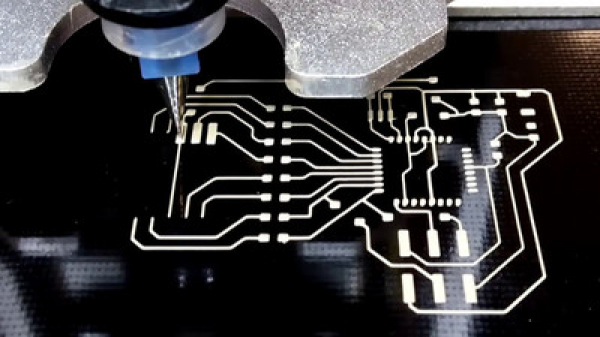
[Source: DrivenxDesign]
Charles R. Goulding and Adam Friedman review a recent webinar discussing the 3D printing of electronics.
On April 28, 2020, a consortium of 3D printing entities – nScrypt, U.S. Army Research Center, and DeLux Engineering to name a few – convened for a discussion panel webinar showcasing the science behind 3D printing electronics and highlighting both ongoing and future research efforts. The panel was moderated by John Hornick of Sciperio, and Larry Holmes and Brandon Dickerson of nScrypt.
James L. Zunino, U.S. Army ARDEC
Mr. Zunino provided great insights into 3D printing electronics being developed by the U.S. Army Armament Research, Development, and Engineering Center (ARDEC). Most of his and his team’s work is at the Printed Electronics, Energetics, Materials & Sensors (PEEMS) Center for Innovation.
His discussion focused primarily on “energy harvesting” and how 3D printing could contribute to primary (one-time use) and secondary (rechargeable) batteries that would power dynamic grips and sensors of various armaments and munitions used by a United States soldier. One example he used was 3D printing for the power sourcing of modernized M67 grenades and increasing reliability by increasing the form factor of the M67 through 3D printing.
Other important topics that he discussed were increasing bandwidth and wavelength in Radio Frequency Identification (RFID) to be ultimately integrated with explosives and energetics.
Dr. Ken Church, CEO, nScrypt
Ken Church, the CEO of nScrypt with a Ph.D. in Electrical Engineering from Oklahoma State University, spoke on the evolution of electronic devices within the context of 3D printing. He emphasized that the functions of today’s electronic devices are impressive, having greater capabilities and increased potential to be discovered.
In his discussion, he commented on the proof of concept for all-powerful and reproducible electronic prints, using his model Printer Circuit Cylinder (PCC) as an example. This apparatus contains multitudes of diodes and circuits that can electronically motor machines, smart devices, and even other printers that could continue the process of reproducing high technology.
Many of today’s 3D printed electronics are 2.5 or 2.75 dimensions, and companies are working toward the complete 3D modality using future 3D printer technology.
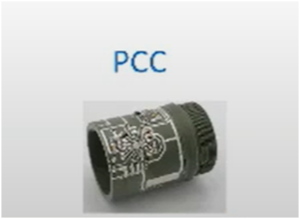
Dr. Amanda Schrand, U.S. Air Force
Amanda Schrand, a Ph.D. in Chemical and Materials Engineering from the University of Dayton, is a military employee who has done extensive research on raw materials that are used in 3D printing. Her latest research paper, A Fundamental Study of Printed Ink Resiliency for Harsh Mechanical and Thermal Environmental Applications, highlights this effort.
Amanda is part of the highly esteemed Flexible Electronics and General Ordinance Manufacturing (FLEGOMAN) team at the Air Force Research Lab, which analyzes how additive manufacturing/3D printing can be used to increase munitions and weapons strength. Much of her research focuses on making high scale proof of concepts, prototyping models with the use of Autodesk and SOLIDWORKS software.
Dr. Schrand provided valuable insight on stress testing and analyzing environmental conditions to structure 3D printed material. She also spoke about one of her ongoing projects, a Bayesian logic integrated robotic arm, co-created by the Army and researchers at Georgia Tech University.
Dr. Erik S. Handy, Principal Scientist, SI2 Technology
Erik S. Handy is a Massachusetts Institute of Technology (MIT) Ph.D. in Organic Chemistry and Polymer Science. Dr. Handy works outside of metropolitan Boston and has done research with the burgeoning engineering and computer science departments at the University of Massachusetts-Lowell. His work has centered on making 3D printed notch arrays that can become prototypes for anechoic chambers which are highly absorbent rooms of sound and light.
He discussed different wet paste adhesives that can be used in 3D printing and how these materials could be used in Radio Frequency design and could further strengthen 3D printed materials long after they are produced. His most interesting insight was when he orated about “dissimilar materials [that] can be compiled on some build plate without moving the part.” His statement, in addition to the body of his research, shows that with ingenuity and science, 3D printing can become even more compact with even greater productivity and strength.
Curtis Hill, Senior Materials Expert, NASA MSFC/ESSCA
Curtis Hill works directly with NASA Laboratories located in Huntsville, Alabama. The research of Mr. Hill dealt mainly with space exploration, however, if there are successful implementations of his technology, there could be significant implications for his technology outside of space activity.
Hill’s Space Manufacturing Project deals with using nano-ink and printing, and using flexors for space sensors. The bulk of his research focuses on developing 3D printed humidity sensors that concurrently measure bio senses (water vapor, heat, sweat excretion) that can be attached with Radio Frequency Identification (RFID) technology. His research also deals with circuit boards and substrates that can be used for important energy harvesting, especially in outer space where electricity is governed by different rules than that of Earth. The highlight from his presentation was a 3D printed cortisol detection device biosensor that, through his teams’ multitude of researchers, could reliably be used for moderating stress levels of astronauts in outer space.
Dr. Mark Mirotznik, University of Delaware
Mark Mirotznik is a biomedical engineer with a Ph.D. from the University of Pennsylvania. He currently chairs the Department of Electrical & Computer Engineering of the University of Delaware and provides consultations with various companies on additive manufacturing/3D printing. Dr. Mirotznik gave his perspective on additive manufacturing and the cost-benefit analysis of producing different structures in 3D printing. He, too, stressed the need for most electronic 3D printing to change from 2.5 dimensions to 3 dimensions.
He mentions the works of Dr. Raymond Rumpf of the University of Texas El-Paso (UTEP) and his research focuses heavily on lattices, notches, resins, and the scientific components that make 3D printing highly technical as well as increasingly effective. Some projects that he cited included pellet printing with a programming script, printing aluminum and zirconium crystals (lattices/super structured arrangements), as well as his work on passive beam steering lenses, namely 3D Luneburg and Maxwell Fish-Eye lenses.
Dr. Paul Parsons, CEO/Chief Science Officer, DeLUX Engineering LLC
Paul Parsons, a Materials Science Engineer with a Ph.D. from the University of Delaware, is an up and coming developer of 3D printing structures. His research has been vast, and like many on the panel for this webinar, he tests 3D prints at extreme temperatures and environments.
During the webinar, he discussed Radio Frequency applications and how they can withstand higher levels of temperature, pressure, and volume. He also touched upon the use of high art in 3D printing, which requires special logistics for making unique designs and structures.
The work of his business, DeLUX Engineering LLC, abides by “subtractive manufacturing”. DeLUX Engineering LLC products are created with 3D printing superstructures and then taking apart these structures to get highly distinctive shapes for medicines, radar, and defense devices.
Conclusion
The webinar was highly technical and provided a great illustration of the scientific state of 3D printing/additive manufacturing, thanks to the expertise of the various speakers.