Brake Caliper Cover Made with RPU 130 — Painted/unpainted brake caliper covers are an example of an automotive application that benefits from RPU 130 unique strength and heat resistance qualities. [Image: Carbon]
A new rigid polyurethane material from Carbon proves interesting for both its performance properties and the story of its development.
Digital manufacturing giant Carbon hasn’t slowed its pace since its high-profile debut several years ago of its surprisingly high-speed 3D printing process. Most updates we hear lately about the company include partnerships for end-use products created with their digital manufacturing platform and available at volume — including products, like shoes, for the everyday consumer.
But one of Carbon’s perhaps underemphasized strengths is one of its strongest points: its materials portfolio.
Carbon Materials
Digital Light Synthesis (DLS) 3D printing is compatible with a growing library of materials with various attributes.
From flexible to help put bounce in a shoe step to foamy for cushion in high-performance helmets, the materials range at Carbon is growing quickly to meet real-world customer needs. Working to meet those needs means a highly dedicated materials team working to understand exactly what conditions need to be met.
The latest material, introduced last week, takes several desirable performance qualities to roll into a single resin.
RPU 130
The new material is a rigid polyurethane, expanding Carbon’s RPU portfolio.
RPU 130 offers toughness, rigidity, and high-temperature characteristics, adding “superior impact resistance and dimensional stability at elevated temperatures that no additive material could address,” Carbon notes. Not only that, but its partially plant-based derivation ensures that it fits the bill for more sustainably-made goods.
Creating the material was, it turns out, quite an endeavor.
Matt Menyo, Senior Product R&D Manager at Carbon, tells Fabbaloo of the process:
“As the team at Carbon set out to develop RPU 130, we knew that achieving the toughness, rigidity, and temperature resistance expected of engineering thermoplastics in a material that could be printed with the high resolution and detail of a light-based process would be a challenge. We tackled this head-on, screening a large library of oligomers, diluents, hardeners and functional additives to identify optimal polyurethaneurea candidates. The team paired this expertise in materials formulation with the integrated hardware and software of Carbon’s DLS process to develop, refine, and launch a groundbreaking material that accesses this previously uncharted materials property space.”
Bringing all of these characteristics, each individually available in other Carbon’s resins, like RPU 70, FPU 50, and EPX 82, into a single material represents quite an achievement — especially considering the manufacturing process the material must then endure.
Carbon reports that RPU 130 is a “tough, heat and impact resistant material, similar to ABS, unfilled nylon, or polypropylene.” It is suited for use in production of both industrial (e.g., air ducts, tool housings, brake caliper covers) and consumer (e.g., sunglasses) products.
On top of materials science, RPU 130 relied heavily on advances in Carbon’s software and hardware. The company reports:
“In addition to the new dual-cure resin, Carbon is offering a new heated C5 Cassette required for use with the material, a new dispensing solution, and tuning via software to ensure great end-use products.”
Material Quality
Carbon developed RPU 130 in partnership with DuPont Tate & Lyle Bio Products.
The partnership enabled use of Susterra propanediol, a bio-based raw material that produces significantly fewer greenhouse gas emissions and uses less nonrenewable energy than petroleum-based options. Susterra comprises almost 30% of RPU 130.
“We are focused on ways to incorporate more sustainable approaches to developing materials, and our partnership with DuPont Tate & Lyle emphasizes that commitment. We believe that sustainability can go hand-in-hand with improved performance. In the case of RPU 130, we believe it will make the material even more appealing for our customers, as it makes it possible to create better quality products that are also ultimately better for the environment,” said Jason Rolland, SVP of Materials at Carbon.
On top of its more eco-friendly profile, RPU 130 delivers where it counts: performance.
