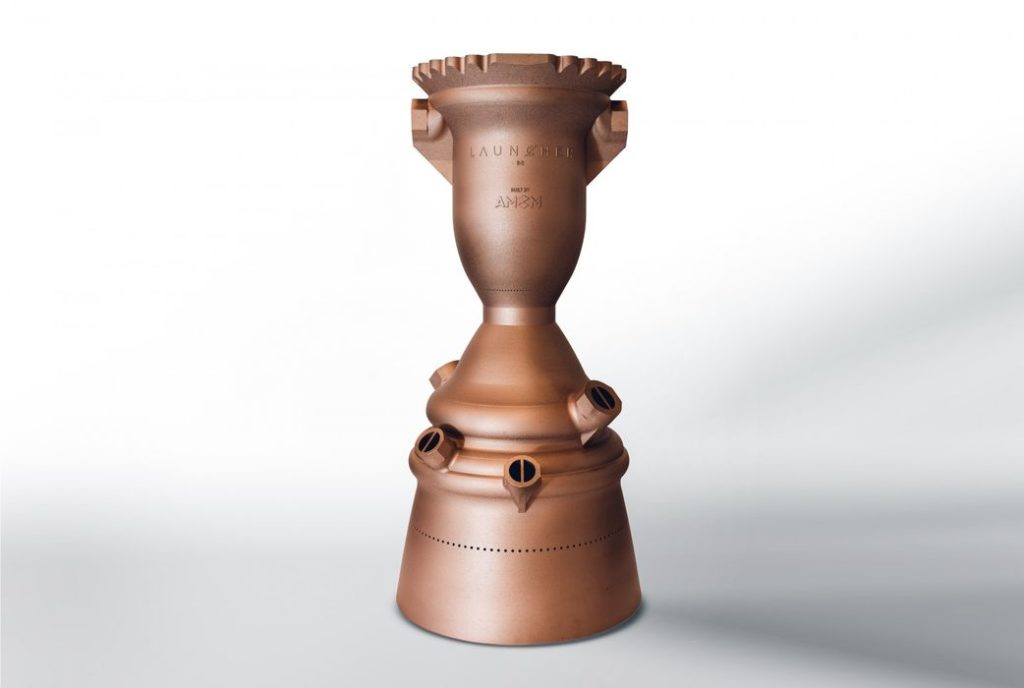
Launcher has successfully tested a unique 3D printed copper rocket engine.
Launcher is one of several space startups vying for a chunk of the expected space transport boom in coming years. They were founded only in 2017, and are based in Hawthorne, California — which just happens to be the same city as another player in the sector, SpaceX.
Launcher projects the number of satellites to be launched annually will reach 5,000 by 2025, and that’s where their target market will be found. To do so, however, they need to develop a launch system that is able to compete with the increasingly effective systems developed by others.
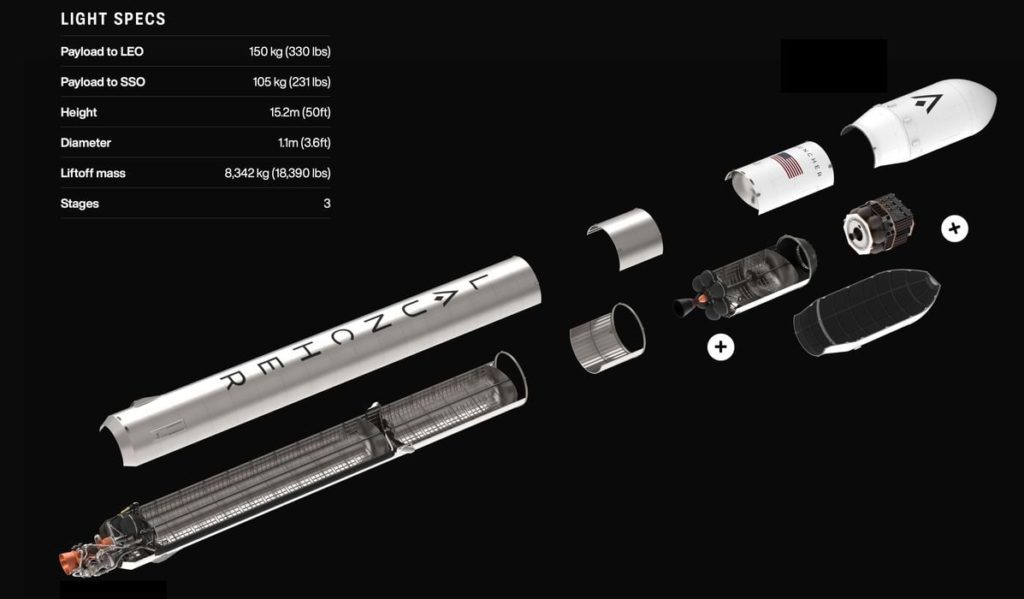
The Launcher system is based around their initial launch vehicle, the “Light”. It’s a relatively small system, with a payload capacity to low earth orbit of only 150kg. (For perspective, SpaceX’s Falcon 9 system’s LEO payload is 22,800kg.)
Launcher is focused on the cubesat market, where small standard-sized satellites are deployed in orbit for experimental purposes. Typically these are launched in “rideshare” mode, where they piggyback on an existing launch at low cost. However, these cubesats end up in the same orbit as the primary payload.
Launcher’s system solves this issue with their “Orbiter” vehicle, which is a kind of orbital taxi that can take small cubesats to different orbits. It’s a very interesting concept that I haven’t seen developed by any other company.
But all of this depends on the rocket engines involved in these vehicles. Launcher has chosen to 3D print them, as is customary in the aerospace industry these days. Launcher’s design for the E-2 engine is a single, 3D printed part. This approach minimizes weight due to the loss of mass for bolts that would otherwise hold the parts together, and also increases reliability: there are no seams to fail.
The E-2 is 3D printed entirely in a copper alloy, because the running engine requires a means to remove heat, and copper is an excellent conductor. Launcher said they are the first company to use copper alloys for an entire rocket engine.

As we reported last year, Launcher is using a custom metal 3D printer developed by AMCM, the MK4. This is a rather large device with a build volume of 1000 x 450 x 450, and is actually based on an EOS M400 platform.
Somehow AMCM was able to adapt the MK4 to 3D print the copper alloy, which is notoriously challenging to print using LPBF technology. It’s not clear what they modified, but I’m interested to find out more.
Launcher also 3D printed the E-2’s injector using a Velo3D Sapphire system.
But did this all work? Apparently so, as they successfully executed a full-thrust test last week:
This test demonstrates the viability of their unique copper rocket engine, and opens the door for more companies to examine the use of copper in their own designs.
Via Launcher