![[Image: Stratasys]](https://fabbaloo.com/wp-content/uploads/2020/05/3Dprintedaircraftplane_img_5eb09627ba409.jpg)
Marshall Aerospace and Defense has revealed its use of 3D printing for prototype and final flight parts.
3D printing parts for aircraft is becoming more commonplace as aviation continues to take interest in the technology — and, importantly, as quality and repeatability improve to the point of qualification.
There is little “in between” ground in aircraft parts, not a lot of parts where “good enough” is good enough. If there’s an industry (other than medical) where we want certification to take the fore, it’s flight. Having final flight parts from a 3D printer can be a solution to a good many applications, as the technology can create lighter-weight parts made to spec.
So Marshall Aerospace and Defense (ADG) has turned to some familiar equipment to for its military, civil, and business aircraft, as well as ground-running equipment.
Marshall ADG and 3D Printing
![Final part: 3D printed aircraft ducting [Image: Stratasys]](https://fabbaloo.com/wp-content/uploads/2020/05/3Dprintedaircraftducting1_img_5eb0962819a9e.jpg)
“When manufacturing on complex engineering programs, we need a method that can create an accurate, complex, functional and lightweight duct efficiently with minimal tooling costs – this is where 3D printing fits perfectly. But we also need to ensure that the ducting work produced will be approved by the EASA for flight,” explains Chris Botting, Materials, Processes and Additive Manufacturing Engineer at Marshall ADG. “As a result, we’re using the Stratasys Fortus 450mc FDM Printer and ULTEM 9085 resin – a tough, yet lightweight 3D printing material with high thermal and chemical resistance. This has been crucial to overcoming the stringent requirements of our industry, as we can now 3D print parts with the desired flame, smoke and toxicity properties for use on aircraft interiors.”
The company is quite familiar with the technology, and is ramping up from existing use that has included “several pieces of 3D printed ductwork flying on heavily modified aircraft, as well as holders for safety knives and switches for aircraft interiors.”
