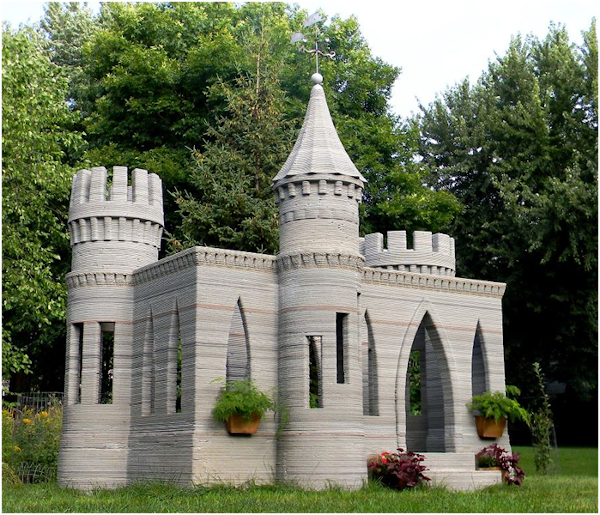
Charles R. Goulding and Peter Favata take a look at concrete 3D printing for various uses.
Advancements in construction technology have always been critical to the industry for making jobs more efficient and structures more durable throughout their intended lifetime. The use of additive manufacturing in construction has been one such application increasing in the past few years.
3D printing with concrete can help quickly and efficiently create benches and chairs, art, or even entire homes. Utilizing 3D printing also helps to prevent material waste. Compound this with the low cost and high production speed, 3D printing concrete offers an environmentally friendly way to handle construction.
Columbia University Engineering School has noted the benefits of 3D printing as opposed to traditional methods. Professor Shiho Kawashima stated in a Columbia University news article âwe can lower material and labor costs, reduce material waste, cut construction time, and minimize human error.â
Outdoor Seating
Using 3D printing to produce benches and chairs for public use has many benefits and continues to grow in popularity. Concrete benches are much more durable compared to traditional metal and wood benches, which need continued maintenance throughout the years, after becoming weathered by the elements. 3D printing concrete allows for designs in a much shorter time when compared to making concrete benches using traditional methods.
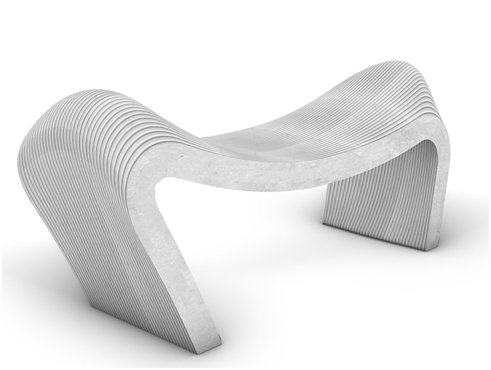
Concrete Art
When it comes to concrete art, there is a strong emphasis on geometrical abstraction. It is for this reason that 3D printing is the perfect tool for creating various types of structures out of concrete. 3D printing allows for unique designs and structures to be actualized that otherwise could not be possible to produce using traditional molds.
Recently, graduate students at ETH Zurich used robotics to create a series of 2.7-meter columns with custom patterns, only made possible through high-resolution 3D printing. Columns were created for a series called Concrete Choreography. The design for the columns created strength with minimal material and without any framework or molds.
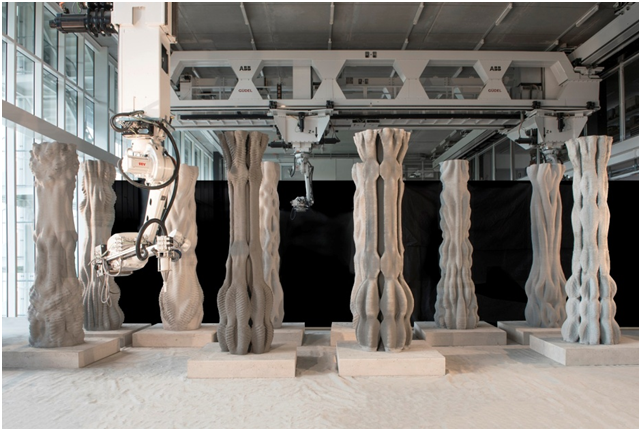
Offshore Wind Energy
The global offshore wind energy is a growing industry with a nearly 30% per year increase between 2010 and 2018. This growth is relevant because large amounts of concrete are required for the foundation of a singular wind turbine, let alone an entire offshore wind farm.
