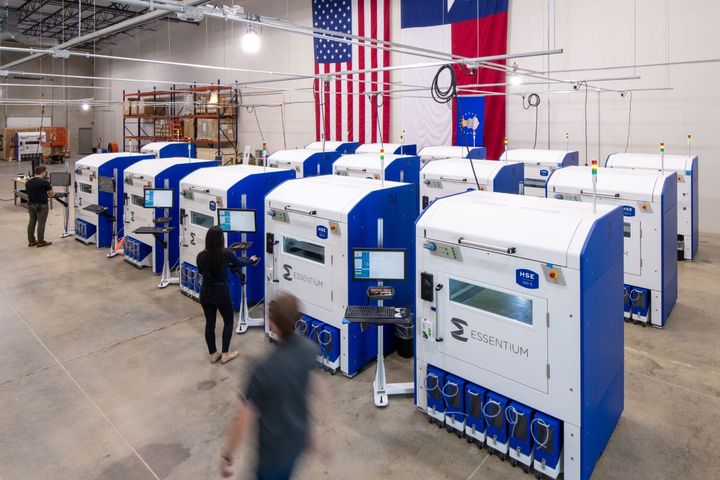
SPONSORED CONTENT
Many 3D print companies service the aerospace industry, but it appears that Essentium is doing things in quite a different way.
For years the typical approach was to simply 3D print aerospace parts in a more suitable material beyond the common ABS, PET and Nylons offered by most companies, such as ULTEM or PEEK. Both of those materials carry higher thermal resistance as well as significant chemical resistance.
But they are also quite expensive.
That wasn’t a problem for some 3D print vendors, as selling expensive products is not usually an issue for them. However, it can be an issue for aerospace companies seeking to get the most value for the dollar.
What is surprising is that the vast majority of 3D print companies still use this business model; we make it, you use it.
That’s perhaps one of the reasons 3D printing has not penetrated as deeply into the aerospace industry as it should have.
Essentium seems to be taking a very different approach, one in which they work directly with the aerospace clients to figure out optimal solutions that are not necessarily obvious at first glance.
Essentium Strategy
The Essentium Strategy is based on a fundamentally different approach to the physical aspects of 3D printing. They’ve developed a unique 3D printing system, the High Speed Extrusion (HSE) 3D Printer, which derived much of its design from the founders’ previous experience building ultra-high speed pick-and-place machines for the semiconductor industry.
In that world they discovered how to build machines that move very quickly, and this technology was provided the foundation for Essentium’s HSE 3D printer.
The second part of their strategy involves “open”. They designed their HSE 3D printer to be an open materials machine, meaning that it can theoretically use any physically compatible material, as opposed to requiring the use of proprietary materials, usually at prohibitive cost levels.
Finally, their system uses an open process that provides a tremendous amount of flexibility.
Essentium in Aerospace
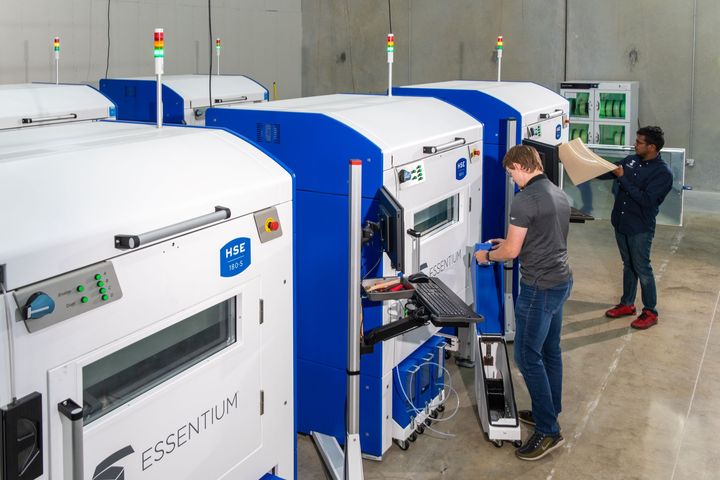
To target the aerospace industry, Essentium leverages all of these advantages to provide a deep partnership with clients on projects to enable optimal use of the technology. Instead of simply saying “this is the answer”, and pulling a solution off the shelf, they have been working directly with clients to deeply understand their needs and then develop solutions precisely for that scenario.
