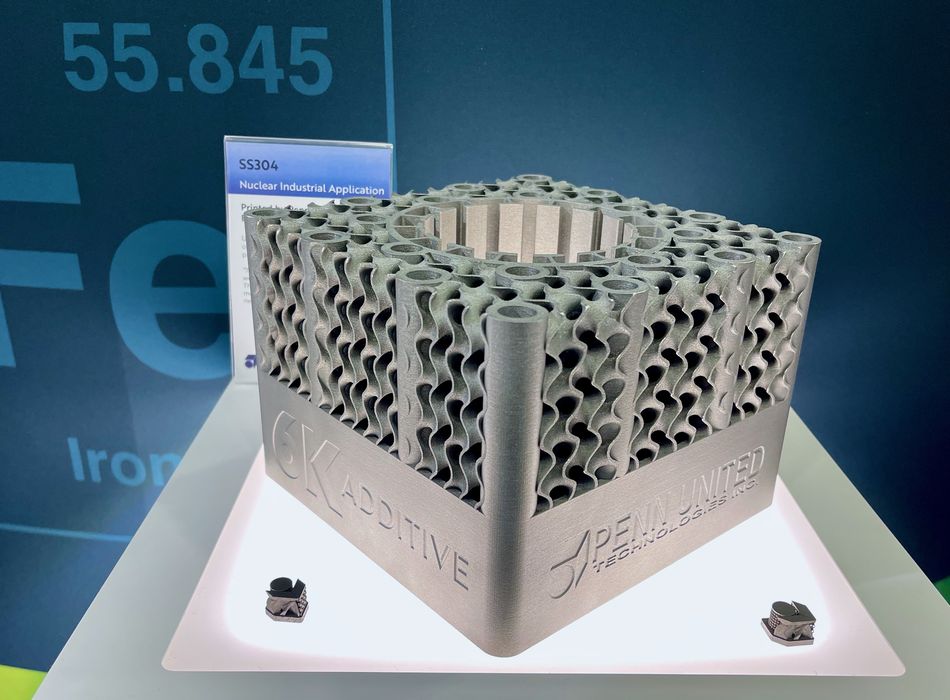
6K Additive is yet another 3D print company that’s working diligently on attaining a sustainable state.
6K Additive doesn’t produce 3D printers, but they do make fine metal powder for industrial 3D printing. The company uses a revolutionary new technique for powder production they call “UniMelt”.
UniMelt is quite different from typical powder operations that tend to be surprisingly wasteful. The common method for making these powders is to shoot some raw metal into a plasma, where the material liquifies into droplets. These droplets then freeze solid and fall out, where they are collected and sorted.
This is where the problem occurs. The particles generated by the plasma approach have non uniform sizes and shapes. Ideally, consistent metal 3D printing requires identically-sized particles that are perfectly spherical. The powder production process basically sifts through the generated particles to pick out the ones that meet the criteria. Unfortunately, the vast majority of the particles produced don’t. 6K Additive claims there can be as much as 90% waste material in these processes.
Certainly some of the waste powder can be re-injected into the process, but some will be not be reusable at all. The re-injected material might eventually form usable particles, but in effect it would be taking multiple runs through the plasma to obtain those particles. In fewer words, this is a rather inefficient process.
6K Additive’s approach is quite different. Instead of using a high temperature plasma, they instead use a chamber with highly tuned microwaves to heat up and melt metals in a far more controllable manner. UniMelt is able to reliably produce particles with predictable size and shape, ideal for 3D printing applications.
Again, in fewer words, UniMelt is vastly more eco-friendly than typical plasma production processes.
