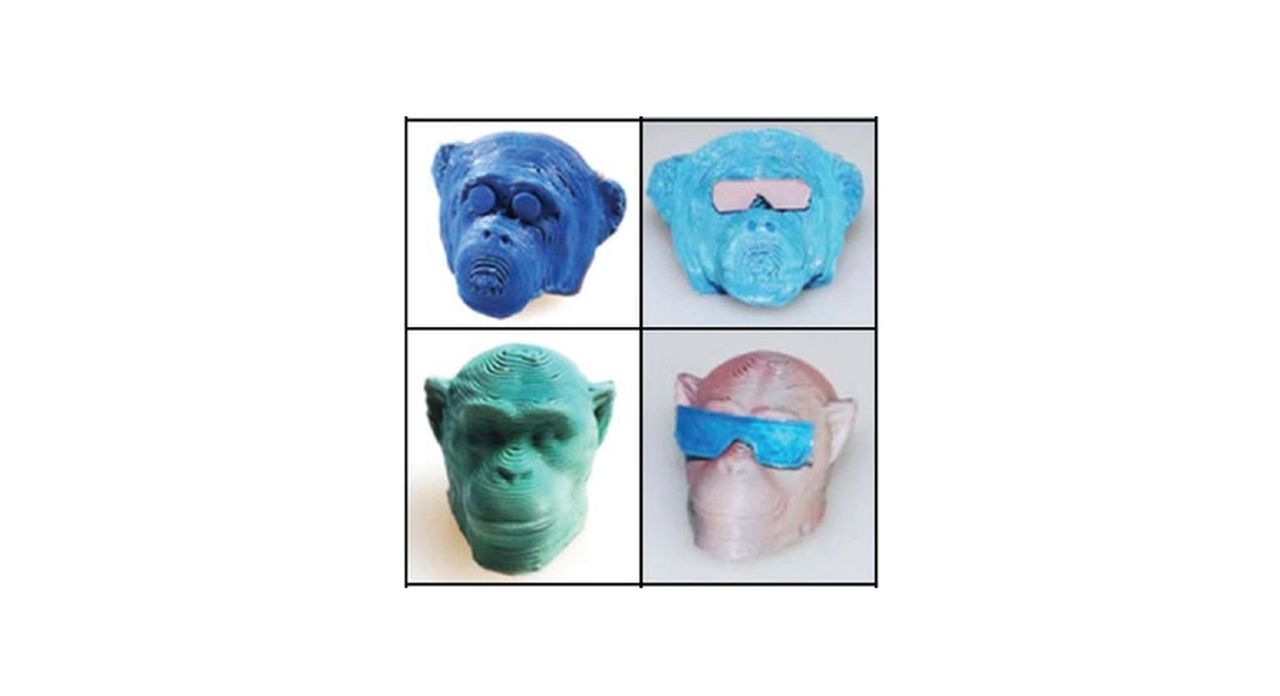
Researchers have developed a method of 3D printing mechanochromic parts.
Hold on, what exactly is āmechanochromicā?
Itās a form of iridescence, where the color shown depends on the mechanical stress currently experienced by the material. This property, seen in nature in butterfly wings, chameleons and similar creatures, varies the color appearance of a surface.
While creatures may use iridescence for protection or mating purposes, there are plenty of industrial uses. A simple example might be a pressure sensor that flips color when a threshold level is reached.
Itās also possible to use stimuli other than mechanical stress for this effect, including electrical fields, pH, magnetism, etc. Thus you can well imagine a massive number of potential applications for this property.
The approach is to somehow create polymer-based core-shell-particles (CSP) that are designed to exhibit these properties.
