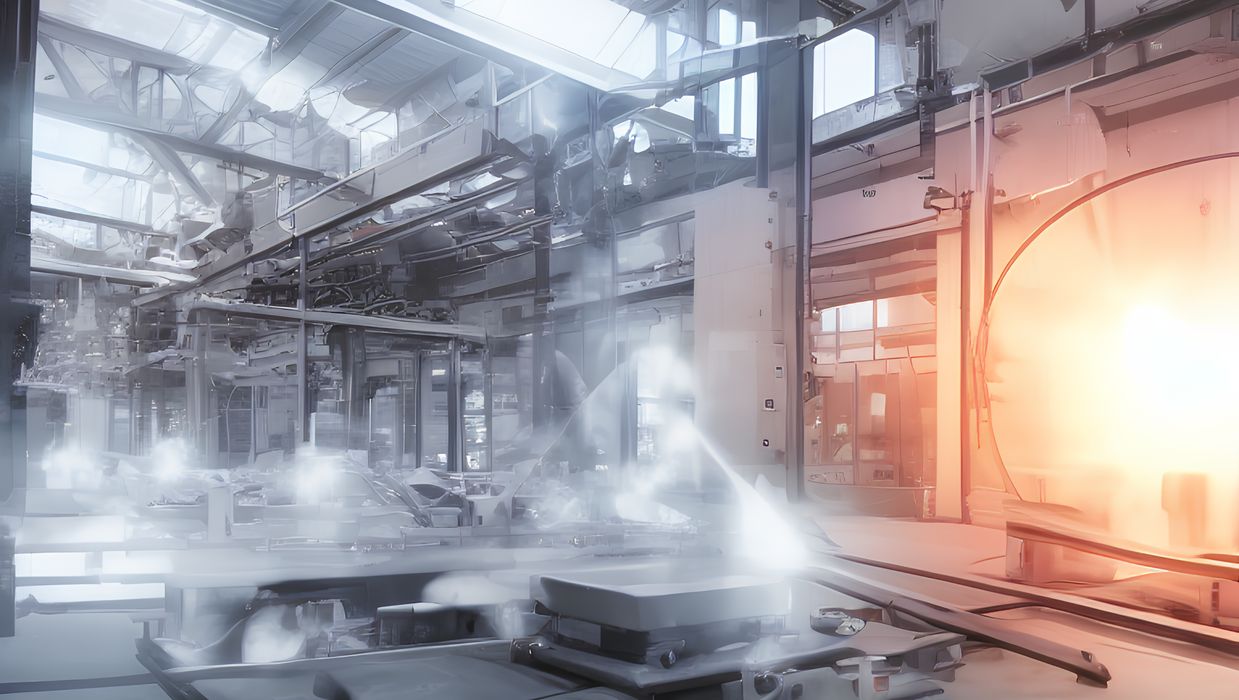
Small steps forward are taking us to an additively manufactured future.
A recent industry survey by Materialise highlighted several key trends.
Materialise believes the industry has largely shifted from āwhy 3D printingā to āhow to do itā. They report that in the US, some 60% of respondents are now using the technology to produce end-use parts, while strangely that figure is only 43% in Germany and an even lower 36% in Japan.
Nevertheless, the idea of producing end-use parts with additive processes is clearly catching on, in spite of many challenges. Materialise reports that 98% of respondents āexperience challenges and barriersā when adopting 3D printing technology. Almost half of their respondents intend on doubling their use of the technology going forward.
This surveyās results ring true to me.
Roboze and ARES Modena
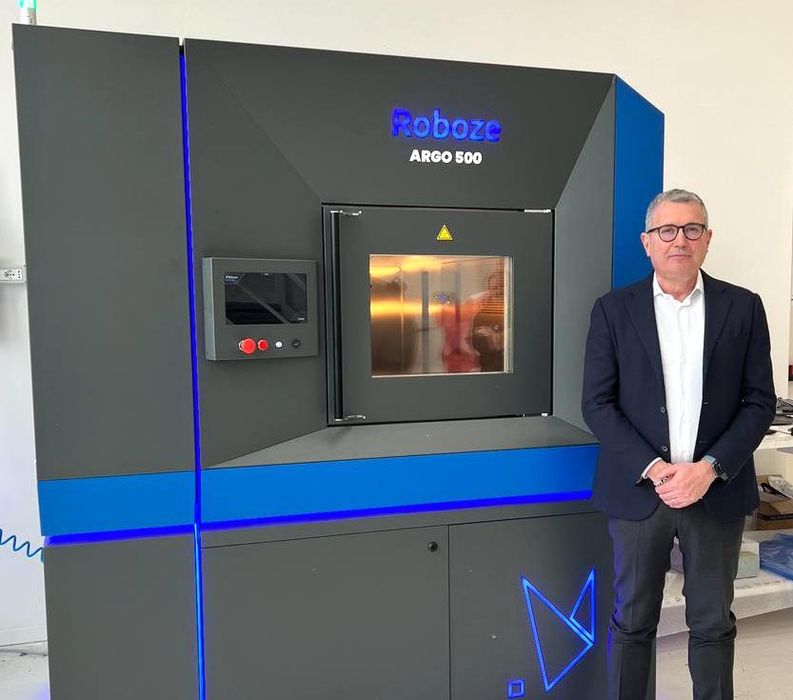
An example of this phenomenon was recently presented by Roboze, which sold one of their huge production ARGO systems to ARES Modena, an Italian manufacturer of one-off or limited edition sports cars.
They intend to use the system to produce high-temperature custom parts that can be used in their vehicular products. Roboze explained:
āAs a result of crucial changes in the automotive world, with a strong and growing desire for individual solutions, flexibility and tailored customization, integrating an additive manufacturing solution such as Roboze’s can become strategic and accelerate innovation and new productivity frontiers. Indeed, Roboze designs and manufactures industrial 3D printers that are helping manufacturing companies around the world solve common problems related to process repeatability, precision, and the production of custom parts with high-performance polymers and materials.ā
This is true for not only Roboze equipment, but also for many other producers of industrial 3D printing gear for different applications.
However, there is a ratio that needs to be discussed.
Mass Production vs Customization
Historically, virtually all parts were mass produced, and one had to find ways to use them for the application at hand. The application fit the parts, so to speak.
But with the advent of additive processes, another possibility emerged: customization. It was possible with 3D printing to efficiently produce one-off parts that would be used for only a single application. In other words, the parts fit the application, the reverse of the mass manufacturing scenario.
So thereās a kind of ālineā between mass manufacturing and customized parts. The position of this line, I believe, is entirely dependent on the willingness of the public to accept the notion of customized solutions.
During our lifetimes we have been exposed almost entirely to mass manufactured products and only very rarely have witnessed true customized solutions. My prediction is that this exposure will increase over time, and our collective expectations about parts and products will gradually shift towards customized solutions, which are clearly better.
Itās just that they are more expensive, at least for now.
Via Materialise and Roboze