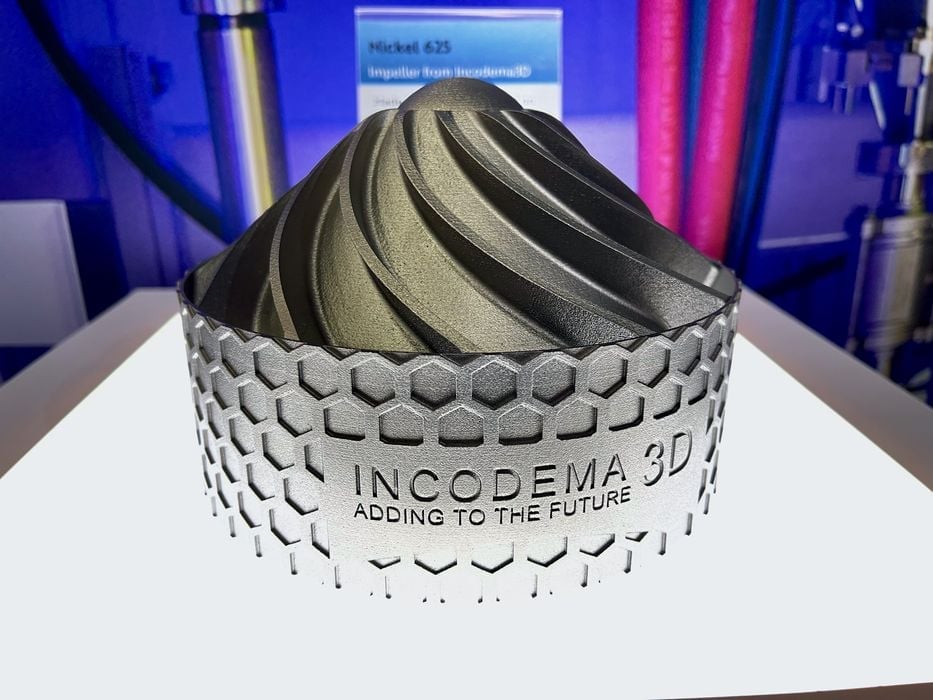
Even better, UniMelt is able to receive and process recycled materials far more effectively than other processes.
But is this really true? 6K Additive set out to more formally define these savings. They engaged an independent agency (Foresight Management) to undertake a “Lifecycle Assessment” for the production of certain metal powders by the UniMelt process.
Two of these studies have now been completed and published, for Nickel and Titanium. Foresight Management describes their methodology:
“Sphera’s GaBi software for life-cycle assessments is a sustainability software product that empowers business to perform life cycle assessments by providing rich datasets from across the globe that detail the costs, energy and environmental impact of sourcing and refining every raw material or processed component of a manufactured item.”
The investigation looked at raw material extractions, transportation of raw materials, manufacturing of the product, and distribution of the product, but not what happens to the powder after it’s been delivered to clients. That’s another analysis for someone else to do.
The idea was to determine the total environmental cost of 6K Additive’s process to produce 100kg of powder material and compare it to other methods of producing the same type of material. Materials, energy, water and other factors were tallied. This is a flowchart of the activities under investigation:
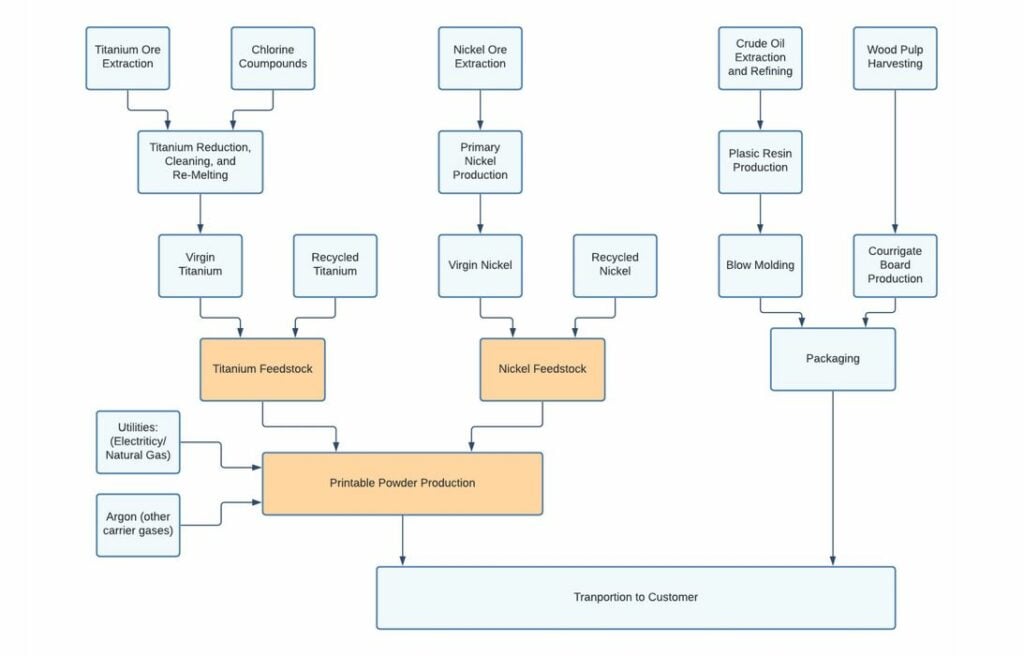
The study even included the cardboard packaging of the product once manufactured, to give you an idea of the depth of detail for this work.
