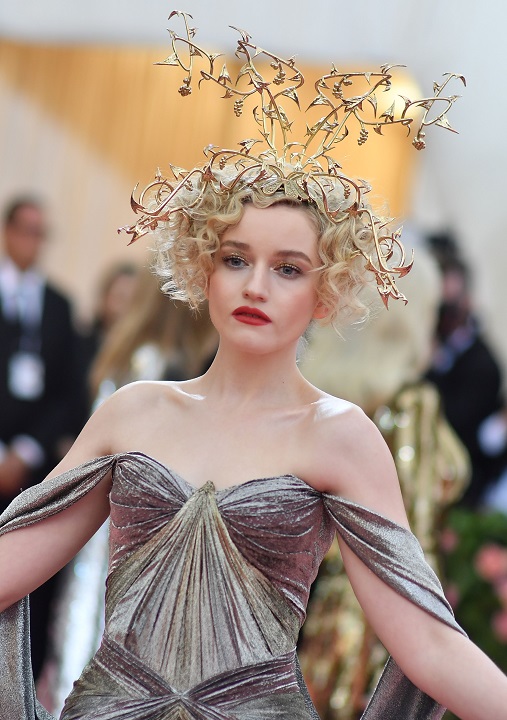
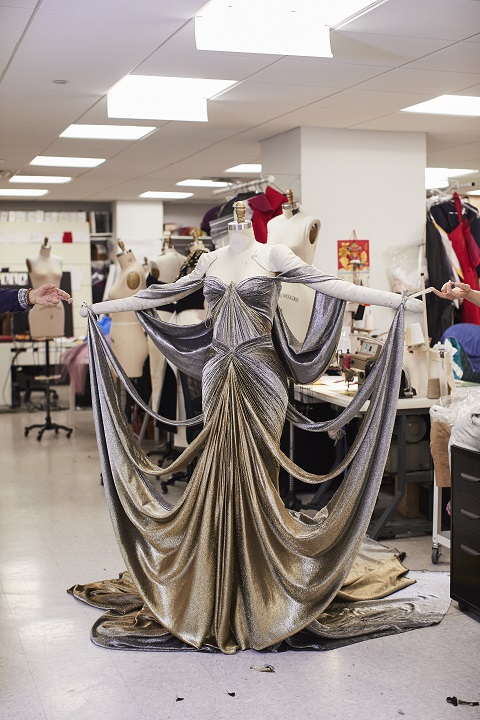
[Images: Getty Images]
Bollywood’s Deepika Padukone wore a gown with elaborate 3D printed embroidery. The 408 pieces were 3D printed in Accura 5530 on an SLA system, then sewn onto her Posen gown. The hundreds of pieces for the embroidery detail took more than 160 hours.
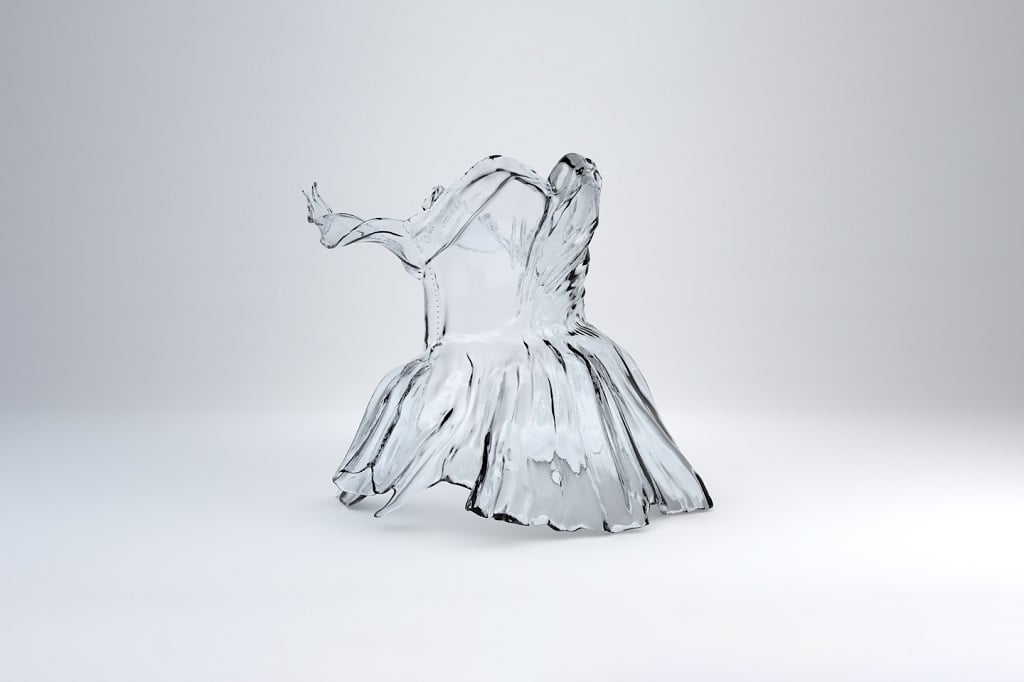
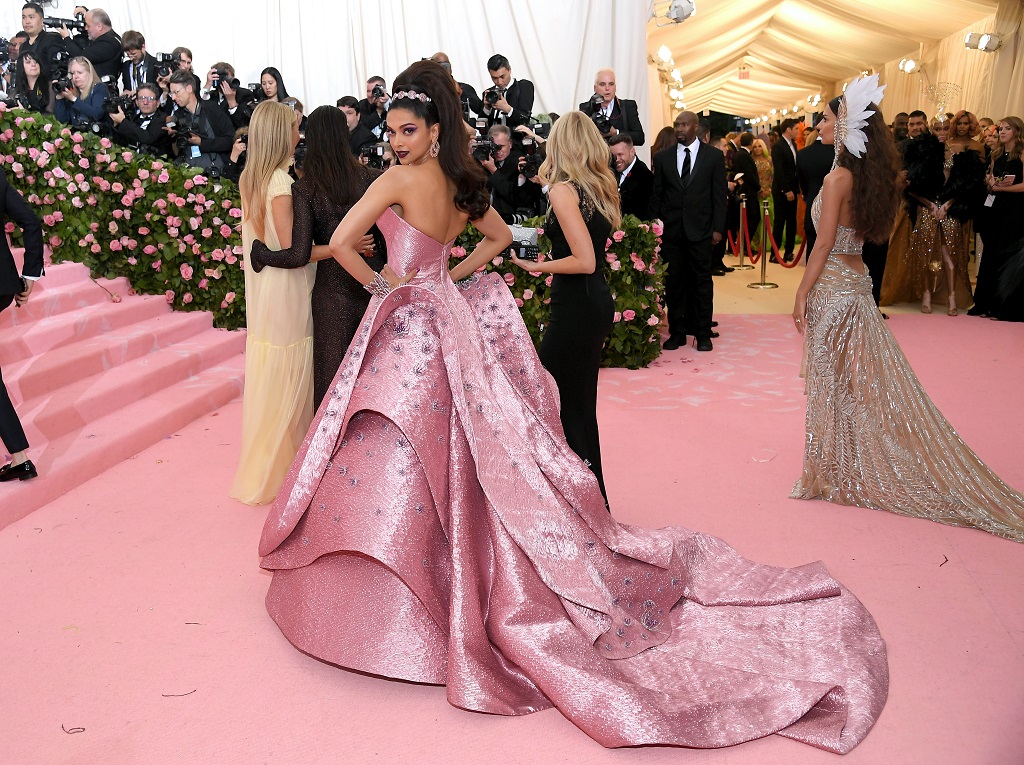
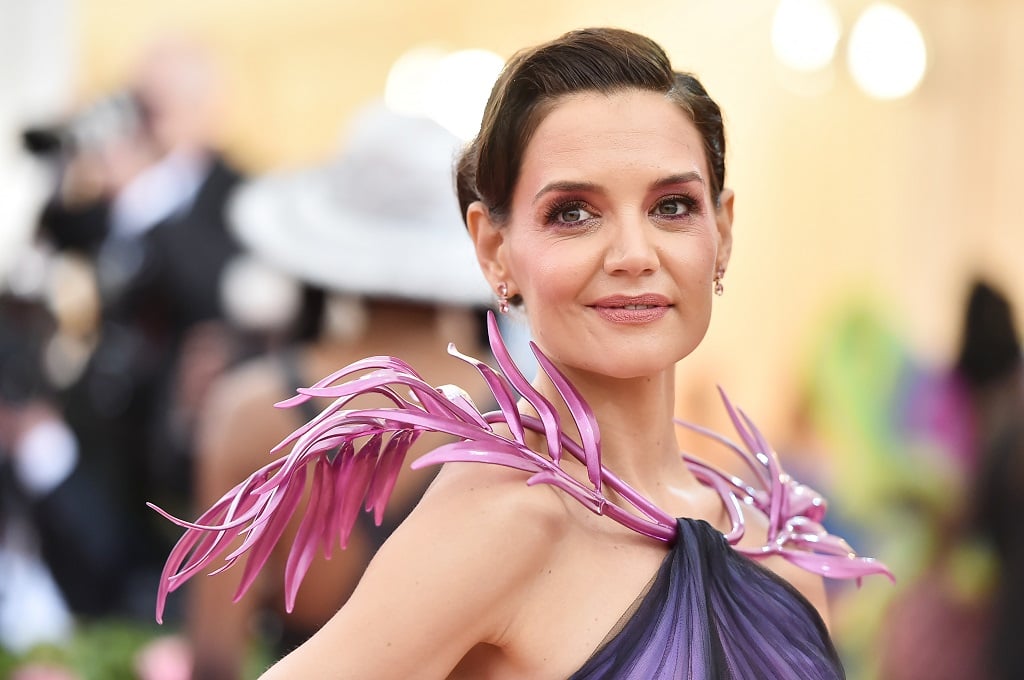
[Images: Getty Images]
While those gowns and headpiece were the show-stoppers, they were not Posen and team’s only foray into fashionable 3D printing.
Posen himself sported palm leaf lapel brooches 3D printed with both SLA and MJF technologies. Actor Andrew Garfield and art dealer and gallery owner Vito Schnabel both accessorized with SLA-3D printed cufflinks that mimic the design and structure of the above rose gown.
I would be honestly surprised if these Posen / GE Additive / Protolabs creations were the only examples of 3D printing to have appeared on last night’s red carpet, but feel pretty confident this collaboration marked this year’s largest use of the technology.
I’m also very much interested in finding out more about this very multidisciplinary collaboration — and so I was happy to accept Protolabs’ invitation to moderate an upcoming panel.
At the fast-approaching RAPID + TCT event in Detroit, Protolabs and GE Additive will present more detail in a panel discussion titled “Boldly Going Where 3D Printing Hasn’t Gone Before.” I’ll be moderating the conversation between Eric Utley, Applications Engineer, Protolabs and Sarah Watson, Design Engineer in GE AddWorks, GE Additive.
Join us at the Smart Manufacturing Hub presentation on Wednesday, May 22, 11:20 AM – 12:00 PM.
Via Protolabs (pdf)