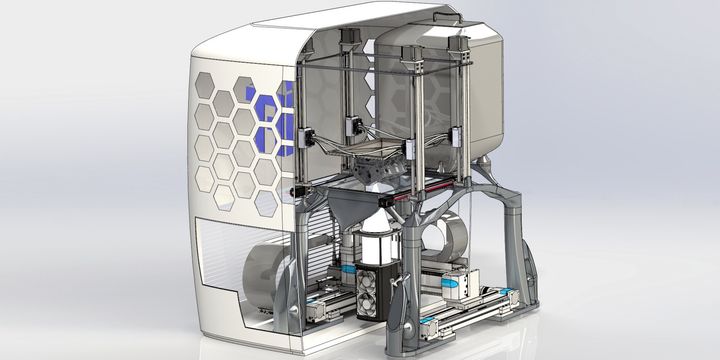
We were tipped to some very intriguing research being undertaken at TU Graz to develop a new metal 3D printing process called “SLEDM”.
SLEDM is somewhat similar to SLM, or “Selective Laser Melting” that is performed by a number of powder bed fusion 3D printer manufacturers. However, the “L” means laser — but there are no lasers in an SLEDM system.
Instead of lasers, SLEDM actually uses powerful LED light engines, hence the name “S LED M”, or “Selective LED Melting”. But LEDs are not all the innovation in this highly unusual process.
Selective LED Melting
But first I’m very curious about the LED light engines in this prototype device. The LEDs I’m familiar with won’t even warm up your fingers if you turn them up full, so it seems the SLEDM process uses something a little different. They explain:
“The SLEDM process uses a high-power LED beam to melt the metal powder. The light-emitting diodes used for this purpose were specially adapted by the west Styrian lighting specialist Preworks.”
I took a look at Preworks, and it seems they are a lighting manufacturer, whose products typically are used to illuminate large spaces, such as arenas and theaters. One of their products uses 1000W to produce an eye-searing 37,000 lumen beam! For reference, a standard household bulb will produce 900 lumens, so this single device would produce the equivalent of 41 bulbs, all at once. They also seem to be able to produce lighting equipment using various colors / frequencies, and thus are likely able to make a light engine suitable for SLEDM.
The secret here is in the focusing. Imagine taking the light required to illuminate an entire theater and focusing it down to a mere 1mm diameter spot. That’s how they gain sufficient energy to melt metal powder.
And about that focusing, they further say:
“[It’s] equipped with a complex lens system by which the diameter of the LED focus can be easily changed between 0.05 and 20 millimetres during the melting process. This enables the melting of larger volumes per unit of time without having to dispense with filigree internal structures, thus reducing the production time of components for fuel cell or medical technology, for example, by a factor of 20 on average.”
This is an interesting concept, although the wider the beam, the less energy density is produced per unit area. Thus the system must move a bit slower when melting a larger area, as the larger dot size is as much as 160,000X larger in area than the smaller spot. However, it appears the overall result is a 20X faster print speed.
It’s also possible the LED light engine might be less expensive than equivalent laser engines, thus providing a path to developing a less expensive 3D printer.
Another factor in the cost could be how the very specific LED frequency emitted matches the absorption of the target metal. LEDs tend to issue light in a very limited frequency range, so it’s possible to completely miss the required frequency or hit it right on the nose. If the latter, then far less energy would be required for the LED to do its job, as opposed to a more broad-spectrum laser. This could also mean an SLEDM machine might be usable only with a specific metal.
Upside Down Metal 3D Printing
The other highly unusual aspect of SLEDM is that it involves 3D printing metal powder upside down.
This is quite different from the standard approach of bottom up, in which the build chamber is gradually filled with layers of metal powder, eventually completing with the part buried in powder.
In such powder bed fusion systems, the laser (or energy beam) emits from above and impacts the top surface of the growing powder bed. Prints are first printed on a fixed metal plate that forms the build surface. After printing, the object is sliced off the build plate and post-processed.
This is apparently different in the SLEDM process. They explain how this works:
“This technology is combined with a newly designed production plant which ā in contrast to other metal melting plants ā adds the component from top to bottom. The component is thus exposed, the required amount of powder is reduced to a minimum and the necessary post-processing can be carried out during the printing process.”
Honestly, that doesn’t explain to me how this works. However, by looking closely at the SLEDM system concept diagram at top we can guess what’s really happening. Here’s what I think:
- A transparent plate is the build surface
- A fine layer of powder is deposited on the plate
- A build platform is lowered to the top of the fine layer of powder
- The LED engine is underneath and selectively illuminates areas on through the transparent plate
- The first layer bonds to the traveling build platform
- The build platform moves up, out of the way
- Unused powder is swept away, perhaps for recycling or immediate re-use
- A fresh layer of powder is deposited
- The process repeats until the object is completely built
If that’s how SLEDM works, it is reminiscent of SLA systems, in which the laser is underneath the resin tank, firing upwards.
SLEDM Support Structures
The researchers say that this approach provides a means to achieve smooth surface quality. They also say support structures are “no longer necessary.”
While I could see the smooth surface quality being possible as the extremely tight focus of the light energy could result in smoother edges, I cannot understand how support structures would be eliminated. For the platform to move up and down (which it clearly must do, based on the diagram), it must pull the partial print with it. And that, based on almost every geometry, will require support structures to attach to the build platform. This is exactly the same scenario as one would see in an SLA system, which must use supports.
The group designing SLEDM has applied for a patent, which strongly suggests they or someone they license it to will develop SLEDM into commercial products. We don’t know who, and we don’t know when, but SLEDM will surely emerge in product form at some point.
Via TU Graz (German) (Hat tip to Benjamin)