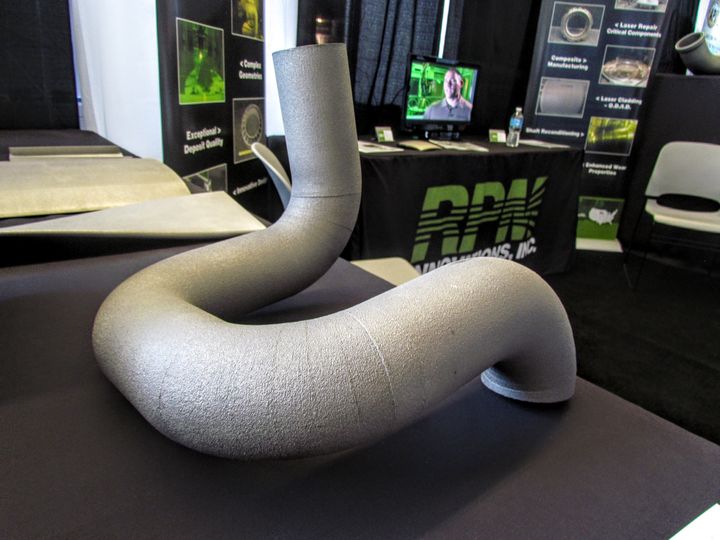
With the recent spotlight on 3D printing as a result of the pandemic’s bump on supply chains, I listed some ways the technology can help manufacturers.
Traditionally 3D printing has been used as a prototyping method by many companies. That fate was cemented in by the original poor-quality material constraints of early 3D printing equipment. However, that’s changing in recent years with the introduction of far more capable machines that can 3D print robust objects in proper engineering materials.
But how can this capability be leveraged by manufacturers?
Jigs & Fixtures
Manufacturing usually requires a considerable amount of jigs & fixtures to aid the process of assembly. For example, a jig could be used to position a plate perfectly before mounting, and would not only speed assembly, but also ensure accuracy.
A 3D printing setup near the production line can allow workers to quickly develop and deploy more effective jigs & fixtures based on their intimate knowledge of the production process. This could make for more efficient production in the long term.
Low-Volume Production
Some manufacturers using conventional approaches will turn away work if it isn’t profitable due to low requested unit counts. However, it is often possible to successfully meet customer demands through the use of 3D printing technology because there is little requirement for production set up: 3D printers can print arbitrary objects if supplied with appropriate GCODE. With a 3D printing capability, a manufacturer might be able to broaden their client base.
Creativity
Making 3D printers available in the workplace, perhaps through an internal makerspace, could encourage staff to become more creative as they could explore and share ideas. If more than a critical amount of people participant, this concept could ignite a wave of creativity over the organization.
Emergency Replacement
Sometimes a production line will shut down due to the detection of an improperly designed or manufactured part: you cannot make products using the wrong part. The shutdown would typically last until new supplies of the bad component could be sourced, sometimes taking days or weeks while a supplier tools up for the new part.
That can be avoided entirely by equipping the manufacturing line with an emergency 3D printing capability. This system could quickly produce the new part without waiting for suppliers, and get the production line back up almost immediately. Of course, the unit cost of the new component would be a bit higher than normal, but that’s a lot better than shutting everything down for an extended period.
When the new part finally arrives from the supplier, the emergency-use 3D printed part can be retired.
Digitization
The pandemic showed everyone the fragility of many contemporary supply chains, and many companies were scrambling to find parts and suppliers. If one were to make use of 3D printing for at least some of the parts in an assembly, these could be rapidly sourced from any of a number of public 3D print services by simply sending the digital files over for production.
This transfer can only occur if the parts were digitized, and thus digitization goes hand-in-hand with use of 3D printing.
Uniqueness
If a manufacturer were to include 3D printing capabilities in their portfolio, it’s possible they could attract more business simply because some buyers seek parts only producible on 3D printers due to unique geometries. Without a 3D printing capability those prospects must seek other providers.
Flexibility
In today’s world there is a constant wave of change washing over certain types of products. In order to keep up, manufacturers must then frequently change their production line to match the new requirements. This can be quite challenging with traditional manufacturing processes.
It’s much easier with 3D printed parts because the making machinery doesn’t really change; only the digital files driving them change. Therefore it can be quite rapid to switch a 3D print factory to produce different components, sometimes radically different components.
Trial Production
Tooling up a production line is a big sunk cost, and that could be wasted if the product turns out to be a dud. Therefore it can be risky trialing new products.
However, if the initial runs of a product were produced through 3D printing, there would be no need to tool up to a large degree. The product could be tested with actual customers and a determination could be made whether to proceed or how to adapt the product for better acceptance. Once the product’s design is settled, then an investment in tooling up can proceed.
And there’s eight ways 3D printing can help manufacturers.