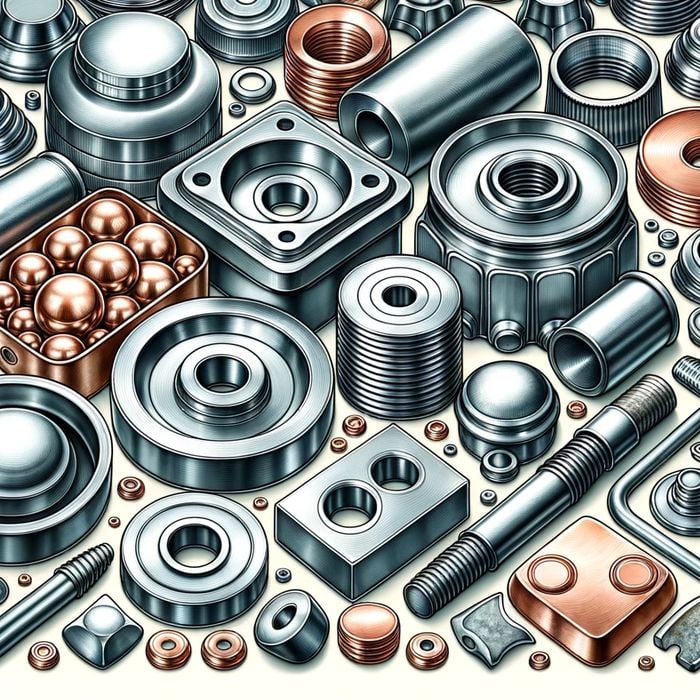
Charles R. Goulding and Andressa Bonafe have a conversation with Sarah Jordan, co-founder of the revolutionary Skuld LLC.
Sarah Jordan is the co-founder of an innovative company with an ambitious vision. Pioneering a sustainable process that combines 3D printing and lost foam casting, Skuld LLC aims to overthrow conventional metals manufacturing and save the world. Its mission is to get metal parts made in the most environmentally friendly and efficient manner which saves time, money, and the planet. We reached out to Sarah to discuss her ground-breaking work.
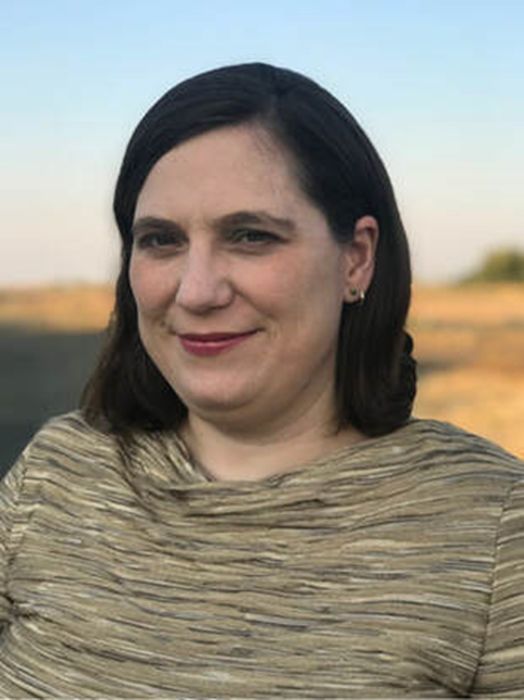
For starters, we are curious to know a little bit about yourself, your background, and what were the professional and educational experiences that led you eventually to co-found Skuld LLC.
I’m a metallurgical engineer. That is a very specialized degree that focuses on the study of metals, including every aspect of processing, finishing, and use. As for my career, early on, I did what is usual in metallurgy, like working in foundries, heat treat shops, machine shops, steel mills, that kind of thing. But one of the areas that I worked in, which I always enjoyed and I thought had a huge potential, was a type of casting called lost foam casting. It is actually the greenest casting process, according to the Department of Energy. It isn’t really that common of a process because it has historically had very high tool costs, which restricted it to high-volume applications, like automotive parts.
We started Skuld LLC because we wanted to tackle this issue. We realized that if we could combine 3D printing with lost foam, we could eliminate the problem of tooling and potentially make this greener process more available and usable in manufacturing. We could help overcome the industry’s reliance on older processes that tend to be less sustainable and have greater carbon emissions.
