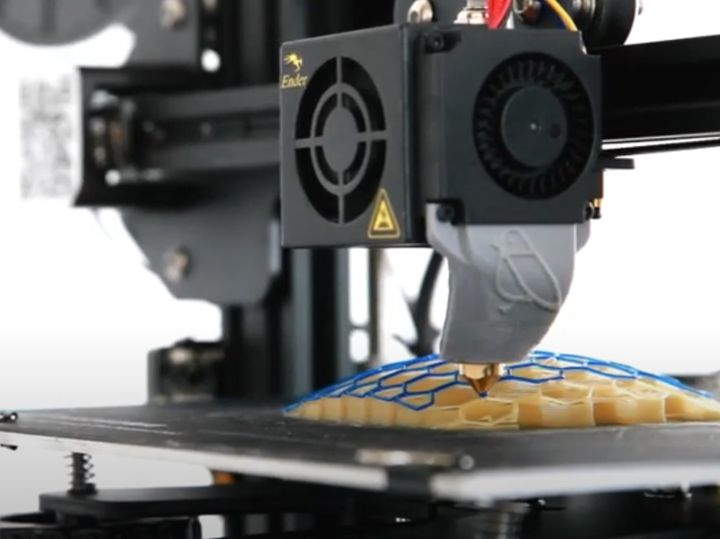
Non-planar 3D printing is perhaps a term you’re not familiar with but, if Gabriel Boutin has his way, you will in the future.
Quebec-based Boutin has twelve years of experience as an industrial designer who has recently been specializing in the design of complex cycling helmets. That is a challenging business to be in, given the incredible level of competition. Today’s helmets compete not only on features and safety, but also strongly on styling and visual appearance.
3D Printed Cycling Helmets
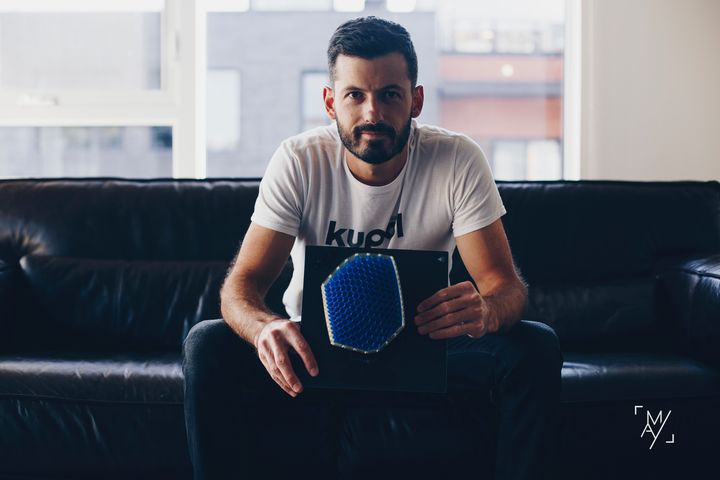
Melissa Tremblay (MAY – Photographie)]
During the course of this work, Boutin frequently used different 3D printers to produce helmet prototypes. But, like many 3D printer operators, found limitations and barriers all along the way.
Boutin experimented with using today’s advanced 3D printing equipment, including gear from Carbon, HP, Origin and others, but found “each had a downside, and was expensive to use.” Commitment for a Carbon 3D printer, for example, requires something close to US$50,000 per year using their subscription model.
These prices were too dear for Boutin’s modest budget, so he looked elsewhere for solutions that enabled the creation of prototypes that were suitable.
By “suitable”, Boutin means the prototype actually “feels like an end user object”.
Powder 3D printers can produce objects with smooth surfaces, but they have a significant limitation: geometries must allow for removal of loose powder. This prevents the printing of sealed interior cavities, for example.
He then considered the use of inexpensive FFF 3D printers, but their uniform layer-by-layer approach didn’t meet his “feels like” objective.
Even worse, the extrusions on FFF 3D printers “don’t respect the flow of the object”, and result in less than optimal mechanical properties.
Boutin discovered 5-axis 3D printing, and after examining the two commercial options (Hage and VSHAPER), they seemed to enable the types of extrusion he sought. However, they were similarly expensive to acquire and operate, so they were not an option.
Boutin realized there might be a way to persuade inexpensive FFF 3D printers to perform in the way he wanted after seeing experimental videos of non-planar 3D printing.
