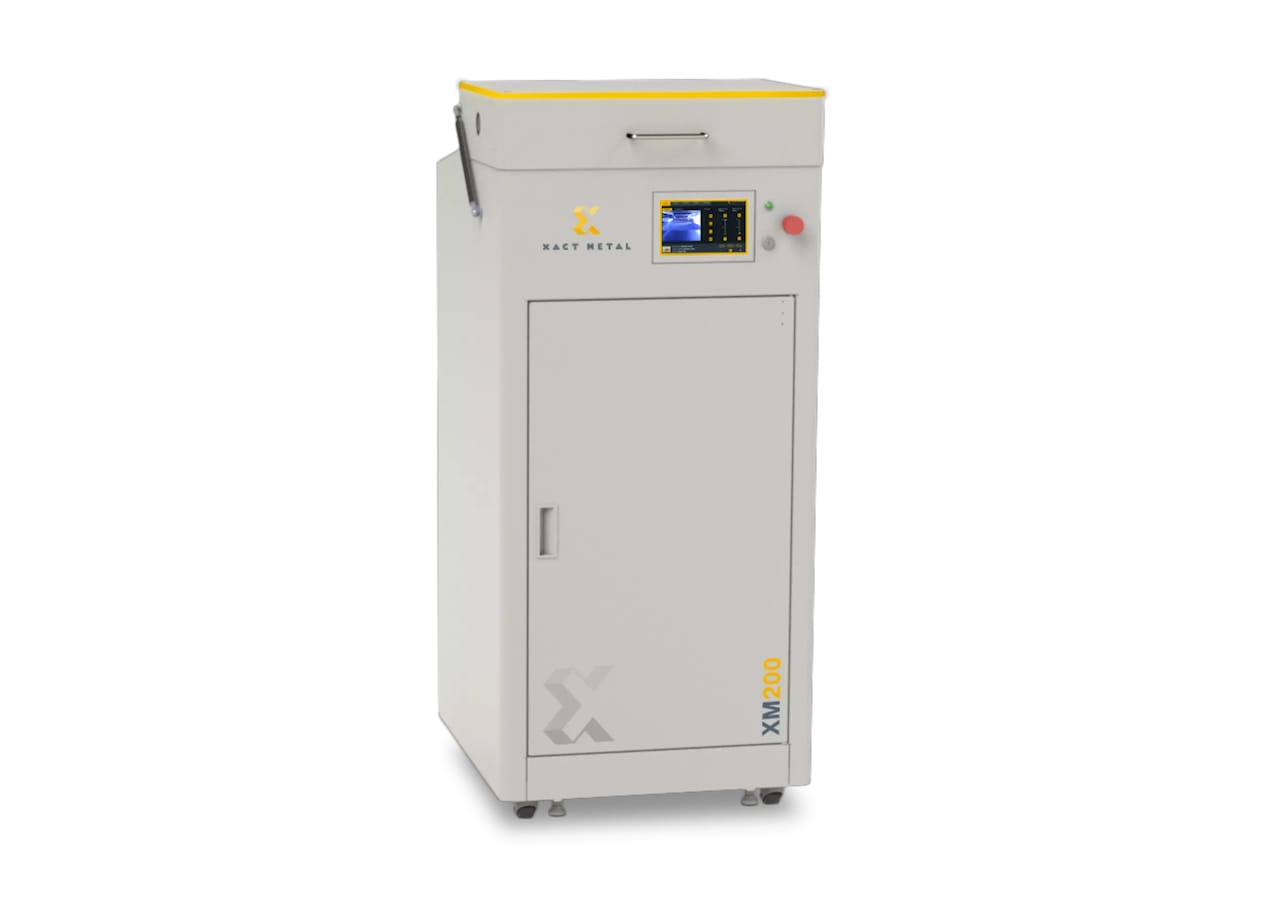
This year’s RAPID + TCT show was abuzz with news about Desktop Metal, an exciting new metal 3D printing startup that has already raked in millions of investor dollars.
However, Desktop Metal was not the only company to showcase novel techniques for metal additive manufacturing (AM). In fact, there were several firms at the show that displayed their unique methods for 3D printing metal, including 3DEO, Admatec and Markforged.
While all promise the ability to 3D print metal parts at lower price points, only one startup at the event unveiled a platform that promises to deliver the same parts one sees with typical powder bed fusion systems, like those from EOS, at such a low cost. Xact Metal is a Pennsylvania-based company that has developed a powder bed fusion metal 3D printer that it plans to sell for just $120,000.
ENGINEERING.com spoke to the company’s CEO, Juan Mario Gomez, and CTO, Matt Woods, to learn more.
From Multi-Metal to Low-Cost Metal 3D Printing
While attending Pennsylvania State University and working at the school’s CIMP-3D AM lab, Woods came up with the idea for a 3D printer capable of melding multiple metals in the same build. However, to prove out his concept, Woods couldn’t exactly tinker with the prestigious lab’s million-dollar equipment. Instead, he was left to his own devices.
Woods was able to obtain bits of funding here and there through grants from Penn State, as well as incubators and Pennsylvania’s Ben Franklin Technology Partners program. “When I finished my degree, I decided to work on the technology full time at Innovation Park at Penn State. I began recruiting some fellow students and friends that I knew to be very talented in what they do, which is either building things or designing things or manufacturing,” Woods explained.
