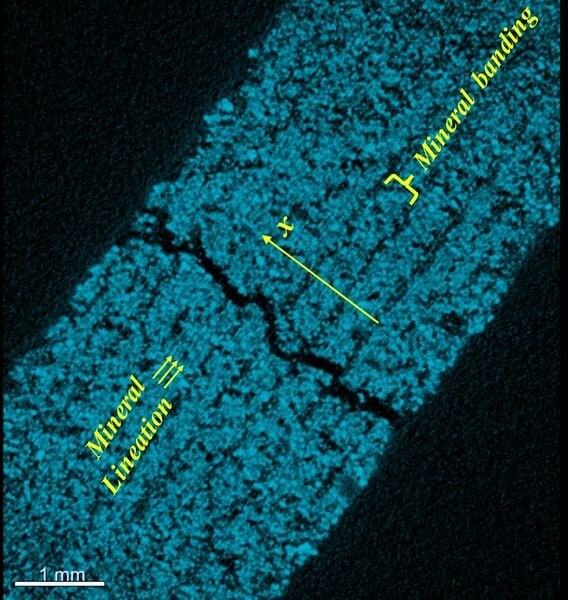
Researchers are using 3D printing to better understand the underground flow of fluids.
Letās talk a bit about underground fluids. These are often water, but can also be oil, waste chemical leakages, and more. But how do they exist and move around when the ground is solid rock?
No, there arenāt hidden fluid tanks underground storing water or oil. Instead, it turns out that fluids are soaked into tiny crevices and cracks within rocks. The underground is a massive volume ā remember itās a 3D environment, not the small 2D environment we humans inhabit on the flat surface of the world. These cracks exist everywhere due to the eternal motion of continental plates and local geological activity.
With the global need for water and oil, as well as the critical requirement to understand chemical deposits, it is important to understand how fluids actually flow underground. If an intervention takes place, for example an excavation, what changes in fluid flow could happen? Thatās a very hard problem to understand.
Imagine youāre a fluid molecule underground. How do you flow? Itās clear that flow is governed by the geometry of these spaces. For example, a rough surface would impede the flow, whereas a ācorrugatedā surface thatās aligned to the flow could encourage fluid motion.
In addition, the ability to understand āfracture geometryā could be important to further understand seismic activity.
How can this be done? While there have been many virtual simulations of the environments, researchers at Purdue and Sandia National Labs felt it useful to simulate these geometries using 3D printing. It was possible to 3D print samples in gypsum in a method they describe as āgeo-architectingā.
They explain:
āHere, we use additively manufactured gypsum rock to show that mineral fabric orientation governs the isotropy or anisotropy in fracture surface roughness in layered rock which in turn governs the volumetric flow rate through fractures. Through additive manufacturing, the orientation of the mineral fabric and layering can be controlled and used to determine the contributions to fracture surface roughness.
The results demonstrate that layer orientation alone is insufficient to predict fracture surface roughness. Knowledge of in-layer mineral fabric orientation is also required. When the resistance to fracturing from layering and mineral fabric orientation acts in the same direction, corrugated surfaces are formed that create highly conductive flow paths parallel to the ridges and valleys of the corrugations. This finding enables the design of fracturing strategies to maximize production potential and provides a method for predicting flow anisotropy in existing fractures through careful examination of in-layer mineral fabric.ā
Their samples were produced using a 3D Systems ProJet CJP 360 3D printer using a bassanite powders that formed into gypsum structures when printed. These were examined microscopically to verify the necessary structures were produced.
Using these prints the researchers were able to better understand the development of corrugated cavities when two surfaces interact. It seems that this could be a useful method going forward to more deeply understand the underground realms:
āThe recent advancements in the creation of āgeo-architectedā rock through additive manufacturing provide a method for creating highly reproducible samples with specific aspects of geologic material to enable identification of physical properties that contribute to the complexity of fracture formation in natural media.ā
Via Nature