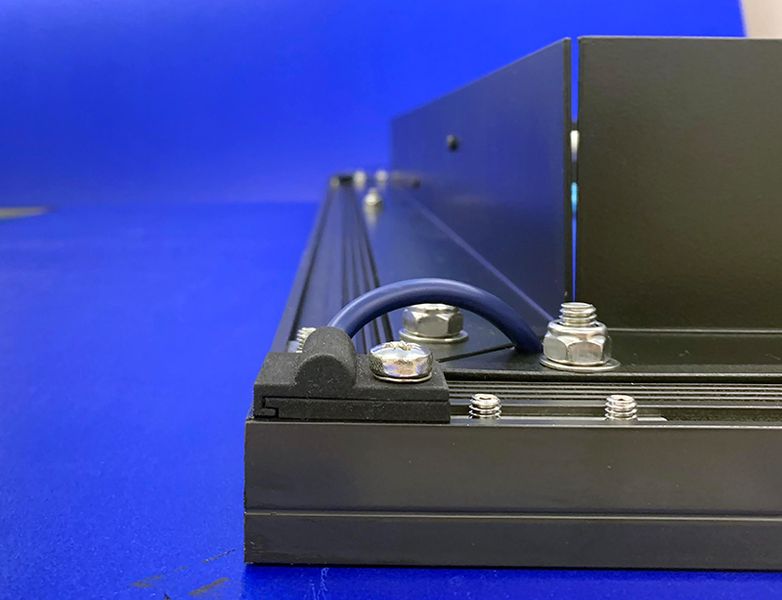
providing protection from the edges of the aluminium housing. [Image: voxeljet]
Many companies requiring thousands of components use 3D printing to perfect their design before moving to injection molding for production, but sometimes it makes sense to stick with additive manufacturing.
When we talk about production 3D printing, a few types of product immediately come to mind — some of the highest-profile parts fit neatly into the low-volume, high-value category, such as for aerospace applications. Complex, lightweight, reduced-part count components for aerospace, often 3D printed in high-value metals like Inconel, certainly perform well as headline case studies for production additive manufacturing. These leverage the benefits of this technology beautifully, as wholly new geometries are possible in single-piece builds.
But not every production use case is nearly so glamorous. Some, indeed, may be much more humble and still make a great deal of sense in a way that is also more widely applicable than rocket parts. And that’s what takes us into serial production, looking at higher volumes.
Serial Production 3D Printing
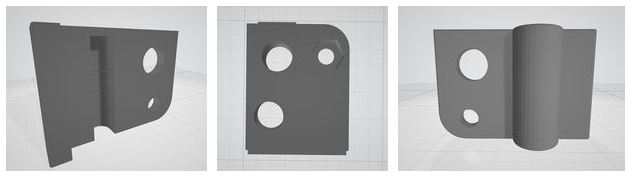
Spanlite, a British company offering LED solutions, recently turned to 3D printing.
The company hadn’t really been making use of the technology, but found itself requiring a new solution for cable management for its LED panels. With the help of voxeljet UK’s service offerings, the Spanlite team were able to prototype a new two-piece interlocking cable clamp.
Once they had the design down, the Spanlite team examined its options. They require about 8,000 of these cable clamps annually. It turns out that 500 of these pieces can fit into the build volume of voxeljet’s High Speed Sintering (HSS) system — just 16 3D printing runs can supply the full year’s requirement, easily possible through voxeljet’s service center, and ensuring that no tooling needs to be made, while design and supply adjustments can be made at any time.
“Due to their small size and despite the relatively low level of complexity of the components, the clamps can be manufactured more cost-effectively using the HSS process than with alternative 3D printing technologies or conventional manufacturing methods,” voxeljet explains.
It seems that the Spanlite team, though new to working with 3D printing, are now converts looking ahead to future potential use, as the company’s Managing Director, Adrian Bowker, notes:
“After a short test phase to perfect the design and function, we were quickly able to move on to full production and assembly. And we are sure the clamps were just the beginning. We are already identifying new components suitable for 3D printing. The technology offers us various advantages both in the design and in the production of the components we need. We are excited to see where the journey will take us.”
And:
“The beauty of 3D printing from voxeljet for us was that not only could an initial requirement, the cable strain relief, be met, but that we could also integrate additional shapes and functions into the component without incurring additional costs.”
These clamps were developed to meet certain criteria, as Bowker alludes, but that doesn’t mean that’s the end for the design possibility for this one piece. Ensuring that the right angles could be achieved, high mechanical loads could be met, and other such functional needs accomplished, the design could be relatively quickly iterated. And it still could be; adjustments can be made at any time, adding or tweaking functionality without the need to change out tooling (because, of course, there isn’t any).
voxeljet Mass Production
This case study fits neatly into an area that voxeljet has been focusing on for some time: mass production.
They’ve been working for a few years toward a “fully automated 3D production solution capable of replacing conventional manufacturing in serial-production.” While much of this has focused on casting, there’s also clearly the development of HSS, which allows for 3D printing end-use polymer parts. The cable clamps for Spanlite, for example, are 3D printed in polyamide 12 and ready for use.
Sometimes, we can see, 3D printing makes sense in serial production. There are of course still some limitations, as a quantity of 8,000 relatively small pieces in a year pales in comparison to millions of injection molded parts able to be made in the same span — but it comes down not only to what those parts are, but who they’re for, and whether there’s wiggle room in adjustments made for their design, supply quantity, and/or supply timing. For Spanlite, it’s making sense to bring 3D printing into play through an outside service offering, gaining immediate access to not only technology but expertise. And I don’t think this will be the only such use case we’ll be seeing along these lines in the near future.
Via voxeljet