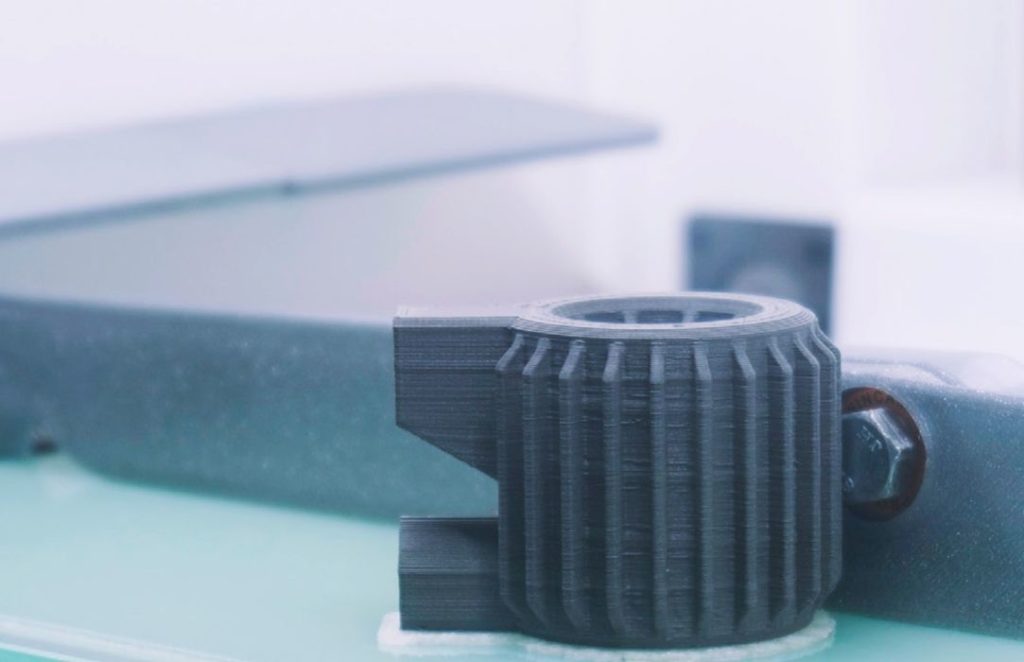
3DQue announced the results of an internal study exploring ways to inexpensively 3D print metal objects.
The Vancouver-based company is known for their 3D print automation solution, “Quinly”. This is a replacement print surface kit that is chemically and thermally designed to automate print operations. Basically, the surface holds prints tight when hot, but completely releases them when cooled.
3DQue has leveraged this capability into an automation solution, where arrays of inexpensive 3D printers equipped with the VAAPR technology can, in parallel, produce large quantities of parts with little to no human intervention: completed parts drop off into collection systems when cooled, because the 3D printers are oriented sideways or at an angle.
The company has been experimenting with 3D printing of engineering materials on inexpensive desktop 3D printers, such as the Ender 3. For example, they were able to successfully 3D print polycarbonate on a slightly modified Ender 3 recently.
It turns out they’ve also been experimenting with metal 3D printing, again on relatively inexpensive desktop 3D printers. This time rather than using the Ender 3, they’ve been testing this approach with an Ultimaker S5 professional 3D printer.
Their approach is to equip the S5 with a Quinly kit and 3D print metal objects using BASF Ultrafuse 316L steel filament. This is a filament made from 316L steel powder mixed with a binder. Once the part is 3D printed, it is placed in a sintering oven to burn out the binder and sinter the powder together to form a solid object. 3DQue said:
“Published results for sintered Ultrafuse 316L indicate tensile strength is roughly equivalent to solid steel in the X/Y direction, and is only 10% weaker in the Z direction. Post- sintering, parts are 98% solid.”
This is a process that’s been done before, but the difference here is that the printing process can be automated using the VAAPR print surface. Just like 3DQue was able to automate the production of thermoplastic parts using an array of Quinsy-equipped Ender 3 printers, they have proven they can do the same with the S5. They explain:
“3DQue’s initial metal printing tests show that automation with Quinly reduces labor and equipment costs; provides more flexible, on-demand production; is more sustainable than centralized mass production; and adds almost no labor when scaling production. Quinly makes metal 3D printing both affordable and scalable.”
But is this a way to reduce the cost of metal 3D print production? We know that traditional metal 3D printing can be enormously expensive due to the cost of materials, staffing, facility, post-processing and more. Although powder bed fusion metal 3D printing approaches do work very well, they can be so expensive that only certain applications are financially feasible.
Some 3D printer manufacturers have attempted to circumvent those costs by developing less expensive metal 3D printing solutions. Two examples are Markforged’s MetalX and Desktop Metal’s Studio System, which use 3D printing processes that are far less expensive than PBF.
It seems that 3DQue believes they have a way to produce metal parts of similar quality using an even less expensive approach. They explain:
“3DQue printed a number of test parts using the Quinly automated Ultimaker S5. With Quinly, part costs dropped 63% compared to Desktop Metal’s BMD printing.
Desktop Metal’s binder-jetting production system has a reported capacity of 63,230 parts per year (BMW water wheel). Tests showed that fourteen Quinly-automated Ultimakers would provide similar capacity, cost 10x less, could be housed in 30 square feet of shelving or placed close to end-users.”
How do they calculate the “10X” cost? They explain:
“The Ultimaker S5 is a popular industrial 3D printer that uses fused filament fabrication (FFF) which is similar to Desktop Metal’s bound metal deposition system (BMD). Preliminary results from testing shows that with Quinly the capital needed to start high volume printing drops 90%, decreasing initial investment from $60,000+ for a BMD printer to the $6,000 required to fully automate an Ultimaker for high volume metal printing.”
This is an interesting development, as it seems to offer yet another path to even more inexpensive metal 3D printing. It’s also a very big step for tiny 3DQue to compete directly with the likes of Desktop Metal, currently in position three on our Biggest in 3D Printing leaderboard.
Via 3DQue