
Charles R. Goulding and Julia Wallace review the findings of a recent panel discussion on use of AM technology in the US military.
On June 7, 2022 The AM Coalition hosted a webinar entitled “Military Applications of AM: Innovations Changing the Battlefield.” The speakers consisted of CEO of Craitor Daniel Valdes, VP of MELD Manufacturing Dr. Chase Cox, Senior VP and Chief Technology Officer of DMG Mori Advanced Solutions Inc. Dr. Gregory Hyatt, and Additive Manufacturing Technologist at US Army Ground Vehicle Systems Center Dr. Matthew Kelly. They discussed the recent advancements in the use of additive manufacturing in the military, both in manufacturing and repairs in the field. We have previously discussed similar advancements, with the recent contract between ExOne and the Department of Defense.
The Benefits of AM in the Military
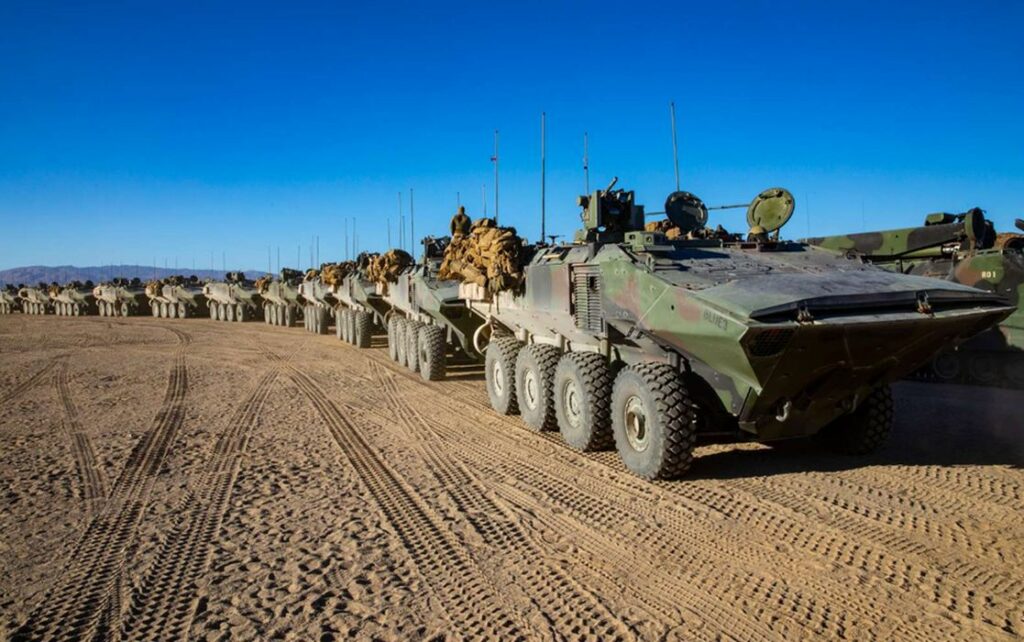
The Marine Corps is the leading force in additive manufacturing across the Department of Defense and has teamed up with Craitor to implement the use of the company’s rugged, portable 3D printers in harsh conditions. Daniel Valdes discussed how closely he has worked with the Marine Corps to design and develop a practical printer that will be used on battle lines to make necessary parts quickly, on-site, and with very little operator management.
A prototype has been tested on the back of a moving Amphibious Combat Vehicle (ACV) and produced a part with no shifting of layers or imperfections other than light stringing. Craitor plans to continue working with the Marine Corps and Department of Defense to increase the use and accessibility of 3D printers across the entire military; it will soon begin work with the Navy and the Army. The company is also currently experimenting with medical usage of its machines.
The Department of Defense has also been working with DMG Mori, one of the world’s largest manufacturers of cutting machine tools, CNC lathes, and milling machines, which started incorporating additive manufacturing into its machines about a decade ago. The hybrid machines produced by the company have incredible precision and can build at virtually any angle, allowing the user to manufacture parts of unusual complexity. The mix of subtractive and additive manufacturing in one device also makes repairing parts incredibly efficient, allowing the entire process to be done at once.
These machines are also capable of changing the alloy used as “ink” while it is building to address topology-specific modes of failure. For example, NASA worked with the Department of Defense to create a monolithic build of engine parts using multiple alloys, accommodating thermal and pressure requirements.
Jointless Hull Project
Dr. Chase Cox and Matthew Kelly discussed the Jointless Hull project, in which additive manufacturing will be used to print the entirety of the hull of a combat vehicle. Matthew Kelly is the current project lead. This method of production would be much faster and more cost effective than traditional methods; a prototype of the printer was able to print a hull out of aluminum in about 30 hours, as opposed to having to wait several months for one to be forged and shipped. A jointless hull is also much stronger than a traditional one, with fewer weak points.
