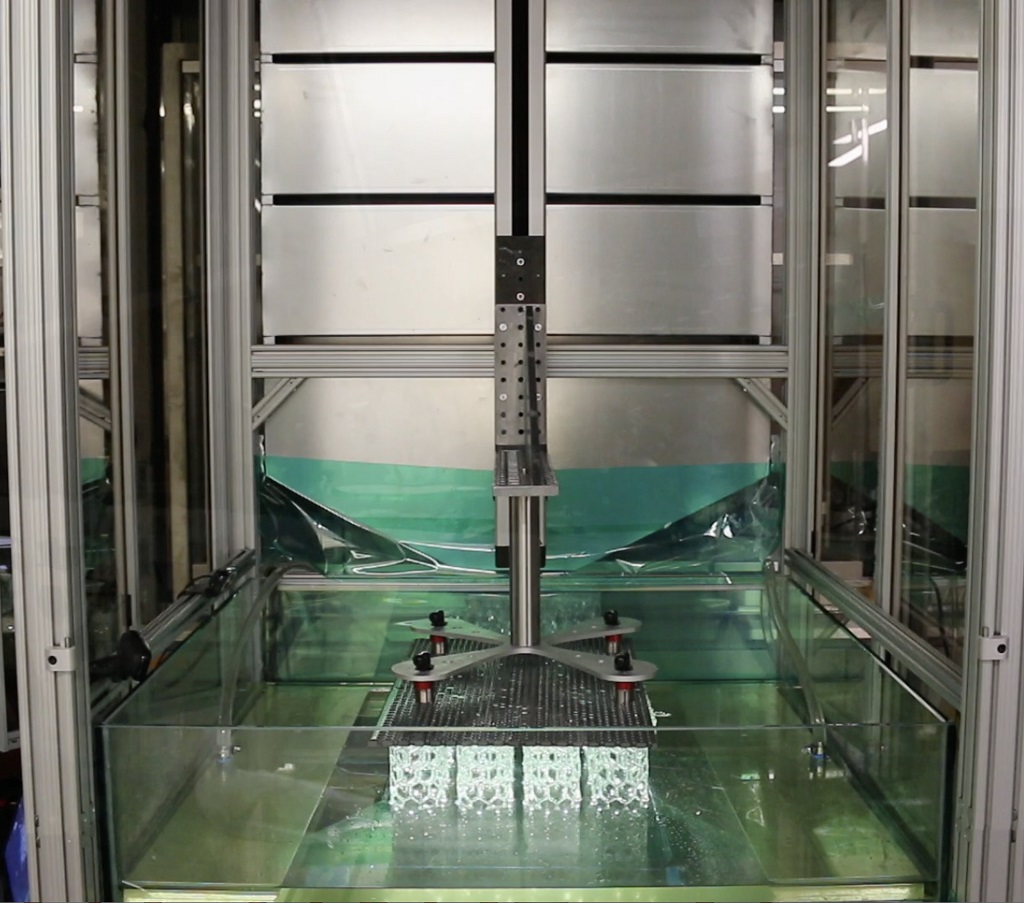
High-throughput 3D printing company Azul 3D recently announced a notable seed funding round.
The company, born out of research from Northwestern University, is focused on high-throughput 3D printing. Their technology, HARP — High Area Rapid Printing — takes DLP 3D printing to another level.
Senior Chemist Rachel Davis describes the Azul 3D process in her Women in 3D Printing interview:
“The technology we work with is called High Area Rapid Printing, or HARP, where a mobile liquid interface is at the bottom of the print vat instead of a traditional nonstick surface that requires a time-intensive peel process. The interface can be cooled, which helps with managing the heat generated during a fast print process – especially over large areas.”
The young company has seen interest picking up lately. It was, for example, recently included among industry expert and Fabbaloo friend Tuan Tranpham’s 3D printing trends. Azul 3D took its place in these perceptions in the trend of “Resin Polymer Is Moving Faster Into Manufacturing” alongside Inkbit and Nexa3D.
Azul 3D not only sounds interesting — it apparently sounds profitable, as last week the Illinois-based company joined a growing number of 3D printing companies pulling in millions of dollars of investment.
The company announced a $12.5 million funding round, which it describes as “an oversubscribed seed financing” and brought on some big names as new backers. They list:
- Louis A. Simpson, former CIO for Geico, former manager of Berkshire Hathaway and founder of SQ Advisors
- Wally Loewenbaum, former chairperson of 3D Systems
- Joe Allison, former CEO of Stratasys Direct Manufacturing
- Hugh Evans, former senior vice president of corporate development for 3D Systems
So what’s to come of this investment?
“The company intends to secure major partnerships validating this point in the very near future,” said Chad Mirkin, Co-Founder and Chair of Azul 3D.
It’s not only the technology that’s interesting for this fundraising, but the timing. We are, as we all well know, still in the midst of a global pandemic. Business conditions are, shall we say, not quite as normal. To raise millions during this time is a major sign to industry that a company is not only performing well, but performing well in a disrupted world. 3D printing has seen some major investments and business moves in the last half-year, despite so-called COVID conditions.
These funding rounds make sense from a few angles. Not only has 3D printing been on the rise as an industrial technology for years now, but these last several months have shown the technology to be viable in many real-world applications, including pandemic response.
Azul 3D was among the many, many companies in this industry to step up to help 3D print personal protective equipment (PPE) and other pandemic-response products. PPE from Azul 3D has found its way to hospitals, prisons, first responders, and members of the Navajo Nation in need of more personal safety from viral spread. Face shields, which have proven a 3D printing mainstay of PPE, are being produced at scale — with HARP technology, Azul 3D reports that they are “producing medical face shields at a record rate of 1,000 components per printer in a 12-hour shift.”
David Walker, Azul 3D Co-Founder and CTO, shares some company perspective on where they fit in 2020 and why this investment is making sense just now:
“One of the reasons we’re doing so well is because our technology offers a solution to unexpected surges in demand and supply-chain bottlenecks that occur during global crises, such as in the current pandemic. With the ability to manufacture nearly anything quickly and on demand, we can meet these unexpected needs as they arise to quickly fill gaps in the supply chain. That’s the big difference between HARP and traditional manufacturing as well as many other forms of 3D printing, which either don’t have the throughput or material properties to meet the required specifications. We don’t have to change a whole assembly line or machine new molds. The concerns that accompany a stressed supply chain simply vanish.”
Via Azul 3D