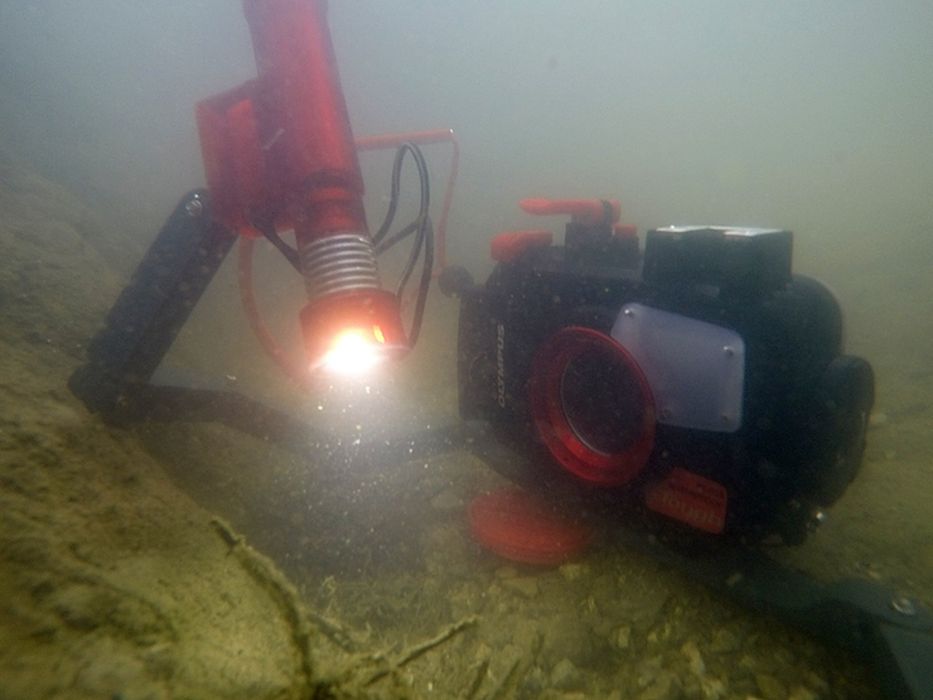
Charles R. Goulding and Matt Selman consider the benefits of using 3D print technology to produce watertight cases for underwater devices.
Underwater electronics are becoming more and more popular to enable the exploration and understanding of vast water bodies. If done correctly, 3D printing has the potential to fulfill the demand for such electronic devices. It can be used to create custom electronic housings for divers, custom parts for remote-controlled submarines, boxes for various measuring equipment, and many other applications.
In general, the most efficient watertight model is a hollow container that is round and has no openings or moving parts. This is because it can be printed as one continuous piece, so the chance of imperfections that cause leaks is greatly reduced. The problem with this method is that it is not practical because the applications that this would be useful for have moving parts and require openings. Instead, a sealable container can be 3D printed to achieve the functionality required for underwater applications.
3D printing a sealable container that is watertight is a difficult task that will require prototyping and testing to get right. Just one minuscule opening or fault in the design of the 3D print can result in the destruction of the enclosed electronics.
One of the most important aspects to consider is the thickness of the walls. Typically, 2-3 mm is sufficient. However, the walls may have to be thicker than that if the product is intended to go deep in the water due to the increased pressure.
Another aspect that must be considered is the print settings and infill of the print. While it is not as important for shallow depths (low pressure), the walls have to be as solid as possible to withstand greater depths. The walls best withstand the higher pressure with a high number of perimeters and with the highest infill percent possible. 0% infill is when the object is completely hollow, and 100% infill is when the printed object is completely solid. While 100% infill is ideal for watertight models, the price of filaments can be expensive and printing with 100% infill can be costly. Therefore, testing with lower infill percentages and alternative numbers of perimeters is sometimes necessary to find the best settings for a particular product.
While the material is not as influential as the print settings, wall thickness, or infill percentage, products intended for great depths and pressure require more consideration regarding the print material used. This is because stronger materials are needed to withstand the pressure and because they may require post-processing in the form of applying an epoxy resin.
The application of epoxy resin is essential in sealing the model to eliminate any leaks caused by faults in the printing, usually along the seams of openings, but also along the entire surface to ensure there are no gaps between print layers.
The best material to use are filaments that are sufficiently strong and that have the most effective layer-to-layer adhesion properties. Many options exists, but the choice also depends on the capabilities of the 3D printer being used.
The Research & Development Tax Credit
The now permanent Research and Development (R&D) Tax Credit is available for companies developing new or improved products, processes and/or software.
3D printing can help boost a company’s R&D Tax Credits. Wages for technical employees creating, testing and revising 3D printed prototypes can be included as a percentage of eligible time spent for the R&D Tax Credit. Similarly, when used as a method of improving a process, time spent integrating 3D printing hardware and software counts as an eligible activity. Lastly, when used for modeling and preproduction, the costs of filaments consumed during the development process may also be recovered.
Whether it is used for creating and testing prototypes or for final production, 3D printing is a great indicator that R&D Credit eligible activities are taking place. Companies implementing this technology at any point should consider taking advantage of R&D Tax Credits.
Conclusion
The 3D printing of watertight closeable models can enable underwater functionality for various products. The normal advantages of 3D printing, such as providing flexible designs that are cost-effective and that can be printed on demand, make it an advantageous alternative for the production of watertight models going forward.