Building wind turbines offshore is expensive and requires parts to be shipped about 30 miles away from the coast. 3D printing concrete could offset transportation costs by having concrete components printed onsite. Purdue University engineers are researching the feasibility of 3D printing concrete anchors for floating wind turbines instead of using steel. Not only is concrete less expensive than finished steel, but 3D printing concrete components would eliminate the added expense of molds required for traditional concrete manufacturing.
The researchers are working in collaboration with RCAM Technologies, a startup founded to develop concrete additive manufacturing for onshore and offshore wind energy technology, as well as the Floating Wind Technology Company.
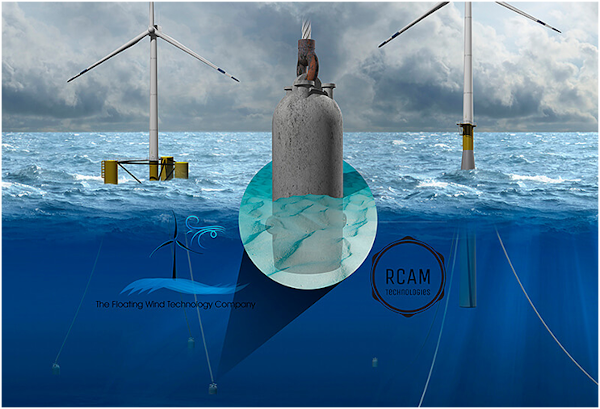
Construction of Houses
One of the most common yet most useful applications for 3D printing concrete is for the construction of houses. The walls of a small single-story house can now be constructed in as little as 12-24 hours using 3D printing, compared to the weeks-long construction process to make a similar-sized house using regular methods.
One company at the forefront of producing these small houses is the Austin-based startup ICON. In 2018, ICON became the first U.S. company to secure a building permit for a 3D printed home. Since then, the company has been constructing homes with its portable near-zero waste Vulcan II 3D printer. Their goal is to leverage 3D printing to provide underserved communities with customized 400-square-foot homes that are not only affordable but durable and built faster than ever. Currently, they have priced the houses at $10,000 for a single-story home but are trying to drive the cost down to $4,000 in the near future.
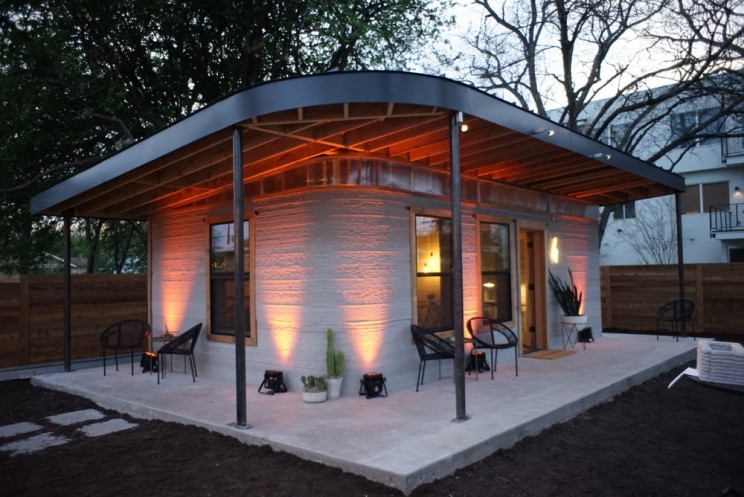
Manufacturers and designers utilizing concrete 3D printing may be eligible for R&D Tax Credits.
The Research & Development Tax Credit
Whether itâs used for creating and testing prototypes or for final production, 3D printing is a great indicator that R&D credit-eligible activities are taking place. Companies implementing this technology at any point should consider taking advantage of R&D Tax Credits.
Enacted in 1981, the now permanent Federal Research and Development (R&D) Tax Credit allows a credit that typically ranges from 4%-7% of eligible spending for new and improved products and processes. Qualified research must meet the following four criteria:
- Must be technological in nature
- Must be a component of the taxpayerâs business
- Must represent R&D in the experimental sense and generally includes all such costs related to the development or improvement of a product or process
- Must eliminate uncertainty through a process of experimentation that considers one or more alternatives
Eligible costs include US employee wages, cost of supplies consumed in the R&D process, cost of pre-production testing, US contract research expenses, and certain costs associated with developing a patent.
On December 18, 2015, President Obama signed the PATH Act, making the R&D Tax Credit permanent. Since 2016, the R&D credit can be used to offset Alternative Minimum Tax (AMT) or companies with revenue below $50MM and, startup businesses can obtain up to $250,000 per year in cash rebates that can be applied directly to payroll taxes.
Conclusion
3D printing concrete has improved the construction of a variety of different structures. With lower costs and faster turnover, it more efficient than traditional methods of concrete forming.