Two machines are being developed for this project: a hull-scale tool to be located at Rock Island Arsenal, IL, for components 20’ x 30’ x 12’, and a subsection tool at the GVSC Advanced Manufacturing Commercialization Center in Troy, MI, for components 3’ x 3’ x 3’. The larger machine will be operational by January 2023, and the smaller by October 2022. Both will have hybrid additive and subtractive capabilities and are being developed in partnership with MELD Manufacturing. They will use additive friction stir deposition to print high-strength alloys in open atmosphere
Although the project is called Jointless Hull, these machines are not limited to producing parts for tanks and will be used to produce a multitude of large- and small-scale parts as needed for the Army and across the Department of Defense. This is a promising development in overcoming supply chain issues that the military is currently facing along with the rest of the United States. Matthew Kelly expressed his excitement that the AM Forward Initiative reinforces the belief that additive manufacturing will help resolve this issue both in and out of the military.
Obstacles
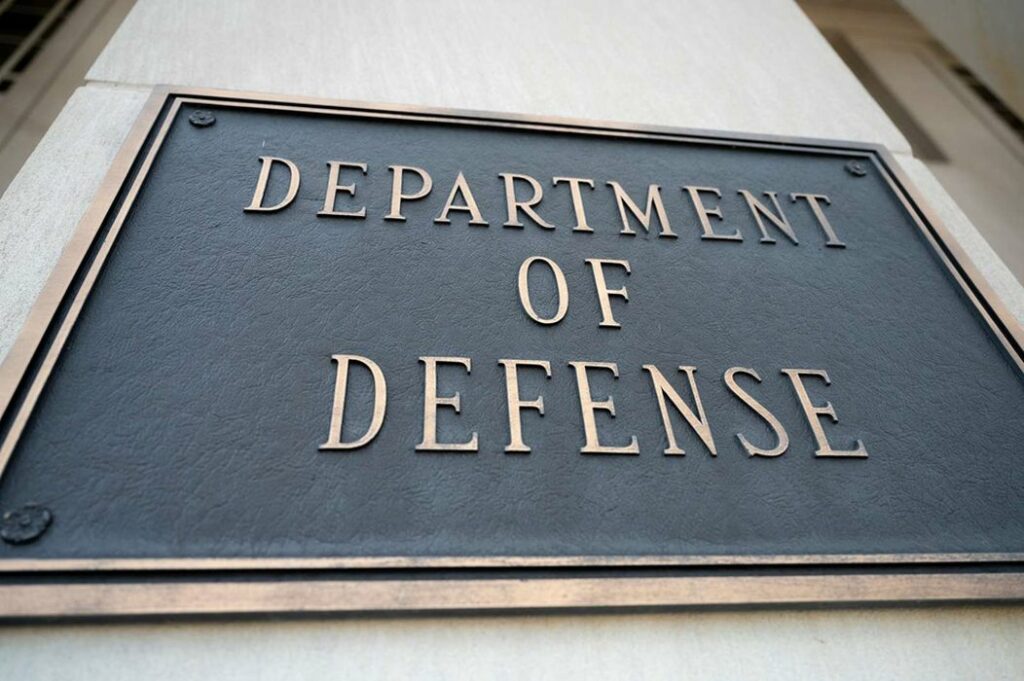
The biggest issue faced when trying to spread this technology is the qualification of parts, according to Matthew Kelly, and he says those pushing for the use of additive manufacturing must continue to show its usefulness and efficacy in practical applications. Daniel Valdes agrees that the lack of understanding and trust in these machines from the Department of Defense is a major hurdle since although some services are now being approved, many commanders are hesitant to put them into action. Dr. Hyatt emphasized the need to fund academic work to define the testing of these new complex materials, and that the Department of Defense suppliers need to invest in additive manufacturing and train their design engineers in this technology.
Future Advancements
Despite the obstacles faced by the additive manufacturing industry today, the speakers were very hopeful for the future of its use across the Department of Defense. Dr. Cox and Dr. Hyatt expressed that they think there will be significant progress in the qualification efforts in the next 5 years. Dr. Chase Cox also said that the possibilities of what can be done is “limited only by the interest and need for technology that doesn’t exist today,” and that we must detach these needs and possibilities from what is possible now. He explained how the geometries, scales, and materials that are able to be used now are different from what was possible just 5 years ago, so 5 years in the future could hold completely new aspects of design and build as well.
The Research & Development Tax Credit
The now permanent Research and Development (R&D) Tax Credit is available for companies developing new or improved products, processes and/or software. Eligible costs include U.S.-based employee wages, cost of supplies consumed in the R&D process, cost of pre-production testing, contract research expenses, and certain costs associated with developing a patent. As of 2016, eligible startup businesses can use the R&D Tax Credit against $250,000 per year in payroll taxes.
3D printing can help boost a company’s R&D Tax Credits. Wages for technical employees creating, testing and revising 3D printed prototypes can be included as a percentage of eligible time spent for the R&D Tax Credit. Similarly, when used as a method of improving a process, time spent integrating 3D printing hardware and software counts as an eligible activity. Lastly, when used for modeling and preproduction, the costs of filaments consumed during the development process may also be recovered.
Whether it is used for creating and testing prototypes or for final production, 3D printing is a great indicator that R&D Credit eligible activities are taking place. Companies implementing this technology at any point should consider taking advantage of R&D Tax Credits.
Conclusion
The use of additive manufacturing already demonstrates great benefits to military applications, and the future likely holds many more. While there are currently many obstacles in implementing 3D printers in the Department of Defense, strides in the right direction are already being made to overcome these and increase the use of these machines.