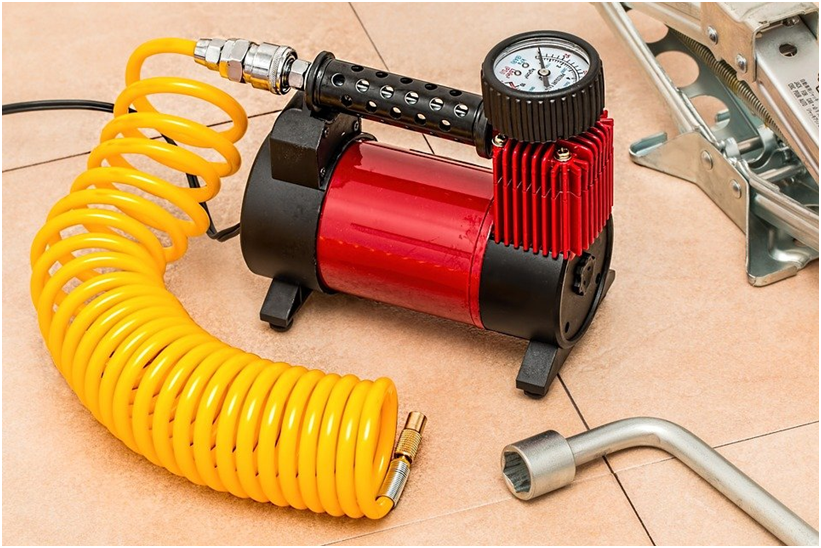
Charles R. Goulding and Randy Rothbort take a look at the growing relationship between the air compressor industry and 3D printing.
The air compressor industry is diverse and long-standing with a plethora of applications, be it commercial, medical, or scientific. However, the development of compressors is starting to undergo changes due to many innovations, most notably the introduction and incorporation of 3D printing. Be it through additive manufacturing methods for product prototyping and construction, or 3D printing business partners who heavily utilize air compressors for their work, 3D printing is becoming a major part of the air compressor industry.
3D Printing Innovations
Many air compressor manufacturers have taken to 3D printing to design and produce their products. Atlas Copco may have had the most significant 3D printing overhaul. In collaboration with Sirris, a nonprofit organization focused on innovative engineering, Atlas Copco went through and evaluated every part in their list of compressor components to determine which ones could be suitable for 3D printing, rather than their standard production techniques. This was a huge undertaking that led to a large number of parts being 3D printed instead of machined. Some parts were redesigned to support 3D printing, while others were natural fits for additive manufacturing.
Another company that has taken to 3D printing is Ingersoll-Rand, which partnered with Oak Ridge National Lab (ORNL) to produce a large-scale 3D printer, called Wide and High Additive Manufacturing (WHAM). This 3D printer can print objects measuring up to 23 ft. x 10 ft. x 46ft. Ingersoll-Rand has already incorporated 3D printing into many of their compressors, most notably their shrouded impellers which are fully 3D printed, and the company has continually evaluated how additive manufacturing can be incorporated into their air compressor assemblies. However, this is a new venture on a scale that is unheard of in the 3D printing industry.
Carnot Compression of Scott Valley, California is a startup compressor company that utilizes a unique centrifugal design to compress air through the weight of water. These compressors, which are oil-free, considerably quieter, and with fewer moving parts, have taken a huge deal of prototyping to build. To find the right dimensions and sizes for the device, Carnot fully 3D printed the entire device. Throughout testing, 3D printing was done to iterate on parts and make consistent improvements to their R&D work.
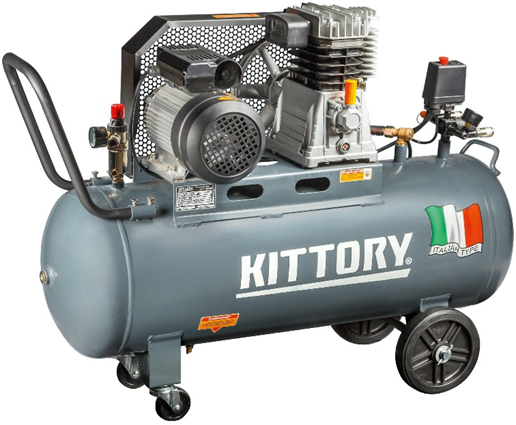
Compressors for 3D Printing
Other air compressor companies have made direct connections to supply their compressors to 3D printing companies. Kaeser Compressors has a relationship with 3D Printing Systems of Australia, which utilizes compressed air for their printers and sources their compressors from Kaeser. Their 3D printers require a controlled atmosphere with inert nitrogen, and Kaeser compressors accomplish this by passing compressed, clean air through a nitrogen generator. FPS Air Compressors have developed air compressors made that are specifically compatible with 3D printing applications, specifically their MICRO line of air compressors.
3D printing is quickly becoming not just a vital part of prototyping and development, but also a growing part of business for the air compressor industry. Companies utilizing 3D printing to develop, test and produce air compressors may be eligible for Research and Development (R&D) tax credits.
The Research & Development Tax Credit
Whether itās used for creating and testing prototypes or for final production, 3D printing is a great indicator that R&D credit-eligible activities are taking place. Companies implementing this technology at any point should consider taking advantage of R&D Tax Credits.
Enacted in 1981, the now permanent Federal Research and Development Tax Credit allows a credit that typically ranges from 4%-7% of eligible spending for new and improved products and processes. Qualified research must meet the following four criteria:
- Must be technological in nature
- Must be a component of the taxpayerās business
- Must represent R&D in the experimental sense and generally includes all such costs related to the development or improvement of a product or process
- Must eliminate uncertainty through a process of experimentation that considers one or more alternatives
- Eligible costs include US employee wages, cost of supplies consumed in the R&D process, cost of pre-production testing, US contract research expenses, and certain costs associated with developing a patent.
On December 18, 2015, President Obama signed the PATH Act, making the R&D Tax Credit permanent. Since 2016, the R&D credit can be used to offset Alternative Minimum Tax (AMT) or companies with revenue below $50MM and, startup businesses can obtain up to $250,000 per year in cash rebates that can be applied directly to payroll taxes.
Conclusion
3D printing is rapidly becoming an important tool in the air compressor industry, as well as a key source of business. The ability to print out parts for prototyping, as well as parts used in the assembly of the compressors, helps to innovate this business and bring more modern and interesting products to the market. As 3D printing continues to evolve and improve, the air compressor industry will surely do the same.