Could you give us more details on Skuld LLC and its mission?
Our stated mission is to overthrow conventional metals manufacturing and save the planet. So we focus on the environmental aspect and process improvements. In practical terms, we aim to actually replace a significant share of metals processes. This may be considered an ambitious goal by most people in the additive world, but we do believe it’s possible.
In order to do so, we’re developing a new process that combines 3D printing with lost foam casting. It is called additive manufacturing evaporative casting (AMEC). The benefits of this innovative method depend on what we are comparing it to. When compared to the current direct metal processes, such as pattern-based techniques, our process has a couple of benefits. First, it is considerably less expensive as a process. One of the problems with additive for metal is the high cost. Because of that, it is really restricted in what parts it can go after as most people can’t pay 10X or 100X for a part. There are benefits to doing that in certain use cases, but it is not going to be widely used if the part costs, for example, US$300.00 a pound instead of US$3.00 a pound. So cost is a big aspect that we’re working on improving. The second area that would greatly benefit from our process is qualification, which is currently a big problem. The resulting material in our process is still casting. It has the same microstructure and the same properties as conventional casting processes even though you don’t have tooling and you can have these complicated geometries that would be difficult to achieve in normal processes.
Could you tell us a little bit about the R&D process that eventually led you to create this new technique? What were some of the challenges and hurdles you faced?
When we first started out, we were just metal people with a casting background. So we didn’t initially start out 3D printing. In the beginning, we were buying prints that existed off the shelf and just testing them to see if they would work. We were different from most initiatives in this area, which come out of universities and labs. We were starting this from the industrial perspective, asking ourselves if we could make this work. Initially it was just trial and error, iterating, and eventually we did, more out of necessity, get a printer and start using it to make our own prints.
My goal is to get to the point in which we can get a CAD file and put it through some kind of software that can evaluate parameters and identify potential problems. Being able to do everything digitally and make sure that it works the first time around. But I think a lot of additive processes, they actually do require some iteration on any new design. There’s always some of that non-recurring engineering costs that you have when you have to iterate to get any specific design to work.
What are some of the current applications of AMEC and what do you envision for the future?
We are exploring a wide variety of applications and materials. We are currently working on tooling parts and different kinds of tooling, including injection molding tooling and drawn over mandrel tooling. Also, legacy parts and prototype designs. We are doing a lot with aluminum because it is the easiest material for us to work with for now, but we’ve done parts in steel, nickel alloys, and copper alloys.
We also have interest from a lot of different industries because of the cost being reduced. I’d say the most active interest is from the industries that are already familiar with additive, such as aerospace, defense, medical – the early adopters of 3D printing technology.
But we do have interest from a variety of industries that want to incorporate additive as long as the costs are favorable.
And what do you envision for the future of Skuld LLC?
We are starting to build equipment as well so that other people can use our process. We recently launched Lightning Metal 16, which allows anyone to make fast, accurate parts. It combines extrusion based polymer 3D printing and lost foam casting and works in aluminum, brass, bronze, and copper. It allows parts to be made in as little as 10 hours with tolerances as good as 0.3%. The process utilizes scrap/ingot and low-cost filament, and the resulting metal has a cast microstructure and properties.

As our final question, we are interested in knowing your perspective on the main challenges for a more widespread adoption of additive manufacturing in the metals industry.
I think there’s a couple of things. The first of them is getting the price down. And that is where we see our process helping as it is cost competitive with conventional manufacturing. Some people may doubt it, but I do believe we should be able to make aluminum parts for US$3 a pound, which is a reasonable goal. The other thing is having enough qualification data to ensure that the additive process and material is going to result in safe, reliable parts with consistent properties.
Conclusion
Sarah’s enthusiasm about metals innovation is reflected in her passion for the creation of more efficient and sustainable manufacturing processes. She recently joined Innovation Crossroads seventh cohort at the Department of Energy’s Oak Ridge National Laboratory (ORNL), which is a recognition of the transformative potential of her work at Skuld LLC.