This is where their open strategy gains the advantage, as that flexibility allows them to design a solution that fits the client.
One example of this flexibility is the use of composite materials. While it’s easy to say “let’s use ULTEM” in an application, the truth, according to Essentium, can be far more complex.
ULTEM may functionally work, but might be too expensive for the application to justify. Instead Essentium might propose the use of a composite material made from carbon or glass fibers that are surprisingly strong and can be used in place of ULTEM at lower costs.
Sometimes this exchange is not obvious, as the basic engineering properties may not seem to match the scenario: ULTEM does have a higher heat resistance than the binding polymer in a composite material, so an engineer may suspect that the composite material may not work.
Essentium’s experiments have shown that the addition of carbon fibers in a material raise the effective heat resistance notably, a fact that some engineers may miss when quickly looking at spec sheets. There’s also the question of heat exposure duration — a short duration exposure, say, a jig passing through a heat booth on an assembly line — may not deliver enough heat to warrant the use of the more expensive material.
Essentium Materials
Although Essentium is known today for their industrial 3D printers, they were originally a materials company. I have a suspicion they are really still a materials company, one that happens to also market 3D printers.
As such they have continued to develop unusual functional materials for these aerospace and other industry applications. One very interesting approach is their use of “sausage” filaments.
The idea here is that you want as much carbon fiber as possible in the filament to gain strength. However, if you made the filament out of a very high ratio of carbon fiber, it would simply snap when bent and could not even be spooled.
Essentium came up with the amazing idea of a “sausage” filament, in which the high-carbon ratio material is on the inside, and a strong, but very thin outer layer — like a sausage — holds the carbon fiber safely inside.
Another interesting Essentium discovery is that the use of semi-crystalline materials vs amorphous materials can provide significantly greater heat resistance, even though the Tg value would suggest otherwise.
Some of these materials are have a higher strength to weight ratio than metals, and can be used instead.
Essentium has been experimenting with 3D printed injection molds, and has been successful using these unusual materials. They have been able to create molds that can withstand many injection shots, and this could be quite a bit less expensive than traditional metal molds for injection molding. Essentium often compares results with their in-house injection molding system and has found near-equivalent results.
It’s with tools like this Essentium is able to provide very interesting aerospace solutions.
There’s more.
Essentium Hardware
Essentium has made some unusual design choices to their HSE 3D Printer hardware to aid in the production of aerospace parts.
One is that the parts printed have far stronger layer adhesion than typical 3D printers. This is apparently due to the speed of the printer. While you’d think printing faster might decrease layer bonding, the opposite actually happens. The reasoning is that if the second layer comes around quickly, it will be 3D printed on top of a still-hot bottom layer and thus bonding will be increased.
Another interesting hardware feature is the use of a sapphire tip in the extrusion nozzle. This is an extremely hard material that can easily withstand abrasive materials such as carbon fiber. However, the idea here is that you want to maintain a very precise nozzle diameter during long and continuous 3D print jobs. With softer brass or even steel nozzles the abrasive materials will slow erode the nozzle and the extrusion amounts will subtlety change. That can’t happen on the Essentium HSE 3D Printing Platform.
Essentium and Aerospace
These tools, combined with Essentium’s “partner approach” on customized customer solutions can provide a unique solution for aerospace companies.
By leveraging the materials and hardware they can provide solutions that are scalable. Once the chemistry of the solution is developed, it is possible to 3D print larger quantities of parts using the very fast HSE 3D Printer. Often the cost per part is lower than one would expect due to the use of lower cost, but still effective materials.
This opens up the possibility for aerospace companies to create new applications for 3D printed parts within their operations. This would extend well beyond mere prototyping, and could include production end-use parts, jigs & fixtures, and replacement parts, particularly where no supplier exists.
In fact, these aerospace advantages are being noticed, as Essentium recently announced a new contract with the USAF. The multi-year arrangement enables Essentium to provide the USAF with advanced 3D printing for tooling, ground support, maintenance repair and overhaul, as well as for the production of flight-certified parts.
If you’re an aerospace provider, you might want to check out Essentium’s intriguing offer.
Via Essentium