Non-Planar 3D Printing
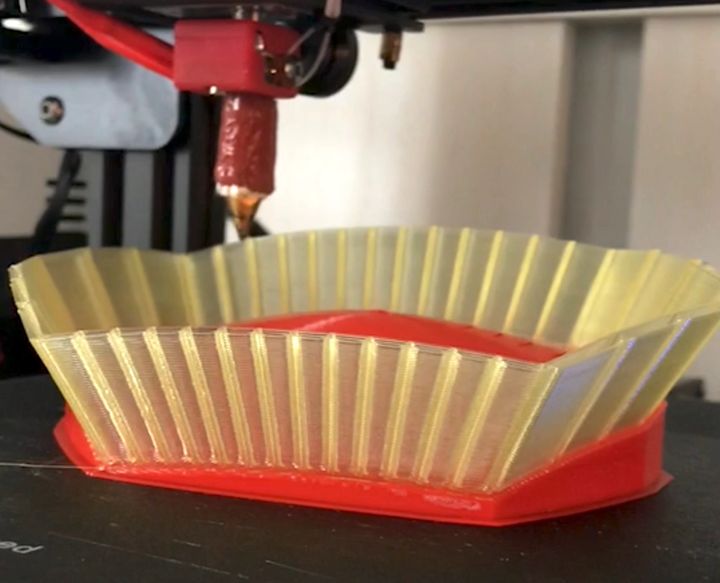
Normally 3D printers deposit material layer-by-layer in what are essentially 2D representations of each layer. These bond together to form the entire 3D object. However, by dynamically adjusting the Z-axis, it is possible to deposit material in three dimensions, not just two.
This is not something any common 3D printer job preparation software would do; all assume you are performing standard layer-by-layer operations. While the FFF machines are capable of moving in this manner, you have to develop your own GCODE to drive them in a non-planar way.
Non-planar 3D printing would achieve a couple of useful goals:
- Curved surfaces would be potentially smooth, and avoid the unsightly stair step look seen on prints from most 3D printers
- Mechanical strength could be improved as the extrusions could theoretically match the lines of force applied to the object, avoiding delamination at the weakest point: the layer boundaries
Boutin was determined to make this work, even though he is an industrial designer and not a coder. Nevertheless, he built a workflow using Rhino3D and Grasshopper to generate the non-planar GCODE to run FFF 3D printers.
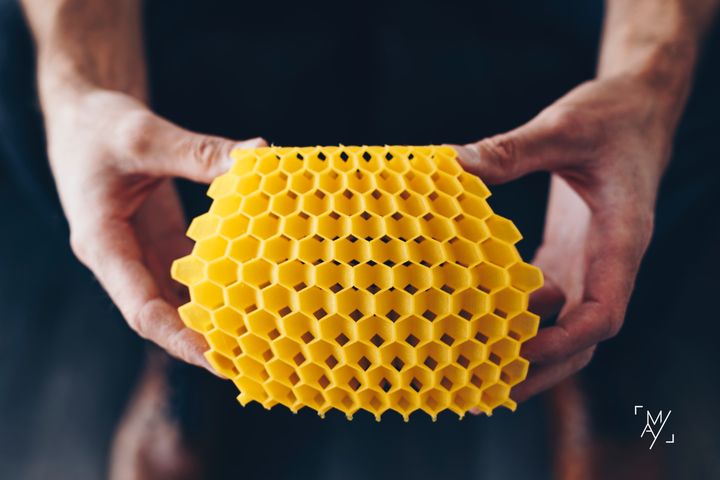
Melissa Tremblay (MAY – Photographie)]
Rhino3D is a relatively inexpensive and popular 3D modeling tool, and Grasshopper is a unique plugin that can be used to “generate” 3D models. Basically you build a flowchart that tickles the 3D model using simple programming techniques. It has been used to generate many of the highly complex 3D prints you may have seen in the media.
But it can also be used to generate text, which in this case was the GCODE. You can see a bit of how this works in this video:
Boutin explained that his approach is to take a cross-section of the 3D model to identify a curve, and then he generates the GCODE for a motion that matches the curve. The accumulation of these motions represents the non-planar GCODE.
Boutin started working on this approach only this past January, and he started from scratch learning Grasshopper and Rhino3D, which are quite a bit different from his usual toolset of SOLIDWORKS, Modo and CATIA. However, he discovered that the process of doing so wasn’t particularly difficult, and he succeeded in generating usable non-planar GCODE.
He took many, many iterations to achieve the results he desired. One of the major challenges was the ability to 3D print near-horizontally without support structures, which obviously disturb the surface texture. Incredibly, he did so by eventually finding a way to dynamically adjust speed, temperature, material flow and layer size.
