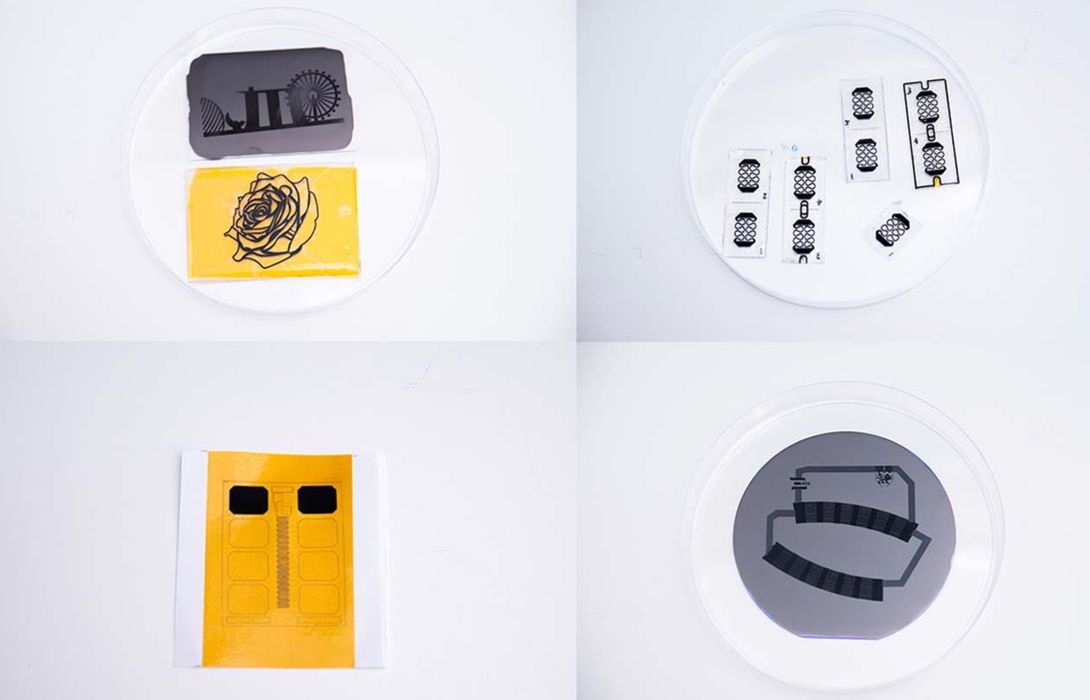
Researchers have identified an unusual way to 3D print flexible materials.
Work done at the Nanyang Technological University, Panasonic and the Singapore Centre for 3D Printing have devised a way to leverage variable wavelength laser energy to 3D print flexible materials.
Their approach used a custom-designed multimaterial 3D printer where the frequency of the laser is varied throughout the print job. They found that it was possible, with the correct frequencies, to change common polyamide and graphene oxide into a āhighly porous grapheneā.
If youāre not familiar with graphene, it is a highly unusual material. Atomically, it is a hexagonal lattice of carbon atoms that provides extraordinary strength, as each atom is connected with three neighboring atoms.
Graphene is a āsemi-metalā, and provides conductive properties in addition to tremendous strength.
The interesting part in this research is that the graphene is formed into a porous structure, meaning that it can be deformed, unlike a solid block. This is similar to 3D printing a thermoplastic in a lattice structure to provide some 4D impact resistance. However, in this case the base material is far, far stronger. And conductive.
Associate Professor Murukeshan Vadakke Matham explained:
āOur project aims to find a way to 3D print new materials like organic polymers and carbon-based materials like graphene, which has properties that allow them to be printed or coated onto flexible substrates like plastics or fabrics, creating flexible and stretchable circuits.ā
One application for this technology is to 3D print the porous graphene directly onto other flexible surfaces. This enables the development of flexible electronic devices, as the electricity can flow through the deformable graphene structure.
Murukeshan added:
ā3D printed flexible electronics paves the way for more comfortable and mobile wearable devices as it can be lighter and smaller. We can now create unique structures that were previously impossible with traditional rigid electronics.”
Could this be commercialized? It seems so, as the research has attracted the interest of noted contract manufacturer JABIL through JABIL-MTI Penang. They are already producing proofs-of-concept using the technology.
Panasonic has set up a new laser manufacturing facility in Singapore, with a mind to perform further testing of the technology. They intend on producing a series of components for trials, and will integrate the technology into a new autonomous factory concept under development.
This is an important development, as it provides a way to relatively easily produce flexible conductive material that can easily be interested into 3D printers. The process used appears to be compatible with industrial 3D printing processes, which could in turn lead to mass production of 3D printed flexible devices.
Via NTU