The Fortus 450mc has seen success in other transportation industries, such as for on-demand replacement parts and tooling for the rail industry and for tooling, jigs and fixtures, and end-use parts for race cars.
Aircraft 3D Printing For Prototyping, Tooling, & Final Parts
Focusing on applications in aircraft, Marshall ADG has created a variety of final parts, such as flight-approved, 3D printed ducting for air conditioners created in ULTEM 9085 resin (seen above), as well as a final ECS duct adapter made in Stratasys Nylon 12 (seen below left). Tooling of course remains important as well, such as with the forming tool seen below (right), also made from Nylon 12.
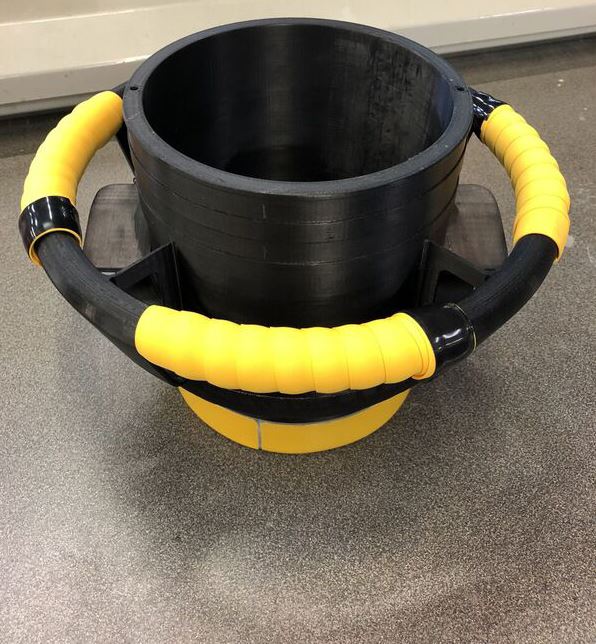
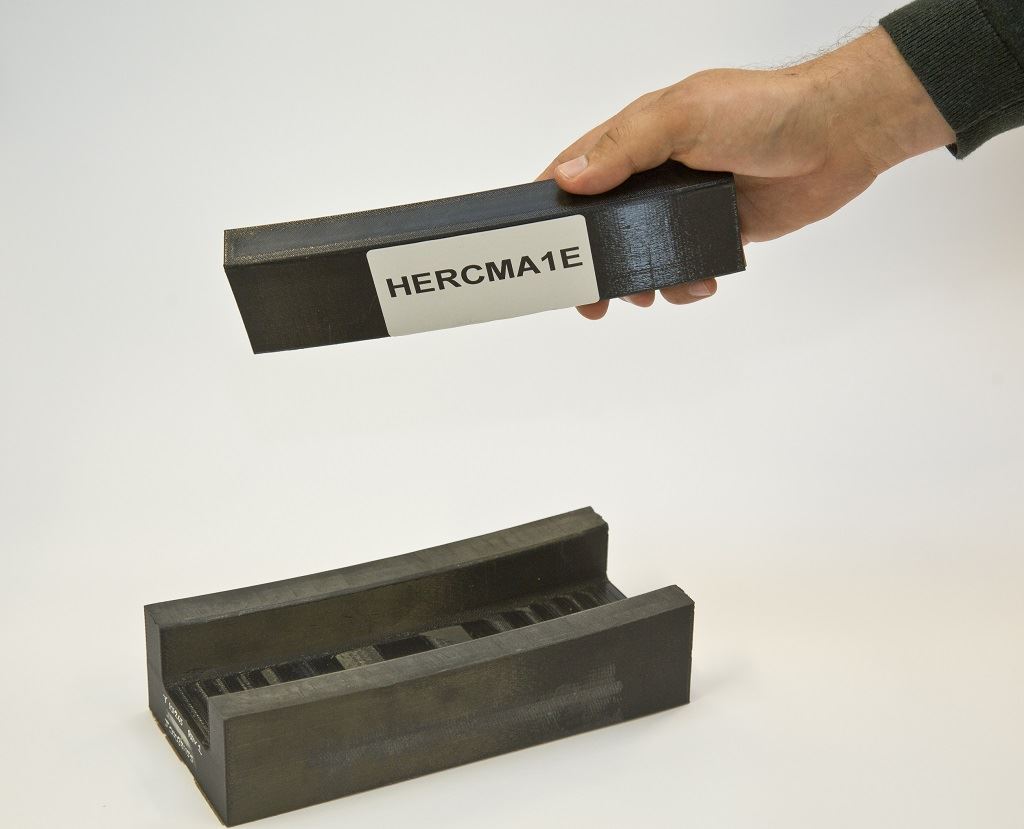
The ducting adapter was an interesting case for moving from prototype to production with 3D printing.
The piece, intended for ground-running equipment, is designed to cool aircraft on the ground. A functional prototype 3D printed in ASA ensured that all was well with the complex design — and then the team went further.
“We were then able to demonstrate it had the potential to be 3D printed in Nylon 12 material as opposed to the more conventional method of machining from aluminum. The 3D printed duct led to a significant cost reduction compared to machining the part out of aluminum, as well as a 63% reduction in overall weight,” said Botting.
Both the ASA prototype and Nylon 12 final piece were made on the Fortus 450mc.
While unfortunately I had to miss out on the opportunity this week to head to the UK to see all in person, these uses of 3D printing in aerospace-grade speak for themselves. And when they don’t, the Marshall ADG team are happy to speak for them as well:
“FDM technology has altered the way we work, and the aerospace-grade 3D printers and materials enable us to meet our increasingly aggressive deadlines and complex manufacturing requirements,” Botting said. “In the future, there is no doubt that 3D printing will continue to have a significant impact in the way we design and manufacture in our business.”
Via Stratasys
Eric Haddad is the founder and Pilot in Command of 3DAeroventures, a Texas-based outfit specializing in 3D printed RC aircraft.