There are several techniques for producing this type of material, but up to now none have successfully used 3D printing. This is due to thermal issues, as the researchers explain:
āA limiting factor for extrusion-based 3D-Printing of mechanoresponsive polymers is the lack in stability against high temperatures and shears of the mechanophores during processing. 3D-printing of particle-based materials exhibiting structural color would therefore pave the way to a new generation of stimuli-responsive materials and complex structures, overcoming this limitation. Beyond that, structural colors are advantageous to mechanoluminescent dyes or pigments, as they exhibit more vivid color impressions, are environmentally friendly and do not fade or bleach over time.ā
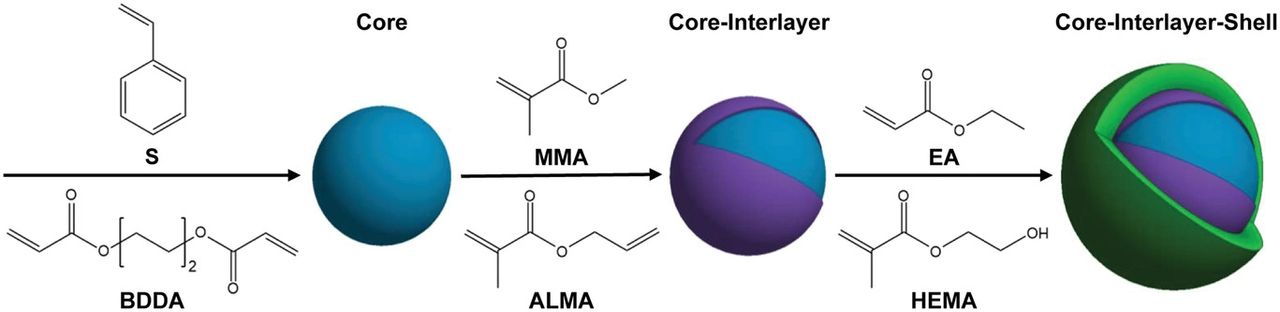
The researchers were able to create CSPs that could be 3D printed through the use of a āstarved-feed emulsion polymerization techniqueā, and successfully 3D printed on a hybrid direct-ink writing / FFF system. They explain:
āThe presented objects were printed on a DIW-FFF-hybrid printing system and combine iridescent mechanochromic structural color, as known from polymeric opal films, with a high level of detail, as known from commercial 3D-printing. By slightly adjusting synthesis parameters, the color of the final product was easily tunable. We envision our stimuli-responsive system as a promising candidate for the fabrication of smart optical sensors, anti-counterfeiting applications and other advanced optical devices.ā
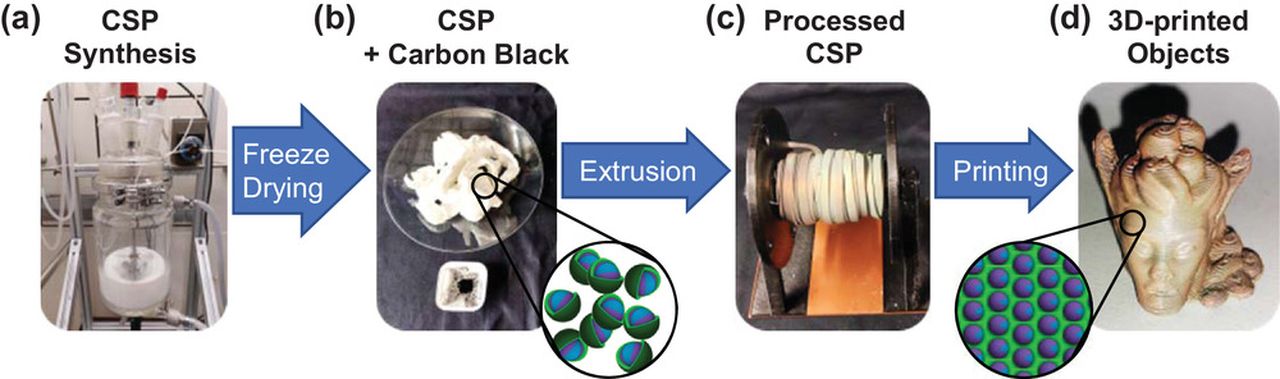
The engineered CSPs were then mixed with carbon black, and heated/extruded through a DIW 3D printer, the Saarpricom Delta UpSD.
After tuning the print parameters, the researchers were able to successfully 3D print a variety of objects using the material and printer. Interestingly, a low temperature of only 140C was used for extrusion.
The print results showed āvivid structural colorsā, as predicted.
The implications of this discovery are profound. It may be that this approach could be commercialized to enable 3D printing of not only vivid colors on prints, but also to embed sensors of all kinds directly into part structures.
The researchers conclude:
āWe envision herein presented methods to open new avenues for a variety of applications for CSP. In the field of deformation sensing, established processing methods were limited to round or rectangular 2D-structures with restricted variability of film-thickness. Using our 3D-printing-based approach, the geometry of the sensor is effortlessly tailorable to the specific problem, while mechanical properties are adjustable. For anti-counterfeiting materials or optical display technologies, state-of-the-art methods rely on the use of a mask and post-processing for the implementation of logos, signs or text. 3D-printing not only removes this time- and resource consuming steps, but also offers a broad freedom of design and the possibility of mass customization.ā
Via Wiley