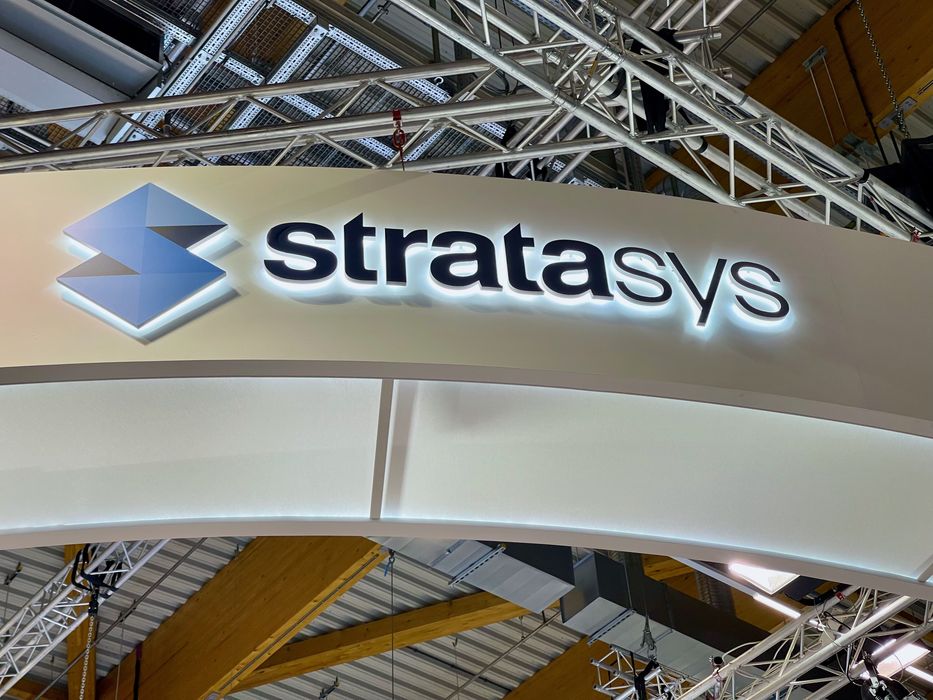
At Formnext 2022, Stratasys featured a product they don’t even sell.
The company had one of the largest stands at the show, and in one of the prime positions at the entrance to the larger hall. You couldn’t miss it.
In their enormous stand they displayed all of their current products, ranging from systems for FDM, to PolyJet, to P3, to SAF. Both machines, materials and processes were on display, with plenty of staff running around to explain all of the above.
But in the back there was a huge area dedicated to something new. It looked like this:
A robotic system, and there was more behind what you see in the image. The robotic system was intended to pick up completed prints from the Origin systems on the sides, and then carry them toward post processing stations beyond. There was a near-complete set of stations required, although for an individual customer the steps would vary depending on needs.
The idea here is that when these 3D printers are acquired for production purposes, they do something interesting: they make a lot of part quickly.
Normally a completed print is worthy of a small celebration. It’s carefully removed from the printer by the operator, and then manually taken through whatever post processing steps are required. Hooray!
But that approach just doesn’t work with production. It’s ok when you produce a few tens of parts per week, but what happens when you have 100,000 parts in a week? How can you possibly process them all? How can you keep track of them?
This issue isn’t one really solvable by a 3D printer, but it affects 3D printer sales.
Consider the scenario where a manufacturer is contemplating getting into 3D print technology. They examine different machine and material options, and come to a selection that works for their product.
But then they realize they would end up with, say, 87 production printers on the factory floor producing a total of 24,332 objects per day. To handle them you’d need more operators, perhaps many. They’d have to be trained, and need space, personnel management, etc.
That’s a rather large technical and management undertaking, and it turns out this actually scares off some manufacturers from using AM technology: when scaled up, there’s too much manual effort required.
This problem has been recognized by some players in the space, and we’re increasingly seeing post processing automation solutions of various types.
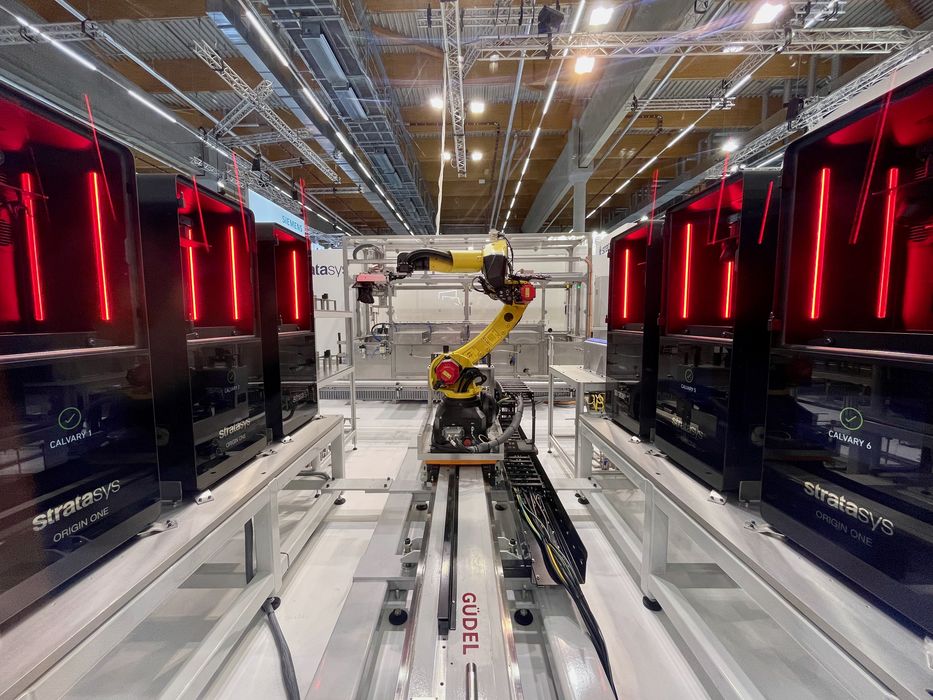
In the case of Stratasys, they contracted with a robotics system integrator to build a “demonstration” of how a four-step post processing sequence could be implemented. The robotic system shown would remove plates from the printers, take them to the wash station, etc.
The interesting part here is that Stratasys doesn’t sell such an integration; it’s entirely from a third party.
So why display it at a major trade show?
The answer is confidence. Stratasys wanted to show passing manufacturers that it is indeed possible to automate the otherwise standalone 3D printers sold by the company. If a manufacturer purchased a series of machines, they could be confident an automation solution could be made to minimize manual labor required, once seeing the demonstration.
That’s a factor some 3D printer manufacturers don’t address, and you can bet many manufacturers see their equipment as more problematic to implement in a factory setting than beneficial.
I believe Stratasys is taking the right approach here to provide visual evidence of 3D print scalability — in all dimensions.
Via Stratasys