His normal non-planar 3D printing configuration uses a 0.6 or even a 0.8 mm nozzle, which is quite a bit larger than the standard 0.4mm nozzle found on most 3D printers. There is a reason for this. Consider this diagram:
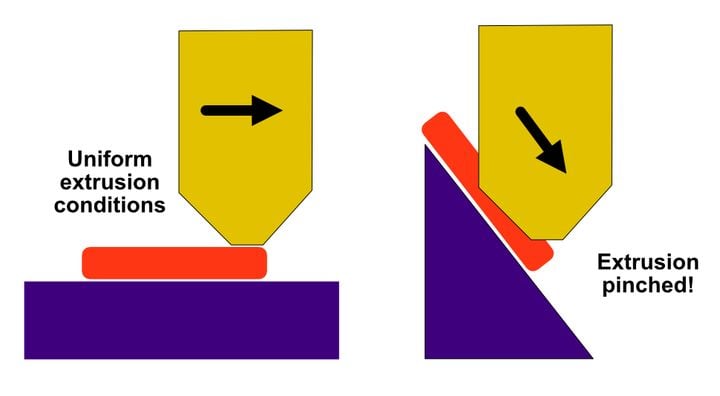
While the standard 2D extrusion has little to worry about, as the extrusion space is always the same, a non-planar extrusion must constantly adapt to the changing size of the “pinch” that occurs when the nozzle tips into the angled extrusion bead.
This meant that Boutin’s GCODE had to play with all the parameters constantly to ensure the extrusion succeeded. He explained to me that typically the layers get quite thin during these extreme situations, which makes a lot of sense. He also avoids retractions and essentially his prints are usually continuous without any breaks in the extrusion line.
Boutin explains that once you have the goal of printing continuously, you think quite differently about how to perform the extrusion. Imagine the nozzle moving along a continuously varying slope and having to dynamically adjust print parameters to account. I imagine this thought process is somewhat analogous to driving an automobile on a highway and having to occasionally add or subtract power to get up and down hills, except in multiple dimensions!
In addition to this, the nozzle itself must be quite a bit longer to enable reaching into a partial print without bumping into any already-printed portions. For this he’s developed a series of extra-long nozzles, which he offers for sale.
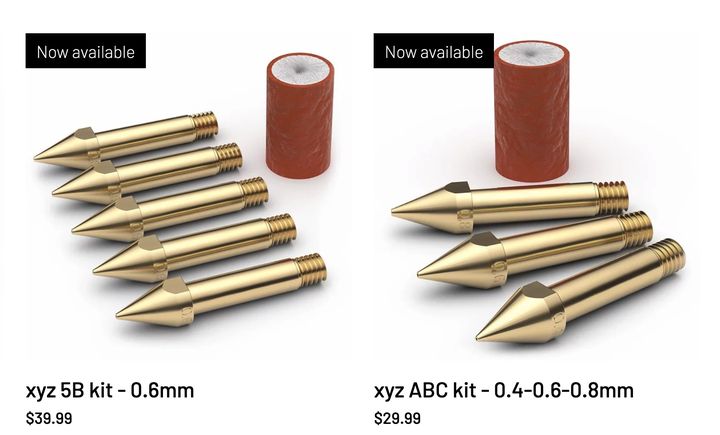
Using this non-planar approach Boutin has been able to successfully 3D print various complex shapes in multiple types of TPU — without support structures. One wonders why the many 3D printer companies haven’t also figured this out by now. Perhaps they may, having seen Boutin’s example.
But is this non-planar approach something that can be used by anyone for 3D printing anything?
Not exactly. There are obviously some geometric constraints, but for dome-like objects, such as helmets, heads, insoles and other products, this can actually be used.
However, Boutin explained that it’s more like a workflow than a product, as you must do tweaking for each and every 3D model to achieve the correct results. He says that it is a lot simpler to do than it appears, so likely most people could give this an attempt.
It’s not like a slicer where you drop a model and hit “Print”. It’s more like a toolkit.
Nonplanar.xyz
Boutin said:
“I don’t want to be the only guy doing this!”
His company, kupol, is focused on using the method to develop helmet prototypes, but he has also launched a separate site, nonplanar.xyz, to help get the word out to the world about this unusual workflow. He’s currently looking for others with interest to help make the system work even better.
If you’re interested in helping advance the concept of non-planar 3D printing, please check out the site.
Via Nonplanar.xyz