Carbon has supplied helpful graphs to indicate RPU 130’s performance attributes as compared to other Carbon materials (left) and to injection molded materials (right):
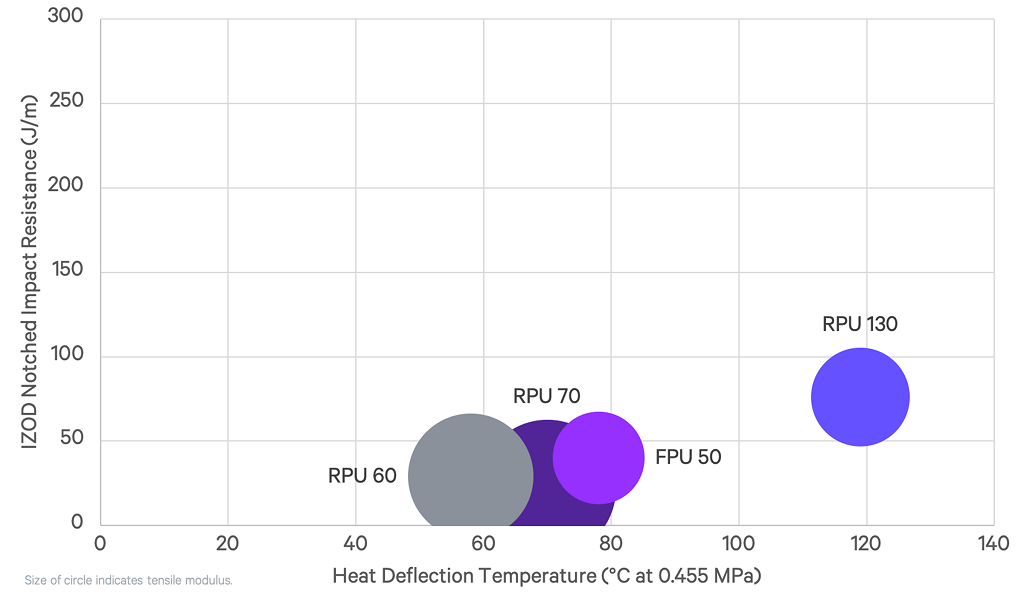
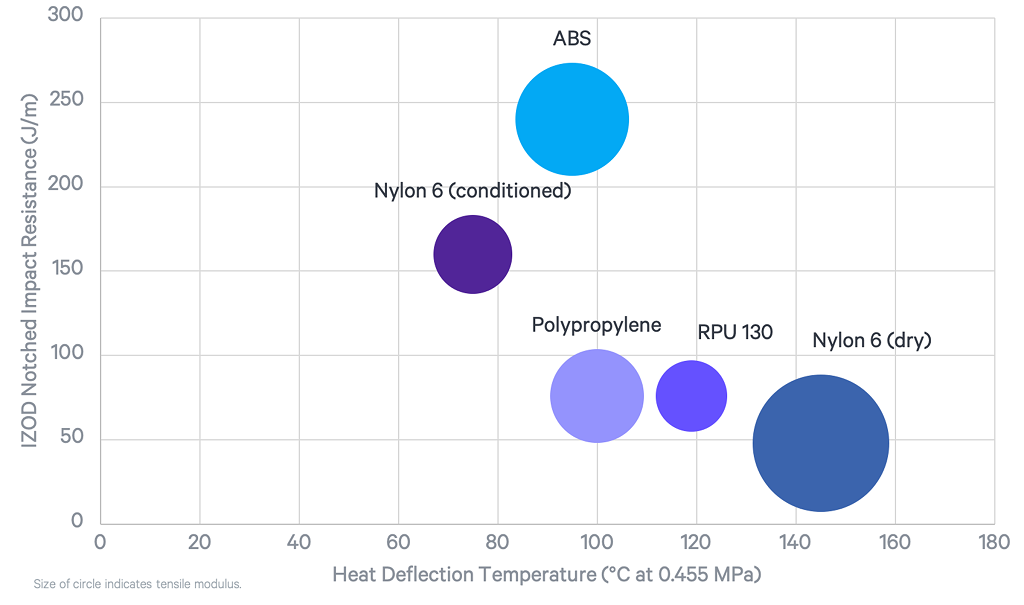
Carbon RPU 130 is available now.
Via Carbon