The results are a little challenging to interpret, but measurements of the following were determined:
- Global Warming Potential (GWP 100 years) [kg CO2-eq] – IPCC (AR4)
- Acidification Potential (AP) [kg SO2-eq] – TRACI 2.1
- Photochemical ozone creation potential (PCOP) [kg O3-eq] – TRACI 2.1
- Eutrophication potential (EP) [kg N eq] – TRACI 2.1
- Ozone Depletion Air [kg CFC 11-eq] – TRACI 2.1
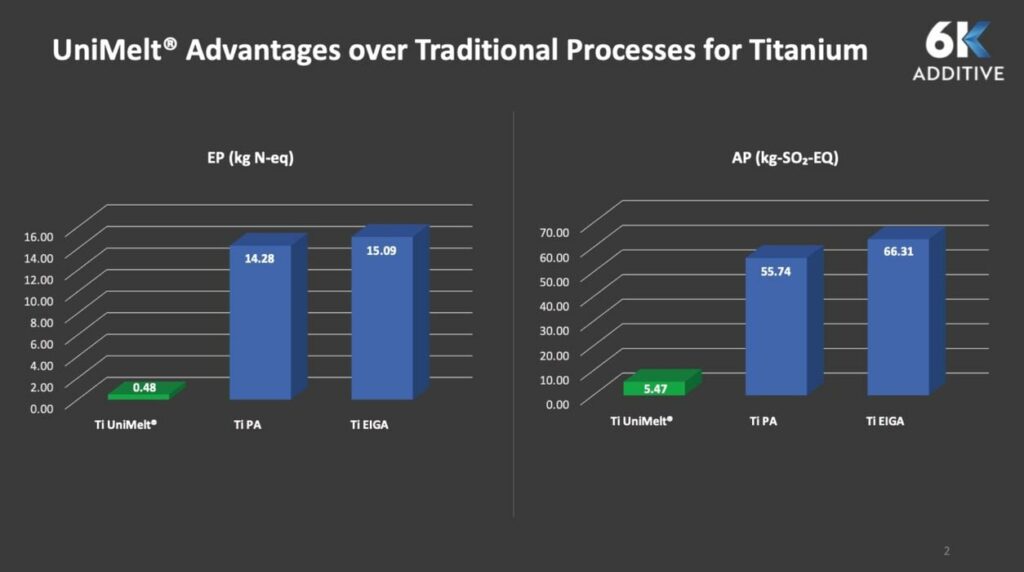
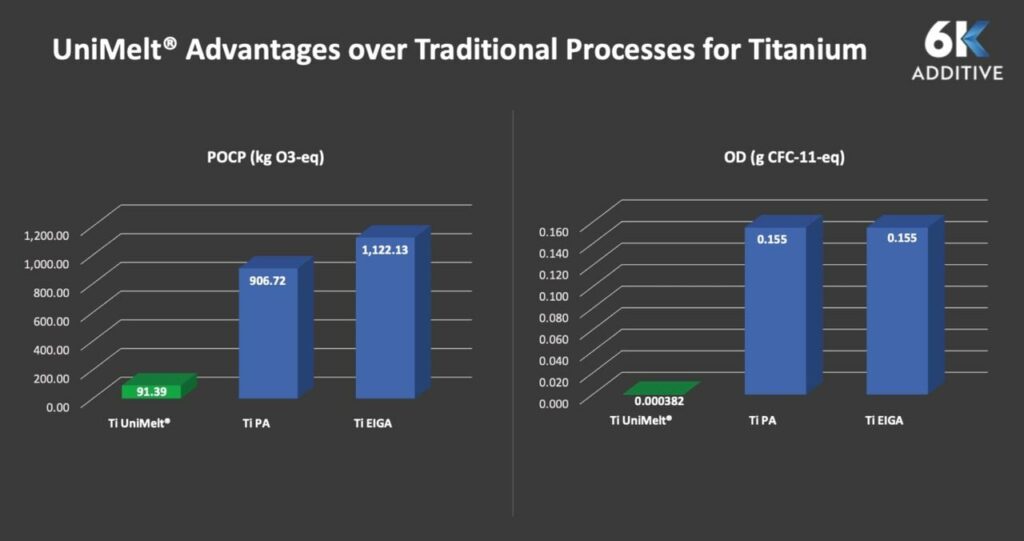
As you can see in these charts for titanium production, UniMelt has vastly less environmental impact that traditional powder-making processes. Foresight Management writes:
“6K’s UniMelt process reduces all environmental impact categories included in this study for Titanium Powder Production. The most impactful aspects of the UniMelt process is how it uses a recycled feed stream