In the process, he and his team came up with a new approach to laser metal 3D printing.
“We began prototyping our own metal powder bed fusion system—basically made on a shoestring budget,” Woods said. “Through that, we had developed this system that allowed us to bring down the cost of a metal system, but at the same time have the performance characteristics of a high-end system. That was kind of the genesis of what we now use as our platform that allows us to deliver a laser beam in a slightly different way than is currently done in the industry.”
As Woods began to transition the technology away from multi-metal 3D printing and toward low-cost metal AM, he began working with Gomez, a manufacturing veteran who had spent over 25 years working with GE. It took just about nine months between the time that Gomez entered the picture and Xact Metal was able to debut its flagship XM200 system at RAPID + TCT this past May.
Cost Constraints Drive Innovation
It was actually the cost constraints of Xact Metal’s development process that allowed Woods and his team to invent the company’s novel method for metal 3D printing. Gomez explained, “He bought a used binder jet printer, took it all apart and, on that foundation, he built a new system that replaces the galvanometer mirrors typically found in a powder bed fusion process with an X-Y gantry system.”
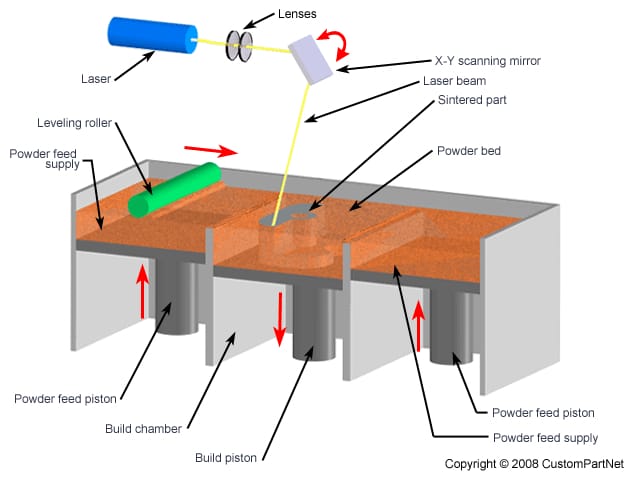
In traditional laser-based powder bed fusion 3D printers, at least one powerful laser is directed at a series of galvanometer mirrors, which rotate quickly to bounce the beam at a bed of metal powder, fusing the particles together. Although the mirrors are small, the mirror systems themselves are bulky, heavy and expensive to buy and maintain.
Xact Metal has done away with the galvos and replaced them with what the company calls the “Xact Core” an X-Y gantry system, which sees lighter, less expensive mirrors mounted onto a gantry that moves them in the X- and Y-axes above the powder bed.
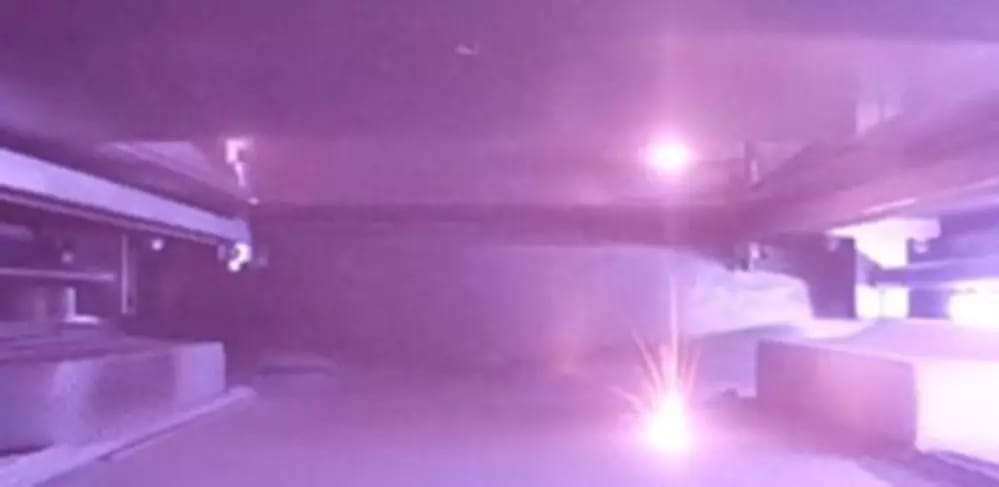
“The problem that we had is that because they are very, very small, the galvo mirrors move very, very fast,” Gomez said. “They can move up to seven meters per second on a point-to-point translation. But the real performance needed for fusing requires moving the mirrors at about 800 to 1,500 millimeters per second. We knew that if we were able to match the fusing equivalent speeds of galvos, we would be in the ballpark of an equivalent printer.
“Several people have thought about replacing the galvanometer mirrors, but could not make it work. We had to apply a variety of tricks with the printer—how it’s setup, its performance, how to move the mirrors around and control the whole architecture—to be able to invent this and make it work. It sounds simple, but it wasn’t so simple to get there,” Gomez explained.
Xact Metal’s original proof-of-concept machine could scan the printbed at a sluggish 100 millimeter per second; however, with some proprietary innovations, for which the company has filed some patents, Xact Metal was able to increase the speed up to 1.5 meters per second. “We still use mirrors, but instead of rotating them, we translate the mirrors and keep the gantry as lightweight as possible to move it as fast as possible,” Woods said.
Read more at ENGINEERING.com