and its lower impactful powder production. Raw extraction of virgin material is by far the most environmentally impactful stage of production. The Ti PA and EIGA processes had a 20% virgin feedstock, even at this ratio, it still accounted for 17% of the energy and carbon. 6K’s UniMelt ability to use a fully recycled feed stream greatly reduces all impacts in the Cradle-to-Gate boundary.”
That’s quite impressive, and the nickel report is quite similar.
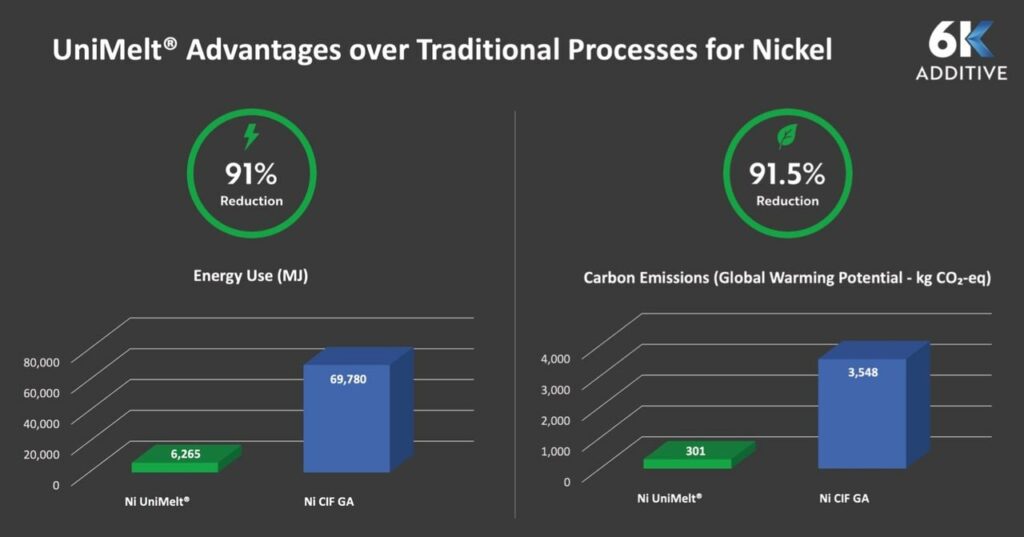
Some companies in the 3D print space have delved deep into the world of sustainability, and 6K Additive is definitely one of them. With these formal lifecycle reports they can prove beyond a doubt their process is indeed far more sustainable.
Let’s see if other companies take this formalized approach for defining and measuring sustainability.
Via 6K Additive